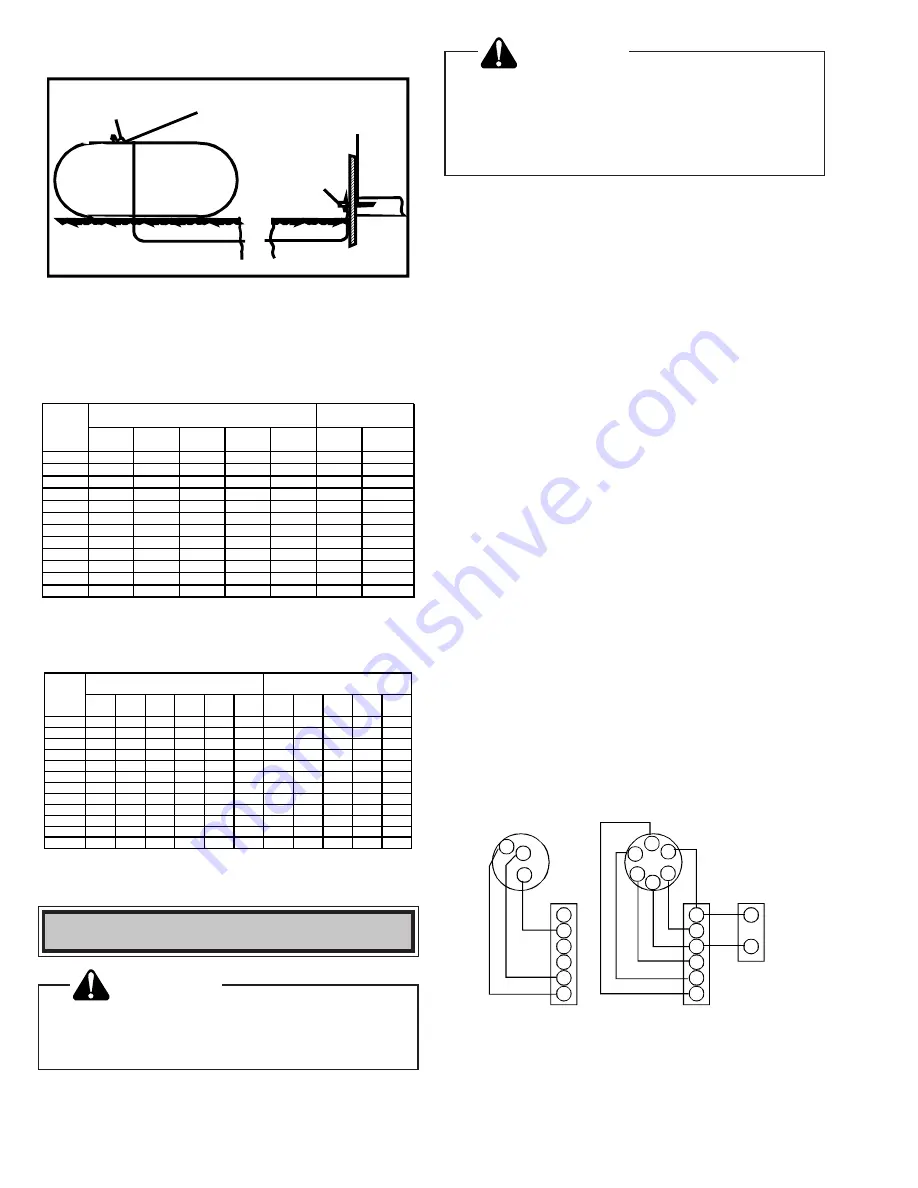
12
Refer to Figure 16 for typical propane gas installations.
200 PSIG
Maximum
5 to 15 PSIG
(20 PSIG Max.)
Continuous
11" W.C.
Second Stage
Regulator
First Stage
Regulator
Figure 16
Typical Propane Gas Installations
PROPANE GAS PIPING CHARTS
Sizing Between First and Second Stage Regulator
Maximum Propane Capacities listed are based on 2 psig pressure drop at 10 psig setting.
Capacities in 1,000 BTU/hour.
