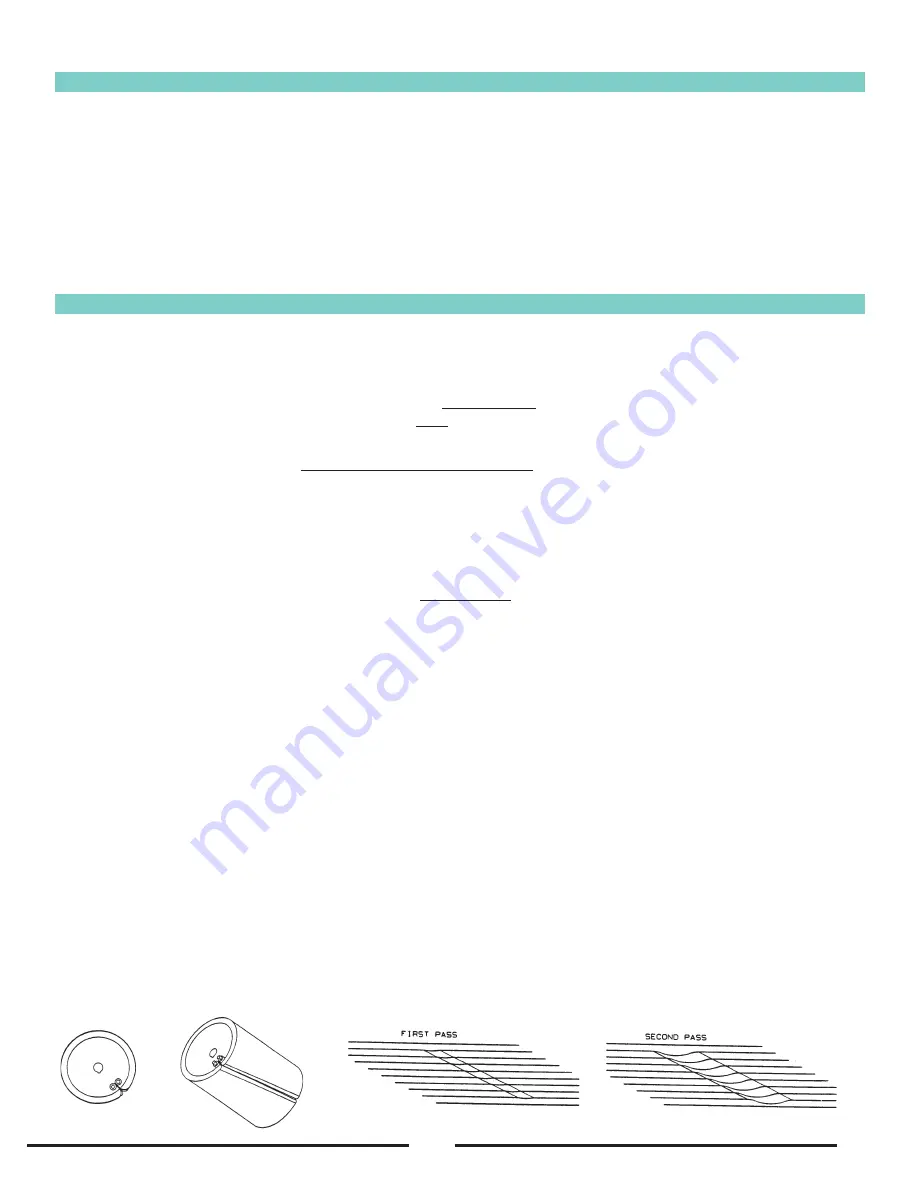
8
Machine Set-Up
Chatter - Wave Prevention
American Sanders are designed and manufactured to the most rigid tolerances. However, after a finishing cut it is possible to see “chatter” or “waves”.The
best guarantee to remove the chatter is to finish the floor with a rotating horizontal sander, such as American Sanders’s Sander 16.
To minimize chatter when using a belt or drum sander the following steps should be taken:
1)
DRUM PAPER... insure the paper is secured in the slot, but not too tight. Paper that
is too tight will force the drum slot wider, leaving a “slot mark chatter” on the floor.
2)
DRUM MARKS... are caused by the operator lowering the drum to the floor without forward traverse. These marks should be
removed by cutting at a 45 degree angle to the mark. Cutting at the mark while maintaining the same
path will only increase the mark depth and width.
3)
UNEVEN WALKING PACE... can leave lengthy “waves”. The machine cuts more material during the slower pace. Pay
particular attention to a steady, even pace.
4)
EXCESSIVE LIGHT CUTS... may reveal high spots on the paper/contact wheel and cause chatter. Take a heavier cut and
increase the pace.
5)
DEBRIS... lodged between the paper and the drum will leave chatter. On a belt sander, debris may be adhered to the drum.
Insure the drum is clean and free of debris before placing the paper on.
6)
SANDER PAPER QUALITY... may vary. Belt seams can be thicker on low quality paper and cause chatter. Use only
American Sanders specified sandpaper.
PROPER CARE OF YOUR MACHINE CAN MINIMIZE CHATTER AND WAVES
1)
V-BELTS... can cause vibration and chatter if they are of low quality. Use only belts specified by American Sanders.
