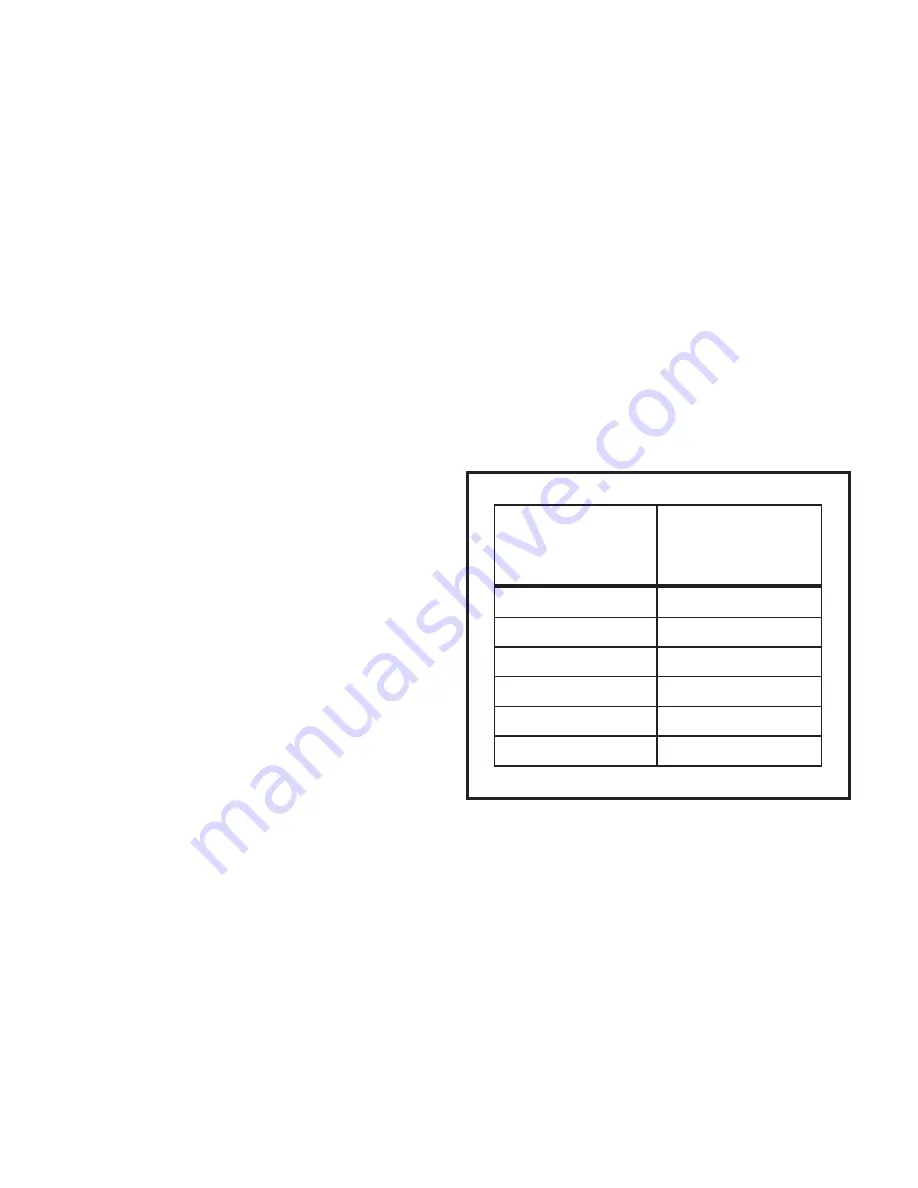
Page 10 of 16
506941-01
Issue 1148
Continuous Blower
With the proper thermostat and sub-base, continuous blower
operation is possible by closing the R to G circuit.
Heating Sequence of Operation
The following sequence describes the operation of the gas
heat section.
1. A call for heat from the room thermostat starts the
combustion air blower and the circulating air blower.
Cooling System Performance
This equipment is a self contained, factory optimized
refrigerant system, and should require no adjustments
when properly installed. If however, unit performance is
questioned, perform the following checks.
Insure unit is installed per manufacturer’s instructions and
that line voltage and air fl ows are correct. Refer to Table 2
for proper superheat or subcooling values. Check superheat
settings by measuring presure at the suction line service
port. For TXV systems, measure pressure at the liquid
service port. Take line temperature within 2 inches of service
port connection to its main tube. If unit superheat/subcooling
varies by more than table allowance, check internal seals,
service panels and duct work for air leaks, as well as
restrictions and blower speed settings. If unit performance
remains quetionable, remove charge, evacuate to 500
Microns, and weigh in refrigerant to name plate charge. It is
critical that the exact charge is re-installed. Failure to comply
will compromise system performance. If unit performance
is still questionable, check for refrigerant related problems
such as, blocked coil or circuits, malfunctioning metering
devices or other system components.
7. After reassembly of all parts is complete and all wires are
reconnected, open the main manual gas shutoff valve;
check for and correct any gas leaks. Turn electrical
power on, initiate a call for heat, and check for proper
burner operation.
8. Install burner access panel.
Heat Anticipator
The heat anticipator setting is 0.75 amp.
It is important
that the anticipator setpoint be correct. Too high of a setting
will result in longer heat cycles and a greater temperature
swing in the conditioned space. Reducing the value below
the correct setpoint will give shorter “ON” cycles and
may result in the lowering of the temperature within the
conditioned space.
OPERATION
Cooling System
The cooling system is a complete factory package utilizing
an air-cooled condenser and is factory-charged with HFC-
R-410A. The compressor is hermetically sealed and base
mounted with rubber-insulated hold-down bolts.
Cooling Sequence of Operation
When the thermostat calls for cooling, R is closed to G and
Y (see the wiring diagram found on page 13). This action
completes the low voltage control circuit, energizing the
compressor, condenser fan motor, and blower motor.
Unit compressors have internal protection. In the event there
is an abnormal rise in the temperature of the compressor,
the protector will open and cause the compressor to stop.
Blower Delay – Cooling
In cooling mode, the circulating air blower operation is
delayed for fi ve (5) seconds after the compressor starts.
The blower continues to operate for 60 seconds after the
compressor is de-energized. The feature is a function of
the blower motor itself and cannot be changed.
NOTE:
There is no blower OFF delay when there is only
a call for G (fan only).
Suction Superheat
Table 2
* This letter will vary according to furnace series.
Outdoor
Unit Model
Suction Superheat
+/- 3° @ ARI
Conditions 82° OD
80° IDDB/67° IDWB
RGE13(*)24
21°
RGE13(*)30
19°
RGE13(*)36
17°
RGE13(*)42
20°
RGE13(*)48
15°
RGE13(*)60
15°