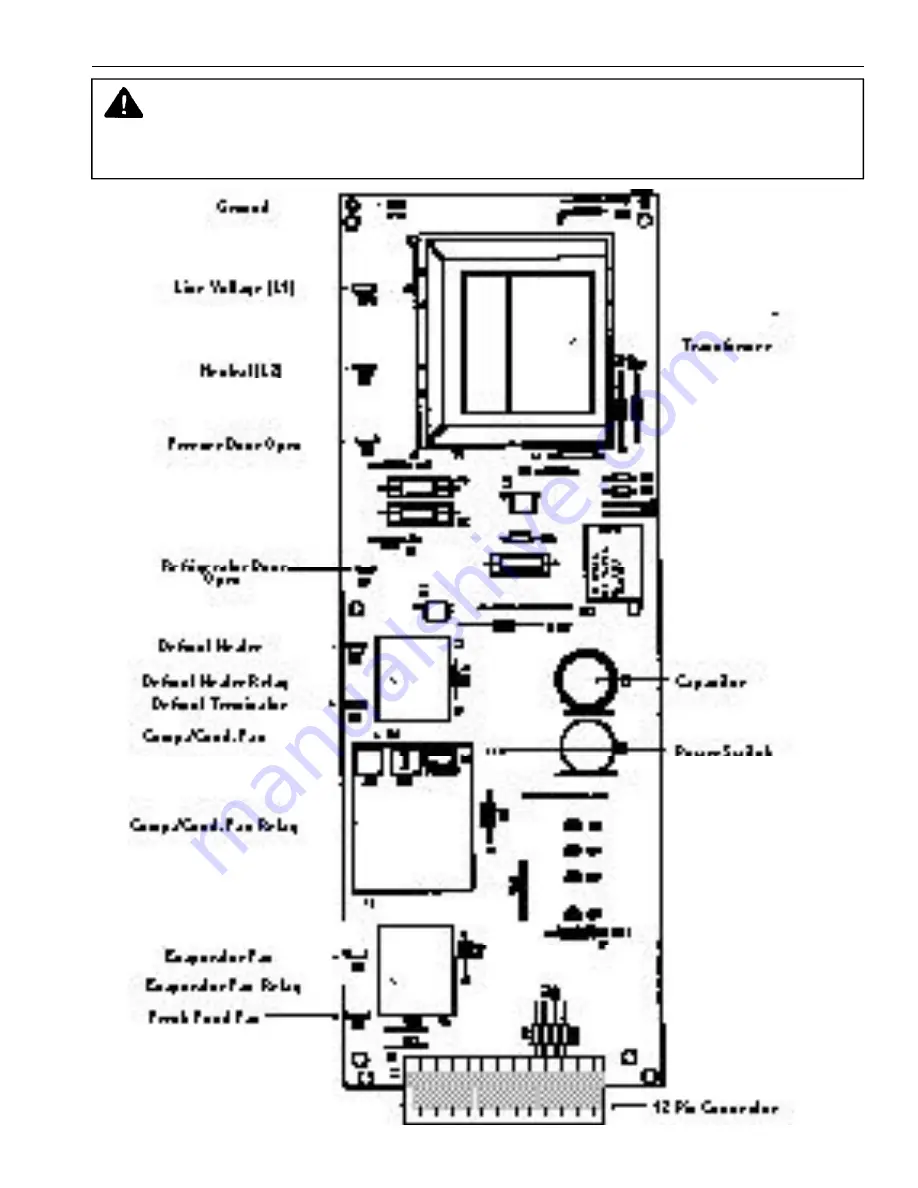
November 1996
31
RS1200001
Electronic Functional Description
To avoid electrical shock which can cause severe personal injury or death, disconnect power to
refrigerator using power switch before servicing. Wires removed during disassembly must be replaced on
proper terminals to insure correct earthing and polarization. After servicing, reconnect power using power
switch.
WARNING
Summary of Contents for Bottom Freezer Refrigerator
Page 17: ...November 1996 17 RS1200001 Refrigerant Flow ...
Page 18: ...RS1200001 18 November 1996 Air Flow ...
Page 19: ...November 1996 19 RS1200001 Machine Compartment Assembly ...
Page 25: ...November 1996 25 RS1200001 Electronic Functional Description ...
Page 50: ...RS1200001 50 November1996 Ice Maker Wiring Diagram and Parts Layout 115 ...