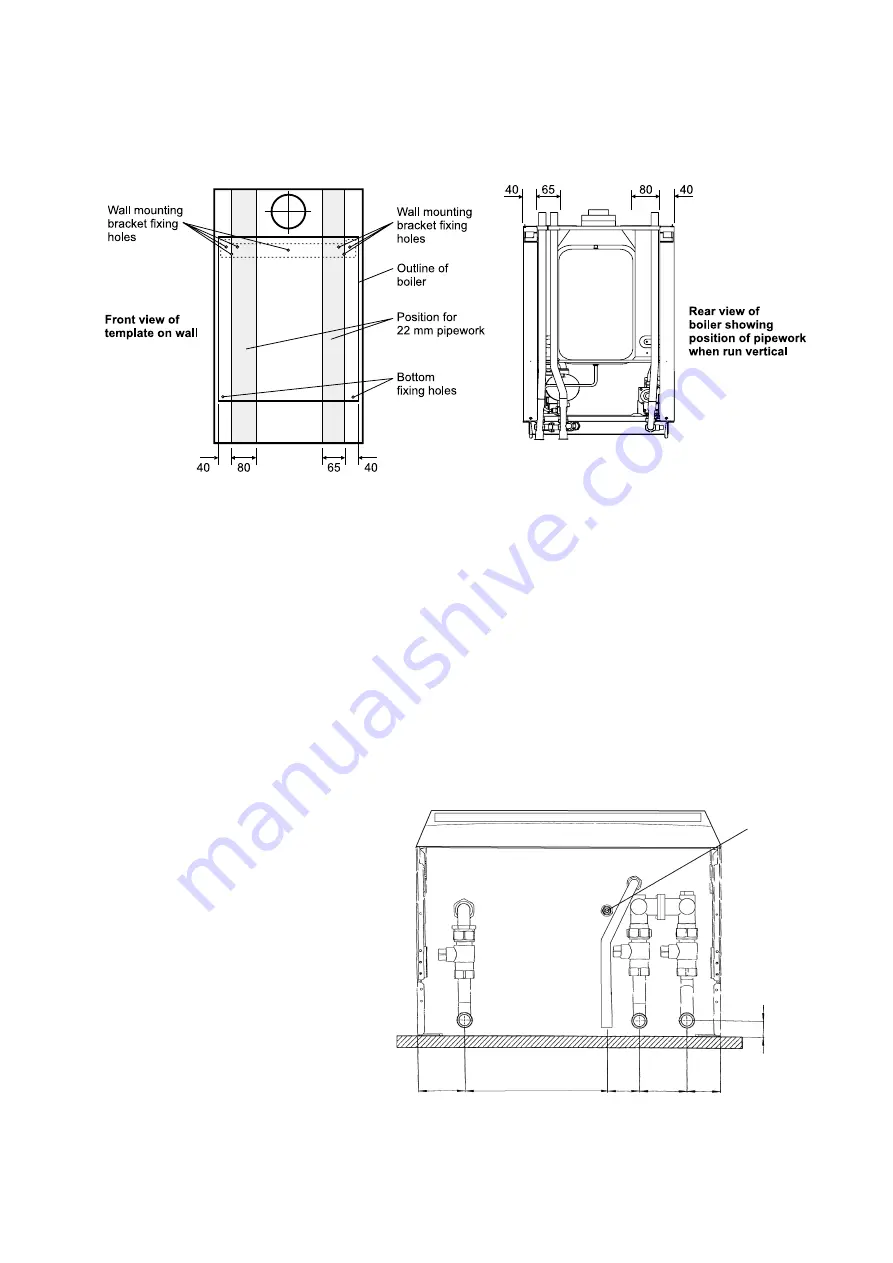
11
Alpha SY9-24 - Installation
Fig. 10
4.4
FIT THE BOILER - Refer to Fig. 10
1.
Lift the boiler and locate it on the mounting bracket.
2.
Fit the bottom screws to secure the boiler in position.
Fig. 11
A - Heating flow (22 mm)
B - Heating return (22 mm)
C - Gas inlet (22 mm)
D - Pressure relief valve (15 mm)
E - Heating drain point
70
212.5
47.5
70
50
A
B
C
D
E
23
4.5
CONNECT THE PIPEWORK - Fig. 11
1.
Thoroughly flush out all the water pipework.
2.
The valves/fittings have been factory fitted, however, check that all the connections underneath the boiler have been
tightened, especially the union bends.
To gain access to all the connections remove the bottom tray by removing the four fixing screws. When all the connections
have been checked for soundness replace the tray and secure with the four screws previously removed.
The heating union bends have been designed to enable the heating pipes to be routed from above and/or below using the
same fitting.
Note: When soldering to the boiler union bends, ensure the bends are not connected to the valves, otherwise the internal
seals may be damaged.
3.
Connect the system pipework to the boiler.
Note: Do not forget that the pressure relief valve discharge pipe must be routed clear of the boiler to a drain in such a
manner that it may be seen, but cannot cause injury to persons or property.
4.
Ensure that all the valves are closed (spindle flats at right angles to valve) and do not turn on the water or gas supplies at this stage.
Summary of Contents for SY9-24
Page 25: ...25 Alpha SY9 24 Wiring Diagrams 9 1 ILLUSTRATED WIRING DIAGRAM 9 WIRING DIAGRAMS ...
Page 26: ...26 9 2 FUNCTIONAL FLOW WIRING DIAGRAM Alpha SY9 24 Wiring Diagrams ...
Page 28: ...28 10 3 FAULT FINDING SOLUTION SECTIONS A to F Alpha SY9 24 Fault Finding ...
Page 29: ...29 Alpha SY9 24 Fault Finding 10 4 FAULT FINDING SOLUTION SECTIONS G to J ...