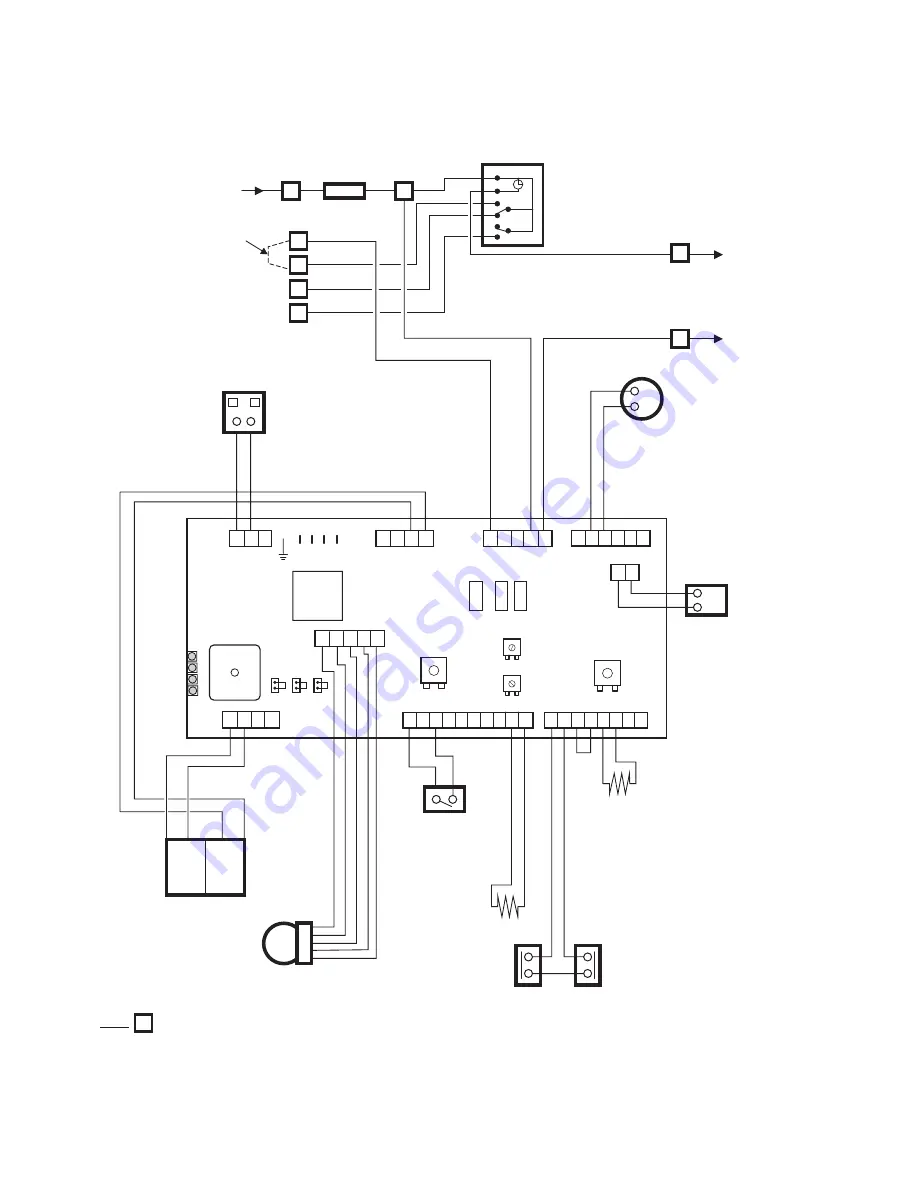
36
9.2 FUNCTIONAL FLOW WIRING DIAGRAM
Alpha CD12S/20S/28S - Wiring Diagrams
Pump
Fan
Gas Valve
Primary
Temperature
Sensor
Primary
Pressure
Switch
NO
COM
Spark
Generator
Overheat
Thermostat
Heat Exchanger
Thermal Fuse
Note:
Main Terminal Block
Flue
Temperature
Sensor
Transformer
L
N
TO CONNECT EXTERNAL CONTROL REMOVE LINK
FROM TERMINALS 1 AND 2 AND CONNECT 240 V
SWITCHED LIVE TO TERMINAL 1.
240
V
a
c
24
V
a
c
S3
S1
S2
Main
PCB
CH CAP
MAX CAP
X7
X3
1 2
X8
3
2 1
X4
1
2 3 4
X13
4
5
3
2 1
X6
4
3
2 1
X12
4
5
3 2
1
X15
4
6
5
2 3
1
X9
4
6
9
5
8
2 3
7
10
1
X11
4
6
5
8
2 3
7
1
CH SET
DHW SET
Green LED
Yellow LED
Red LED
Red LED
Fuse F1
315 mAT max
250 V
Fuse F2 and F3
2.5 AF
250 V
F1
F2
F3
1
2
3
4
5
Optional
2 Channel Clock
Fuse
F2A
1
2
3
4
230/240V ~ 50Hz
Fuse 3A
Remove link to connect
external control
N
N
L
L
N
N
Summary of Contents for CD12S
Page 43: ...43 Alpha CD12S 20S 28S...