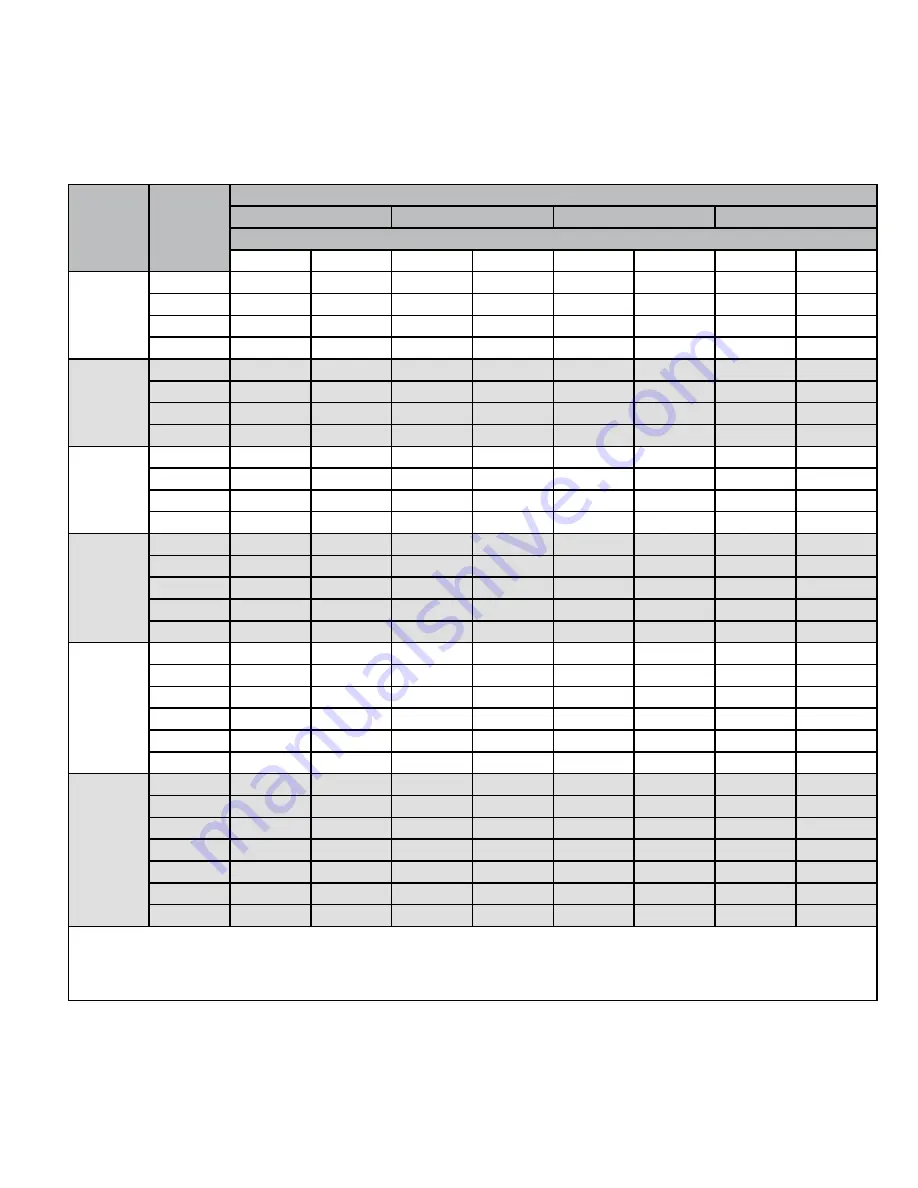
508145-01B
Issue 2108
Page 15 of 36
21. When connecting this appliance to an existing dedicated or common venting system, you must inspect the venting
system’s general condition and look for signs of corrosion. The existing vent pipe size must conform to these instructions
and the provided venting tables. If the existing venting system does not meet these requirements, it must be resized.
Table 5.
Capacity of Type B Double Wall Vents with Type B Double Wall Connectors Serving a Single Category I Appliance
Height
H
(feet)
Lateral
L
(feet)
Vent and Connector Diameter - D (inches)
3 inch
4 inch
5 inch
6 inch
Appliance Input Rating in Thousands of Btu per Hour
MIN
MAX
MIN
MAX
MIN
MAX
MIN
MAX
6
0
0
78
0
152
0
251
0
375
2
13
51
18
97
27
157
32
232
4
21
49
30
94
39
153
50
227
6
25
46
36
91
47
149
59
223
8
0
0
84
0
165
0
276
0
415
2
12
57
16
109
25
178
28
263
5
23
53
32
103
42
171
53
255
8
28
49
39
98
51
164
64
247
10
0
0
88
0
175
0
295
0
447
2
12
61
17
118
23
194
26
289
5
23
57
32
113
41
187
52
280
10
30
51
41
104
54
176
67
267
15
0
0
94
0
191
0
327
0
502
2
11
69
15
136
20
226
22
339
5
22
65
30
130
39
219
49
330
10
29
59
40
121
51
206
64
315
15
35
53
48
112
61
195
76
301
20
0
0
97
0
202
0
349
0
540
2
10
75
14
149
18
250
20
377
5
21
71
29
143
38
242
47
367
10
28
64
38
133
50
229
62
351
15
34
58
46
124
59
217
73
337
20
48
52
55
116
69
206
84
322
30
0
0
100
0
213
0
374
0
587
2
9
81
13
166
14
283
18
432
5
21
77
28
160
36
275
45
421
10
27
70
37
150
48
262
59
405
15
33
64
44
141
57
249
70
389
20
56
58
53
132
66
237
80
374
30
NA
NA
73
113
88
214
104
346
NOTE
: Single appliance venting configurations with zero lateral lengths are assumed to have no elbows in the vent system. For
all other vent configurations, the vent system is assumed to have two 90 ° elbows. For each additional 90° elbow or equivalent (for
example two 45° elbows equal one 90° elbow) beyond two, the maximum capacity listed in the venting table should be reduced by 10
percent (0.90 x maximum listed capacity).