Pipe or
Nominal Pipe Size
Tubing
Tubing Size, O.D. Type L
Schedule 40
Length,
3/8"
1/2"
5/8"
3/4"
7/8"
1/2"
3/4"
Feet
10
730
1,700
3,200
5,300
8,300
3,200
7,500
20
500
1,100
2,200
3,700
5,800
2,200
4,200
30
400
920
2,000
2,900
4,700
1,800
4,000
40
370
850
1,700
2,700
4,100
1,600
3,700
50
330
770
1,500
2,400
3,700
1,500
3,400
60
300
700
1,300
2,200
3,300
1,300
3,100
80
260
610
1,200
1,900
2,900
1,200
2,600
100
220
540
1,000
1,700
2,600
1,000
2,300
125
200
490
900
1,400
2,300
900
2,100
150
190
430
830
1,300
2,100
830
1,900
175
170
400
780
1,200
1,900
770
1,700
200
160
380
730
1,100
1,800
720
1,500
To convert to capacities at 15 psig settings - multiply by 1.130
To convert to capacities at 5 psig settings - multiply by 0.879
Pipe or
Nominal Pipe Size
Tubing
Tubing Size, O.D. Type L
Schedule 40
Length,
3/8"
1/2"
5/8"
3/4"
7/8"
1-1/8"
1/2"
3/4"
1"
1-1/4" 1-1/2"
Feet
10
39
92
199
329
501
935
275
567
1,071 2,205 3,307
20
26
62
131
216
346
630
189
393
732
1,496 2,299
30
21
50
107
181
277
500
152
315
590
1,212 1,858
40
19
41
90
145
233
427
129
267
504
1,039 1,559
50
18
37
79
131
198
376
114
237
448
913
1,417
60
16
35
72
121
187
340
103
217
409
834
1,275
80
13
29
62
104
155
289
89
185
346
724
1,066
100
11
26
55
90
138
255
78
162
307
630
976
125
10
24
48
81
122
224
69
146
275
567
866
150
9
21
43
72
109
202
63
132
252
511
787
200
8
19
39
66
100
187
54
112
209
439
665
250
8
17
36
60
93
172
48
100
185
390
590
*Data in accordance with NFPA pamphlet NO. 54
Sizing Between Single or Second Stage Regulator and Appliance*
Maximum Propane Capacities Listed are Based on 1/2" W.C. pressure drop at 11" W.C. setting
Capacities in 1,000 BTU/hour.
Vl. Electrical Wiring
WARNING
To prevent death or personal injury due to
electric shock, disconnect electrical power
before changing any electrical wiring.
CAUTION
When servicing controls, label all wires
before disconnecting. Wiring errors can
cause improper and dangerous operation.
After servicing is completed, always verify
proper operation.
The unit wiring harness is an integral part of the furnace.
Field alteration to comply with electrical codes should not
be required.
Power supply to the furnace must be NEC Class 1, and
must comply with all applicable codes. The furnace must be
electrically grounded in accordance with the local codes or,
in their absence, with the latest edition of the National
Electrical Code, ANSI NFPA No. 70 and/or the CSA C22.1
Electrical Code. A fused disconnect must be provided and
sized in accordance with the unit maximum overcurrent
protection.
THERMOSTAT REQUIREMENTS
A two stage thermostat must be used with this furnace. A
two stage furnace will have both “W1” and “W2” terminals.
Figure 17 shows connections for heat only two stage
system and a two stage heating/one stage cooling system.
If the thermostat has “Y1” and “Y2” connections and a one
stage cooling system is used, connect “Y” on the furnace
control to “Y1” on the thermostat.
CONTINUOUS FAN OPERATION
The two stage furnace control will energize the low heat
circulator fan speed when the fan switch on the thermostat
is turned to the “ON” position. This fan speed will provide
circulation with less electricity than conventional single
stage equipment.
NOTE
: For two stage heat only (no cooling) applications, the
continuous fan speed may be increased by placing a jumper
between “Y” to “G”. Thermostat must have a ”G” terminal to
make use of this feature.
W2
W1
R
G
Y
W2
W1
R
C
Y
R
B
Y
R
B
G
W1
W2
Y
C
Furnace Control
Furnace Control
Remote
Condensing
Unit
Heating
Room
Thermostat
Heating/Cooling
Room
Thermostat
G
W1
W2
Figure 17
Typical Field Wiring
(24 VAC Control Circuit)