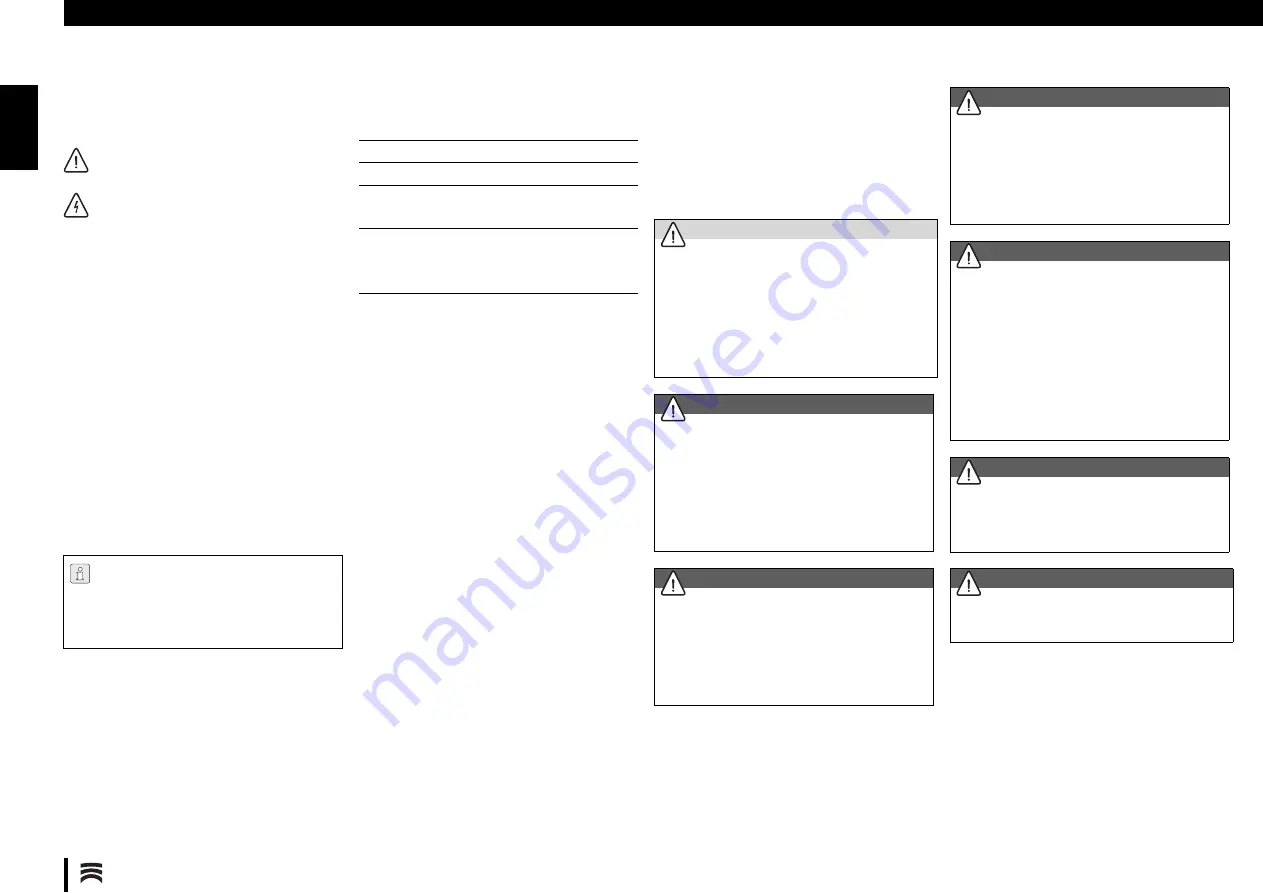
E N
E X P L A N A T I O N O F S Y M B O L S
4
1
Explanation of Symbols
Warning indications
Warning indications in the text are
marked with a triangle and boxed.
In case of hazards through electricity,
the exclamation mark in the warning tri-
angle is substituted by a lightning bolt.
Signal words at the beginning of a warning
indication specify the type and severity of the
consequences, if the measures to avert the
hazard are not adhered to.
_
NOTE
means that property damage can
occur.
_
CAUTION
means that light to fairly serious
personal injury can occur.
_
WARNING
means that serious personal
injury can occur.
_
DANGER
means that life-threatening per-
sonal injury can occur.
Important information
Other symbols in the Manual
2
General Maintenance
and Cleaning Instruc-
tions
When installing, starting-up and operating the
machine, always observe the following safety
instructions:
Important information that does not
lead to hazards for humans or property
damage are marked with the icon aside
and are also boxed.
Symbol
Meaning
▷
Item of an operation description
_
Item of a list
▪
Subitem of an operation descrip-
tion or a list
[3]
Numbers in square brackets refer
to position numbers in graphs/fig-
ures
CAUTION:
A defective machine can lead to malfunctions!
On detection of damage or a functional defect
of the machine:
▷
Label the machine as defective.
▷
Prevent further operation until the
machine is repaired.
NOTE:
Possible damage to the glass window!
Zirconia dust is abrasive and can cause
scratches in glass.
▷
Clean the window in the door carefully,
using only a soft cloth; do not scrub or
scour.
NOTE:
Possible damage to the milling chamber!
Cleaning agents can aggressive to the inner
walls of the milling chamber.
▷
Clean the milling chamber with water only.
▷
Do not use cleaning agents.
NOTE:
Possible machine damage through dried-in
coolant/lubricant and bound in milling dust.
After wet processing:
▷
Clean and dry the milling chamber prior to
downtimes lasting several hours.
NOTE:
Possible machine damage due to unsuitable
cleaning agents!
▷
Clean the milling chamber and material
store only with the specified cleaning aids
(brush, cleaning cloth).
▷
Do not use sponges, brushes etc.
▷
Do not use compressed air, ultrasonic or a
steam jet for the cleaning!
NOTE:
Insufficient milling results!
▷
Keep the zero-point clamping system
clean at all times.
NOTE:
The machine may only be serviced by trained
specialised personnel.