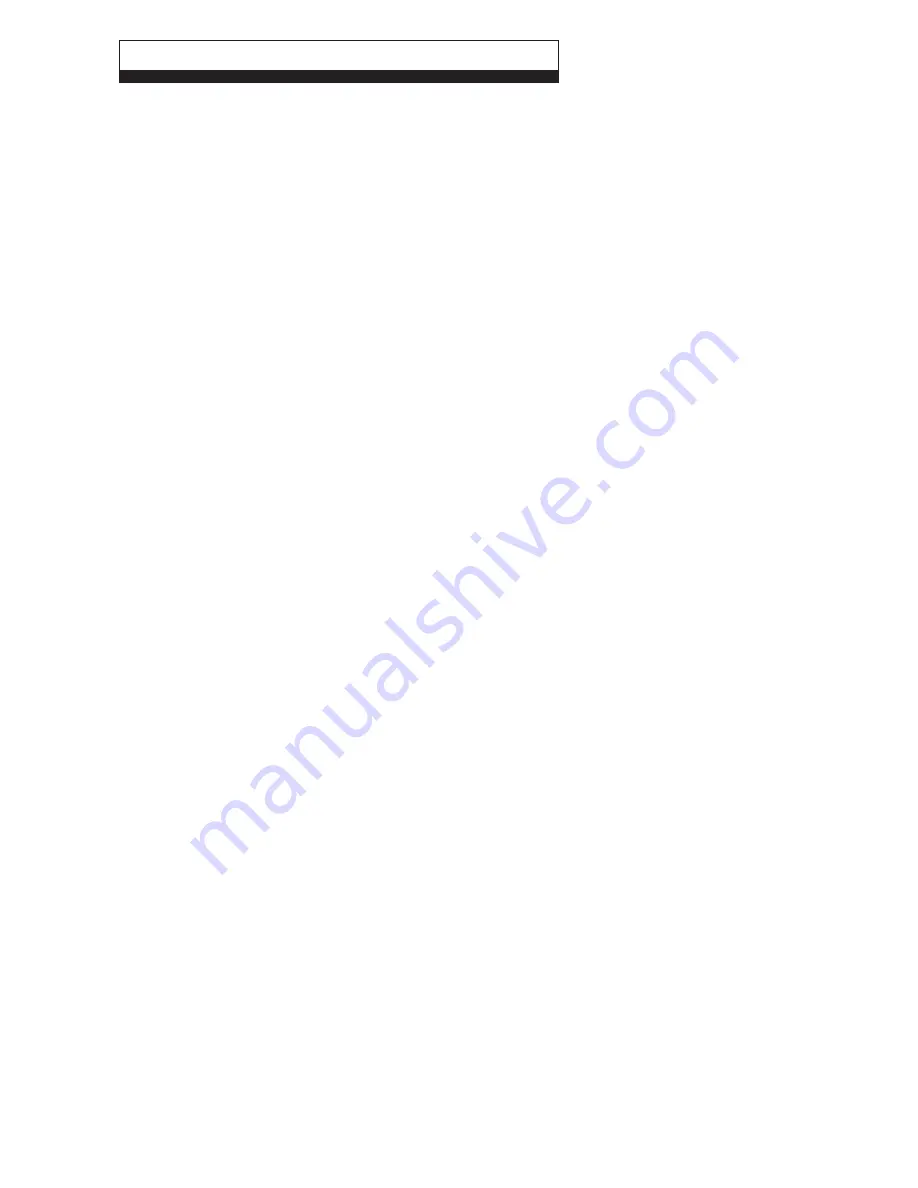
11
3.1 GAS SUPPLY
Natural Gas:
The meter and supply pipes must be capable of delivering the required quantity of gas in addition to the demand from any
other appliances.
The boiler requires at least a 28 mm gas supply pipe and ensure the inlet supply pressure is at least 20 mbar (Natural Gas)
The complete installation, including the meter, must be tested for gas tightness and purged as described in BS 6891 and
IGE/UP/1, IGE/UP/1A or IGE/UP1B.
Propane Gas (LPG):
The local Propane Gas supplier should be consulted, at the installation planning stage, in order to establish the availability of
an adequate supply of gas, 37 mbar for Propane Gas (LPG).
3.2 ELECTRICAL SUPPLY
The boiler requires a 220/240 V ~ 50 Hz permanent mains supply, fused at 3 A
Note: The boiler must be earthed.
There must only be one common isolator, providing complete electrical isolation, for the boiler and any external controls.
This boiler has been fitted with a supply cable, however, if it is necessary to fit a cable use PVC insulated cable not less than
0.75 mm² (24 x 0.2 mm). The boiler should be connected to a fused three pin plug and unswitched shuttered socket outlet,
or a fused double pole switch with a contact separation of at least 3 mm in both poles.
Wiring external to the boiler must be in accordance with the current IEE Wiring Regulations (BS 7671).
3.3 AIR SUPPLY
Open flued (Type B23 flue)
Alpha Pro Tec boilers leave the factory with 'B23' type configuration (open chamber and forced draught - single flue pipe)
and receive the air for combustion from openings in the rear of the boiler, therefore air supply for combustion and ventilation
must be provided in accordance with BS 5440:2 (for domestic installations with a net input less than 70 kW) or BS 6644 (for
commercial installations with a net input over 70 Kw).
Room sealed (Type C flue)
If the boilers are converted to a 'C' type configuration (sealed chamber and forced draught - concentric flue pipe) as
described in Section 3.4 only air for ventilation is required.
1. If the boiler is installed in a room -
No air vents are required in the room in which the boiler is installed.
2. If the boiler is installed in a cupboard or compartment -
Permanent air vents for ventilation are required in the
cupboard or compartment, one at high level and one at low level, either direct to the outside air or to a room. Both the
high and low level air vents must communicate with the same room or must be on the same wall to outside air. Both the
high and low level vent must each have a free area as per BS 5440:2 or BS 6644.
The minimum clearances for servicing must always be maintained.
3.4 FLUE SYSTEM
The flue system must be installed in accordance with BS 5440:1 or BS 6644.
For horizontal flues ensure the flue assembly slopes downwards towards the boiler by a minimum of 25 - 30 mm per metre
of flue.
It is recommended that horizontal and vertical flue assemblies should be supported at least every 1.5 m with access provided
to the joints.
Alpha Pro Tec boilers leave the factory with 'B23' type flue configuration (open chamber and forced draught - single flue
pipe). To change the configuration to 'C' type (sealed chamber and forced draught - concentric flue pipe), remove the 80 mm
dia. adapter, the bracket and gasket from the top of the boiler and fit the concentric flue adaptor, see Sections 4.5 and 4.6.
Note: 1.
Under no circumstances must the flue length (including allowances for extra bends) exceed the maximum flue lengths
stated for each type of flue.
2.
Failure to use the correct Alpha flue components with the boiler will invalidate the boilers CE approval, guarantee
and may be unsafe.
Seals for flue elements -
If lubrication of components (already performed by the manufacturer) is not sufficient, remove the
residual lubricant using a dry cloth, then to ease fitting apply a small amount of common or industrial talc to the seal.
Ensure that the seals are correctly located in the elbows and extensions when assembling the flue.
Note:
Do not use silicone or other oil based lubricants on the flue seals.
Alpha Pro Tec - General Boiler Information
3 GENERAL BOILER INFORMATION