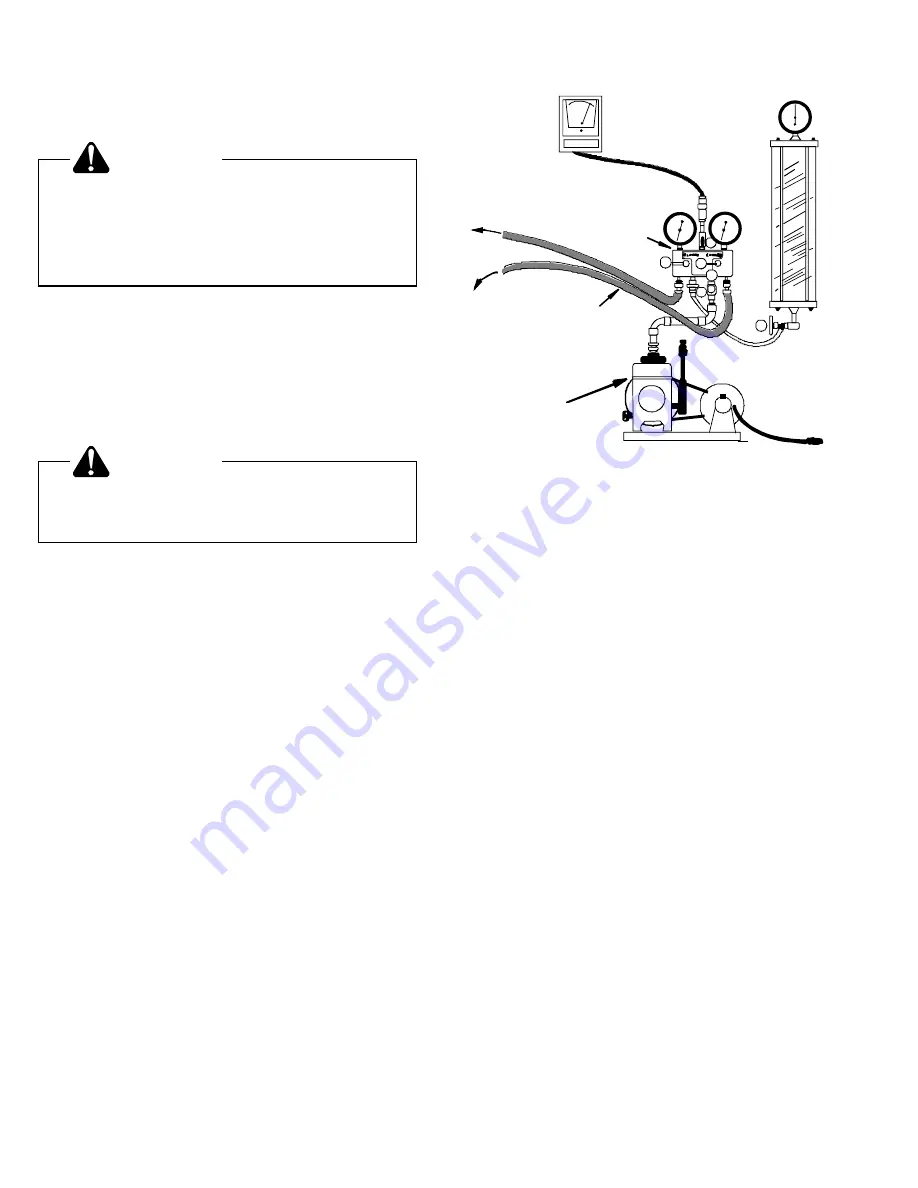
4
A. HIGH SIDE VALVE
B. LOW SIDE VALVE
C. VACUUM PUMP
D. THERMOCOUPLE GAUGE
E. MANIFOLD GAUGE
F. CHARGING CYLINDER
C
A
B
E
D
HIGH VACUUM PUMP
LARGE DIAMETER
BRAIDED VACUUM
HOSES
TO
RELATED
GAUGE
PORTS OF
COND. UNIT
HIGH VACUUM
MANIFOLD
LOW SIDE
GAUGE
HIGH SIDE
GAUGE
DIAL-A-CHARGE
CHARGING CYLINDER
THERMOCOUPLE
VACUUM
GAUGE
F
Figure 2
5. Open the high and low side valves on the gauge
manifold. Keep the valve on the charging cylinder itself
closed, but open the valve on the gauge manifold that
leads to the cylinder.
6. Evacuate the system to about 29 inches of vacuum as
measured by the compound (low side) gauge.
7. Open the valve to the thermocouple vacuum gauge.
Evacuate until the gauge reads 250 microns or less.
8. Close the valve to the vacuum pump. Wait five min-
utes, then check the pressure on the thermocouple
vacuum gauge:
a. If the pressure is not more than 1500 microns, the
system is leak-free and properly evacuated. Pro-
ceed to Step 9.
b. If the pressure rises, but holds at about 5000
microns, moisture and noncondensibles are still
present. Open the valve to the vacuum pump, and
go back to Step 7.
c. If the pressure rises above 5000 microns, a leak is
present. Go back to “Leak Testing” section on page
4.
9. Close the valve to the thermocouple vacuum gauge.
Close the valve to the vacuum pump. Shut off the
pump.
way.) Attach this gauge manifold to the service valves
on the unit. Do not open the unit service valves. Do not
use refrigerant from the unit for leak testing - it has
been precisely measured at the factory for optimum
performance.
WARNING
To avoid possible explosion, the line from
the nitrogen cylinder must include a
pressure regulator and a pressure relief
valve. The pressure relief valve must be set
to open at 175 psig or less.
2. Connect a cylinder of dry nitrogen to the center port on
the gauge manifold.
3. Open the hand valve a minimal amount on the line
coming from the nitrogen cylinder.
4. Open the high pressure valve on the gauge manifold.
Pressurize the refrigerant lines and the indoor coil to
150 psig (1034 kPA). To reach 150 psig, you may need
to further open the hand valve on the nitrogen cylinder.
WARNING
To avoid possible explosion or equipment
damage, do not exceed 150 psig when
pressure testing.
After you reach 150 psig, close the valve on the nitrogen
cylinder. Disconnect it from the gauge manifold. If you plan
to use an electronic leak detector, add a trace of R-22 to
the system (if permitted by current EPA regulations).
5. Put a soap solution on all connections and joints. If you
see bubbles, you have a leak. Mark these locations.
6. Use the gauge manifold to carefully release the nitro-
gen from the system. If leaks were found, repair them.
After repair, repeat the above pressure test. If no leaks
exist, proceed to system evacuation.
ID COIL AND LINE SETS EVACUATION
1. To speed nitrogen release, use a core puller to remove
the valve cores from the service valves.
2. Connect the vacuum pump, high vacuum manifold set
with high vacuum hoses, thermocouple vacuum gauge
and charging cylinder as shown. Begin with all valves
fully closed.
3. Your first step will be only to confirm proper pump and
gauge operation. Open only the shutoff valve which
leads to the vacuum pump (Figure 2)(C). Start the
pump. After the gauge manifold (low side) reading
drops to about 29 inches of vacuum, open only the
valve to the thermocouple vacuum gauge(D). Evacu-
ate until the gauge reads 250 microns or less.
4. Close the valve to the thermocouple vacuum gauge(D).
This will avoid potential gauge damage from “pegging
the meter”. Now that proper pump and gauge opera-
tion has been confirmed, you are ready to begin the
actual evacuation of the lines and indoor coil.