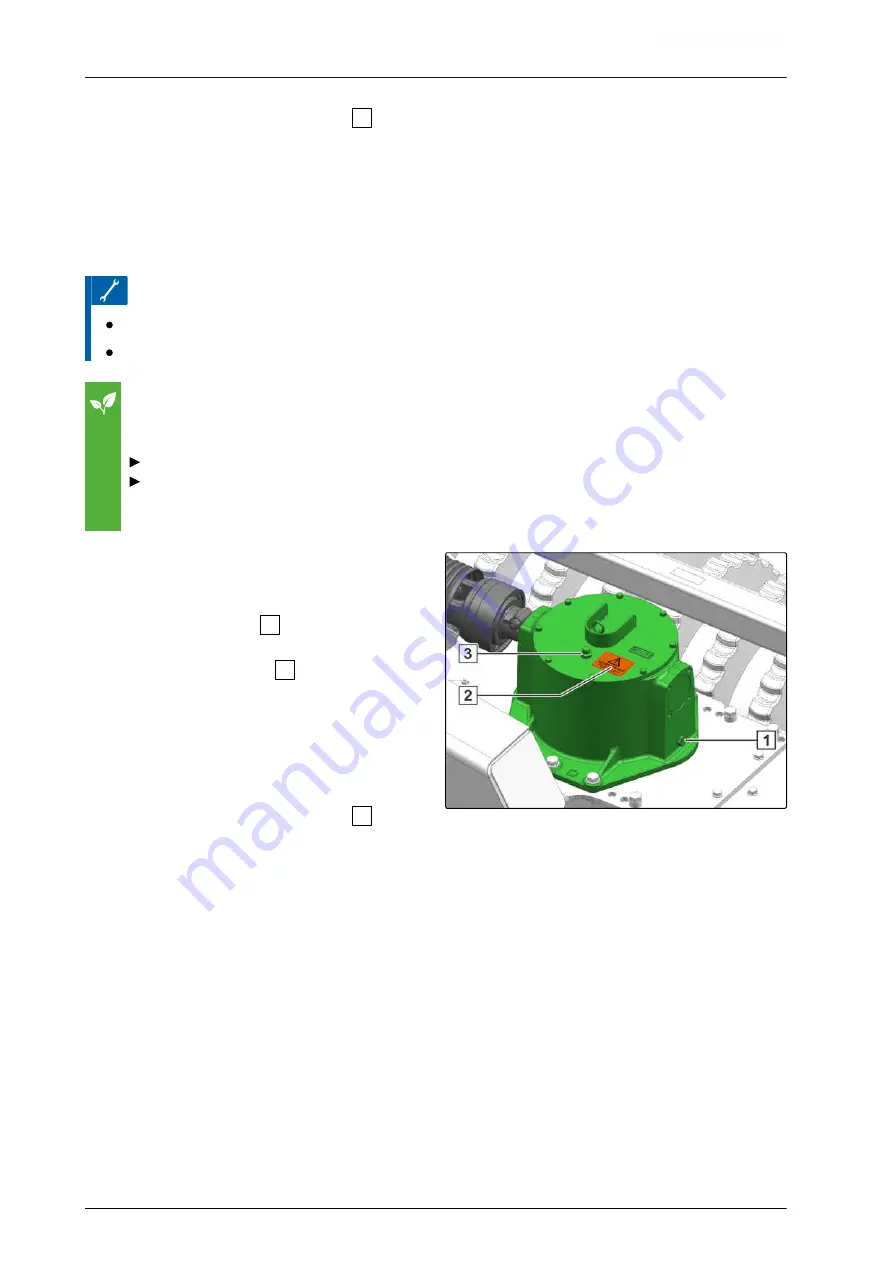
6.
Refill oil according to the specification
3
and the
technical data.
7.
install the refill screw with a new sealing ring.
9.1.11 Changing the oil of the angular gearbox
INTERVAL
After the first 50 operating hours
Every 500 operating hours
ENVIRONMENTAL INFORMATION
Danger due to escaping oil
Collect any escaping oil.
Dispose of oil removal material in an
environmentally friendly manner.
1.
Place a suitable container below the oil drain
opening.
2.
Remove the oil dipstick
3
.
3.
Remove the oil drain plug
1
.
4.
Clean the chip catching magnets on the oil drain
plug.
5.
Install the oil drain plug with a new sealing ring.
6.
Refill oil according to the specification
2
and the
technical data.
7.
install the oil dipstick with a new sealing ring.
CMS-I-00003041
CMS-T-00004136-A.1
9 | Repairing the machine
Maintaining the machine
MG6750-EN-II | C.1 | 21.07.2021
92
Summary of Contents for KG 6002-2
Page 1: ...Original operating manual Rotary cultivator KG 6002 2 SmartLearning www amazone de...
Page 6: ......
Page 117: ......