2)
TRUCK AND CASTER WHEELS... with flat spots, out-of-roundness, or debris adhered to their surface can cause “waves” or a
“chatter effect”. Always clean and inspect all wheels before starting to sand, and before the
finish cut. Replace or true the wheels if found to be out-of-round.
3)
DUST PICK-UP SHOES.......may need adjusted differently for different materials that are to be sanded. An improperly adjusted
shoe will leave trailing debris that will be run over by the wheels and cause “random waves”.
4)
CONTACT WHEELS (DRUMS)... may be out-of-round and cause “chatter”. Contact your American Sanders dealer for
assistance to true or replace the drum.
5)
BEARINGS... in the motor, drum, or fan system may become worn and induce vibration which could cause “chatter”.
6)
PULLEYS... that are damaged or severly worn can induce vibration and cause “chatter”. Contact your American Sanders
dealer for assistance.
American Sanders is not responsibile for rework of floors that are unacceptable to the customer. It is your
responsibility to insure your equipment is in proper operating order, and that you use the right machine for the job.
Clarke
®
American Sanders American 8 Floor Sander Operator's Manual
Page 27
Chatter - Wave Prevention
Clarke American Sanders are designed and manufactured to the most rigid tolerances. However, after a finishing cut it is possible to
see “chatter” or “waves”.
The best guarantee to remove the chatter is to finish the floor with a
rotating horizontal sander, such as Clarke American Sanders’s Sander 16.
To minimize chatter when using a belt or drum sander the following steps should be taken:
1) DRUM PAPER...insure the paper is secured in the slot, but not too tight. Paper that
is too tight will force the drum slot wider, leaving a “slot mark chatter” on the floor.
2) DRUM MARKS........are caused by the operator lowering the drum to the floor without forward traverse. These marks
should be removed by cutting at a 45 degree angle to the mark. Cutting
at the mark while maintaining the same path will only increase the mark depth and width.
Clarke
®
American Sanders American 8 Floor Sander Operator's Manual
Page 27
Chatter - Wave Prevention
Clarke American Sanders are designed and manufactured to the most rigid tolerances. However, after a finishing cut it is possible to
see “chatter” or “waves”.
The best guarantee to remove the chatter is to finish the floor with a
rotating horizontal sander, such as Clarke American Sanders’s Sander 16.
To minimize chatter when using a belt or drum sander the following steps should be taken:
1) DRUM PAPER...insure the paper is secured in the slot, but not too tight. Paper that
is too tight will force the drum slot wider, leaving a “slot mark chatter” on the floor.
2) DRUM MARKS........are caused by the operator lowering the drum to the floor without forward traverse. These marks
should be removed by cutting at a 45 degree angle to the mark. Cutting
at the mark while maintaining the same path will only increase the mark depth and width.
Clarke
®
American Sanders American 8 Floor Sander Operator's Manual
Page 27
Chatter - Wave Prevention
Clarke American Sanders are designed and manufactured to the most rigid tolerances. However, after a finishing cut it is possible to
see “chatter” or “waves”.
The best guarantee to remove the chatter is to finish the floor with a
rotating horizontal sander, such as Clarke American Sanders’s Sander 16.
To minimize chatter when using a belt or drum sander the following steps should be taken:
1) DRUM PAPER...insure the paper is secured in the slot, but not too tight. Paper that
is too tight will force the drum slot wider, leaving a “slot mark chatter” on the floor.
2) DRUM MARKS........are caused by the operator lowering the drum to the floor without forward traverse. These marks
should be removed by cutting at a 45 degree angle to the mark. Cutting
at the mark while maintaining the same path will only increase the mark depth and width.
Initial Cut
:
The purpose of the initial cut is to remove old finish and gross imperfections on the floor surface. The sanding equipment should be adjusted to heavy sanding
pressure setting and a coarse abrasive should be used. If the surface is severely damaged by deep scratches, pre-existing dwell marks, uneven planks, etc., it may
be necessary to sand across or diagonally to the grain to restore evenness to the surface. If these conditions are not present, the initial cut should be done in the
direction of the grain. If glazing, loading, or burning takes place immediately into an initial cut, select a coarser abrasive. If this should occur during an initial cut, the
abrasive has dulled and must be replaced.
Final Cuts
:
The purpose of a finishing cut is to remove the scratches produced during the initial cut. Use a fine (60 - 80 grit) grain abrasive and a reduced sanding pressure setting.
If the surface remains rough after a finishing cut, it may be necessary to use an even finer grain of abrasive (80 - 100 grit). Care should be taken in selecting the grit
size of the abrasive. A very fine grain will close the pores on a wood floor making admission of a stain difficult. If glazing or burning should occur immediately into a
finishing cut, reduce the sanding pressure. If it should occur during a finishing cut, the abrasive has dulled and must be replaced.
Summary of Contents for American Sanders American 8
Page 1: ...Drum Sander American 8 Operator s Manual...
Page 2: ......
Page 17: ...15 Notes...
Page 18: ......
Page 24: ...22 Base Assembly 2...
Page 27: ......