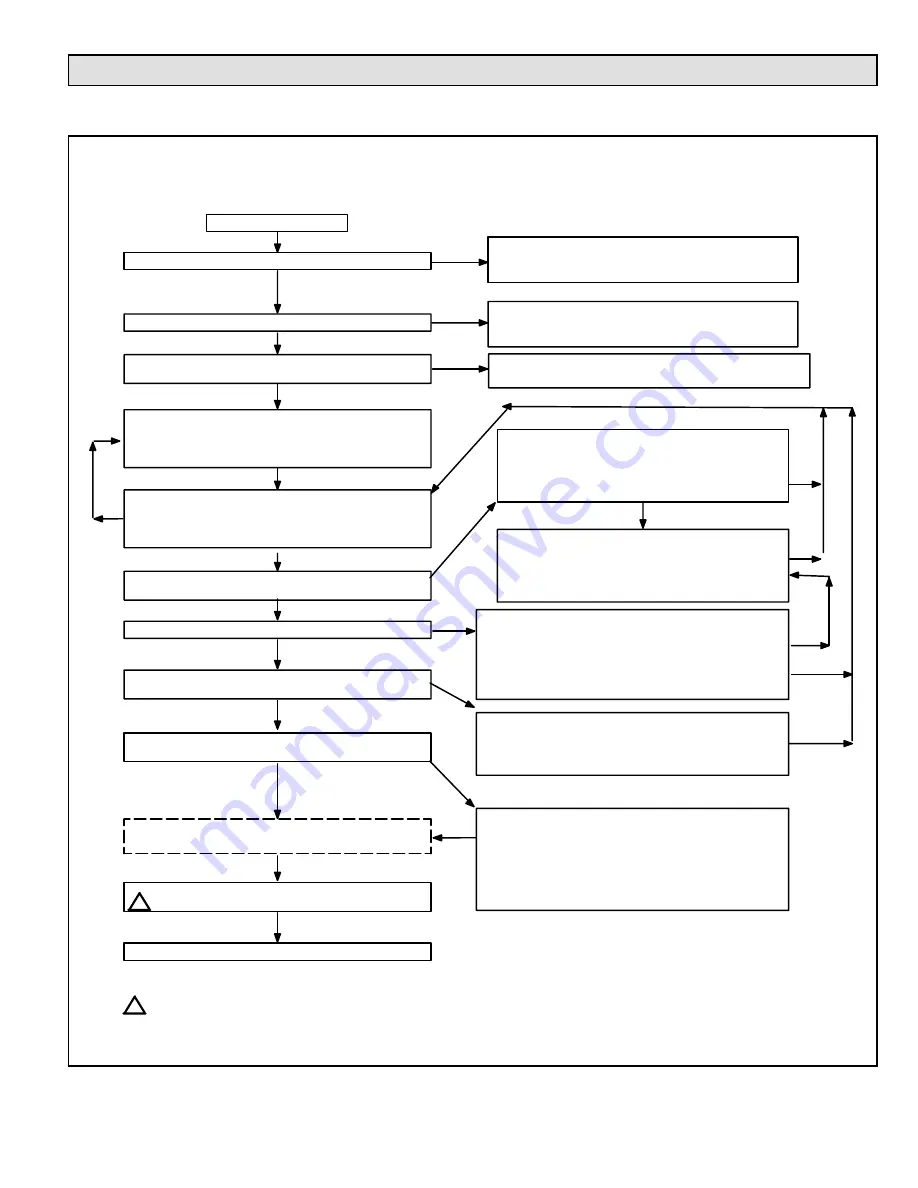
508189-01
Issue 2116
Page 37 of 42
Troubleshooting
Troubleshooting: Heating Sequence of Operation
HEATING SEQUENCE OF OPERATION
NORMAL AND ABNORMAL HEATING MODE
CONTROL SELF-CHECK OKAY?
YES
GAS VALVE OFF. COMBUSTION AIR INDUCER OFF.
INDOOR BLOWER OFF. (RESET CONTROL BY
TURNING MAIN POWER OFF.)
NO
POLARITY REVERSED.
STATUS ERROR CODE 5 + 4.
POWER ON
POLARITY OKAY?
SIGNAL HOLDS UNTIL UNIT IS PROPERLY GROUNDED.
STATUS ERROR CODE 5 + 3.
IS THERE A
PROPER GROUND?
NO
YES
A
NORMAL OPERATION:
STATUS LED -- PULSE
B
THERMOSTAT CALLS FOR HEAT:
STATUS LED -- HEARTBEAT
YES
PRIMARY AND SECONDARY LIMIT
SWITCHES CLOSED?
YES
NO
COMBUSTION AIR INDUCER OFF.
INDOOR BLOWER ON. HAS PRIMARY OR
SECONDARY LIMIT RESET WITHIN 3 MINUTES?
STATUS ERROR CODE 3 + 1.
ROLLOUT SWITCH CLOSED?
GAS VALVE OFF. COMBUSTION AIR INDUCER ON.
INDOOR BLOWER ON.
STATUS ERROR CODE 5 + 1.
SEQUENCE HOLDS UNTIL ROLLOUT SWITCH IS
RESET AND MAIN POWER IS INTERRUPTED OR
T'STAT IS CYCLED OFF/ON FOR 3 SEC. MINIMUM.
NO
YES
FIRST (LOW) STAGE PRESSURE SWITCH
CONTACTS OPEN?
NO
GAS VALVE OFF. COMBUSTION AIR INDUCER OFF.
INDOOR BLOWER OFF. CONTROL REMAINS UNTIL
PRESSURE SWITCH IS DETECTED OPEN.
STATUS ERROR CODE 2 + 4
YES
GAS VALVE OFF.
COMBUSTION AIR INDUCER OFF.
INDOOR BLOWER OFF.
CONTROL WILL NOT ATTEMPT SECOND-STAGE
OPERATION DURING THIS HEAT DEMAND.
FIRST-STAGE OPERATION WILL BE ATTEMPTED.
STATUS ERROR CODE 2 + 6.
NO
TWO-STAGE OR SINGLE-STAGE THERMOSTAT
CALL FOR HEAT
COMBUSTION AIR INDUCER ON LOW SPEED.
STATUS LED -- HEARTBEAT
CONTINUED ON NEXT PAGE
NO
NO
60-MINUTE LIMIT WATCHGUARD MODE.
GAS VALVE OFF, COMBUSTION AIR INDUCER
OFF, INDOOR BLOWER OFF WITH DELAY.
STATUS ERROR CODE 4 + 5.
YES
NO
YES
SECOND (HIGH) STAGE PRESSURE SWITCH
CONTACTS OPEN?
NO
YES
1
1
If the furnace is operating on continuous fan mode (terminals “R” and “G” are energized), the combustion
air inducer will energize on high speed, the gas valve will energize on second-stage heat and the furnace
will operate on high fire. Furnace will stay on high fire 60 seconds then switch to low fire.