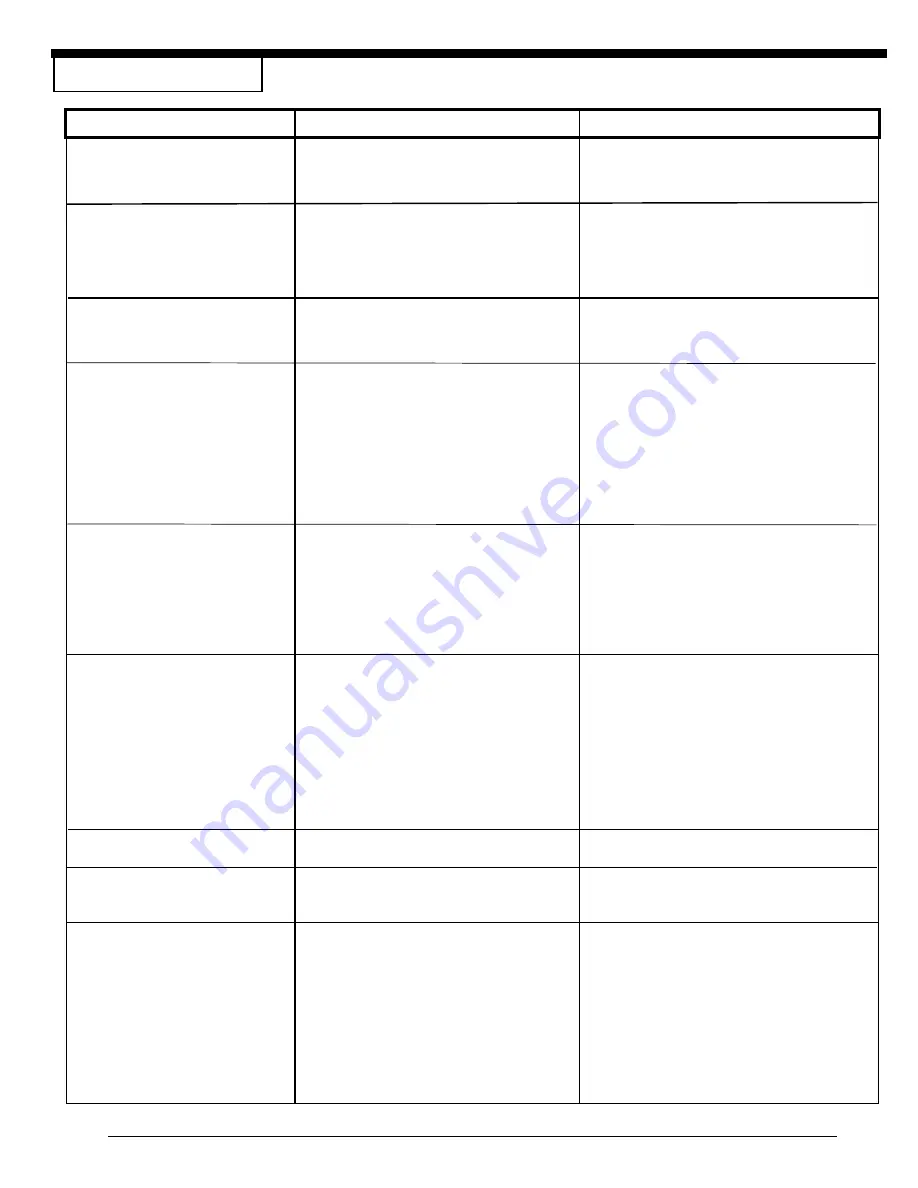
AMERICAN SANDERS TECHNOLOGY -American 12 Floor Sander Operator's Manual
Page 17
P
ROBLEM
C
AUSE
A
CTION
Chatter
Troubleshooting
Drive belts slip.
Insufficient tension.
Tension drive belt.
(Squeaking or squealing sound)
Worn belts.
Replace belts.
Squealing, growling or grinding
Damaged and/or worn bearing.
Remove drive belts, rotate arbor
noise coming from machine.
motor, fan, shafts and idler pulley to
locate dragging or rough bearing.
Contact an authorized American Sanders
Technology dealer.
Dust pick-up is poor.
Dust bag is over 1/3 full.
Empty contents of bag.
Dust bag is dirty.
Shake debris from bag and wash.
Dust chute is obstructed.
Remove fan cover and clear throat.
Motor will not start.
Defective motor starter.
Contact an authorized American Sanders
Technology dealer.
Defective start capacitor.
Contact an authorized American Sanders
Technology dealer.
Defective electronic start switch.
Contact an authorized American Sanders
Technology dealer.
Low voltage from poor connection.
Contact an authorized American Sanders
Technology dealer.
Defective motor.
Contact an authorized American Sanders
Technology dealer.
No power.
Check power supply and connections.
Motor runs sluggishly.
Low voltage from excessive footage,
Locate power source nearer to work site.
undersized extension cord, or poor
Decrease sanding pressure.
connection.
Defective run capacitor.
Contact an authorized American Sanders
Technology dealer.
Defective motor.
Contact an authorized American Sanders
Technology dealer.
Motor starter trips/repeatedly
Excessive load.
Contact an authorized American Sanders
trips.
Technology dealer.
Defective electronic start switch.
Contact an authorized American Sanders
Technology dealer.
Defective motor starter.
Contact an authorized American Sanders
Technology dealer.
Low voltage from poor connection.
Contact an authorized American Sanders
Technology dealer.
Defective motor
Contact an authorized American Sanders
Technology dealer.
Defective capacitor.
Contact an authorized American Sanders
Technology dealer.
Uneven cut.
Leveling out of adjustment.
Readjust leveling.
Burning or glazing.
Dull abrasive.
Replace abrasive.
Excessive sanding pressure.
Decrease sanding pressure setting.
Too fine of an abrasive.
Use coarser abrasive.
Slow cutting.
Dull abrasive.
Replace abrasive.
Too fine of an abrasive.
Use a coarser abrasive.
Insufficient sanding pressure.
Increase sanding pressure setting.
Waves on sanded surface.
Debris on wheel.
Remove and clean wheels.
Flat spot on tire(s).
Replace tires.
Chatter marks on sanded
Drum out of round.
Contact an authorized American Sanders
Surface (close evenly spaced)
Technology dealer or replace the drum.
Drum vibration.
Change shim combination. Remove debris
from surface or ends of drum.