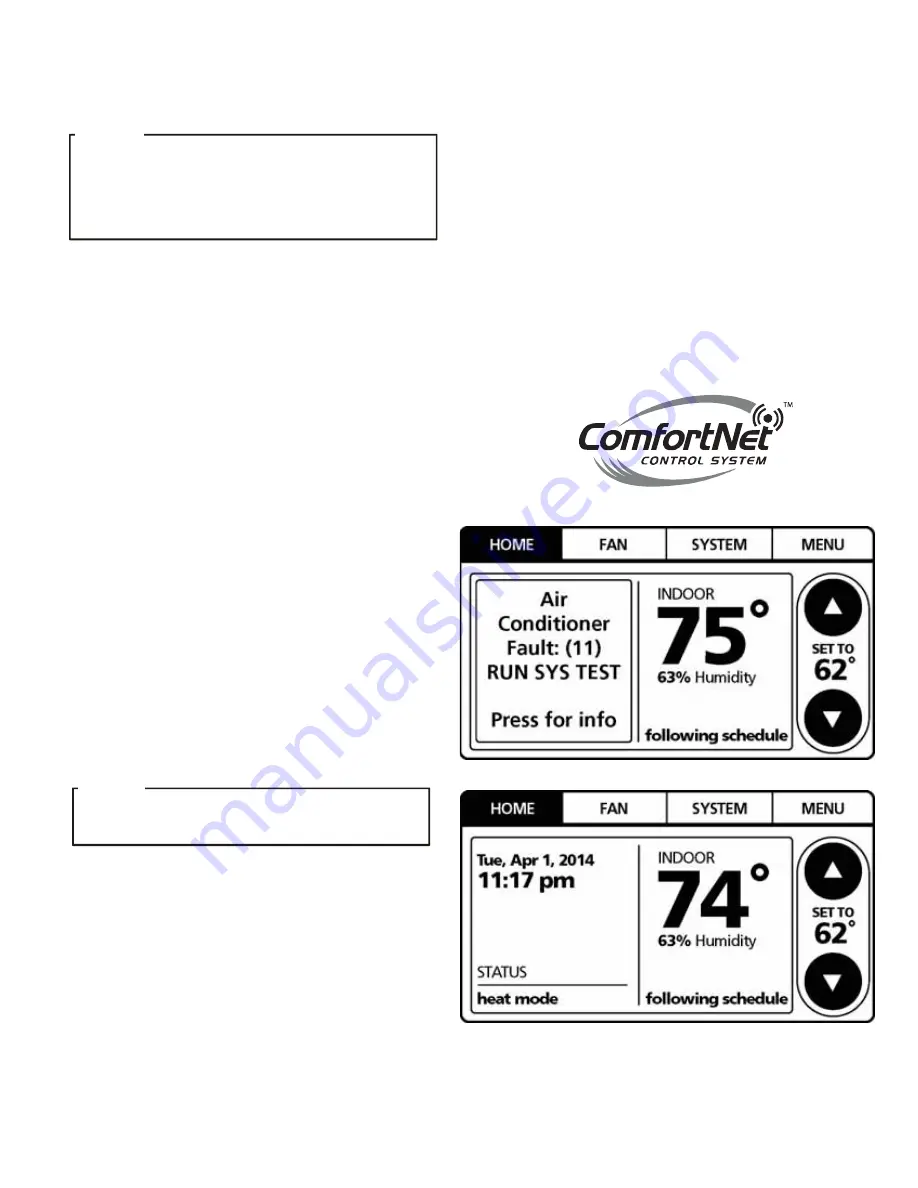
SERVICING
23
T
HERMOSTAT
M
ENU
S
CREEN
S
YSTEM
S
TART
-
UP
T
EST
O
N
INITIAL
POWER
START
-
UP
,
THE
OUTDOOR
UNIT
WILL
DISPLAY
CODE
E11,
SIGNALING
THAT
INITIAL
SYSTEM
TEST
MUST
BE
RUN
. F
OLLOW
THE
C
OMFORT
N
ET
™
SETUP
SCREEN
TO
ENTER
APPLICATION
-
UNIQUE
INFORMATION
. S
EE
C
OMFORT
N
ET
THERMOSTAT
MANUAL
FOR
DETAILED
INFORMATION
.
NOTICE
A system test is now required to check the equipment
settings and functionality. Once selected, it checks the
equipment for approximately 5 - 15 minutes. System test
may exceed 15 minutes if there is an error. Refer to
the Troubleshooting section, if error code appears.
Before starting the SYSTEM TEST, turn off the electric heater
and gas furnace.
NOTE:
If the unit is attempting to run SYSTEM TEST in under 20° F
ambient temperature, the unit may not be able to complete the
test due to low suction pressure. In such a case, re-run the SYS-
TEM TEST when the ambient temperature exceeds 20° F.
1. Ensure the thermostat is installed.
2. Apply power to outdoor and indoor units.
3.
Start-up.
After the application information is entered,
the initial system test must be run.
F
OR
INVERTER
H
EAT
P
UMP
C
ONDENSER
SYSTEM
USING
C
OMFORT
N
ET
,
DO
NOT
INSTALL
A
TRANSFORMER
.
NOTICE
The HOME screen will be displayed showing
information similar to one of the adjacent screens.
Select MENU. Make sure the thermostat is in OFF mode
and select SYSTEM MENU. Choose OFF before SYSTEM
VERIFICATION test.
NOTE:
Either screen may be displayed.
SYSTEM TEST must be run for all installations.
System will not operate without a completed initial
SYSTEM TEST.
NOTE:
The thermostat screen may indicate to run a SYSTEM
VERIFICATION test.