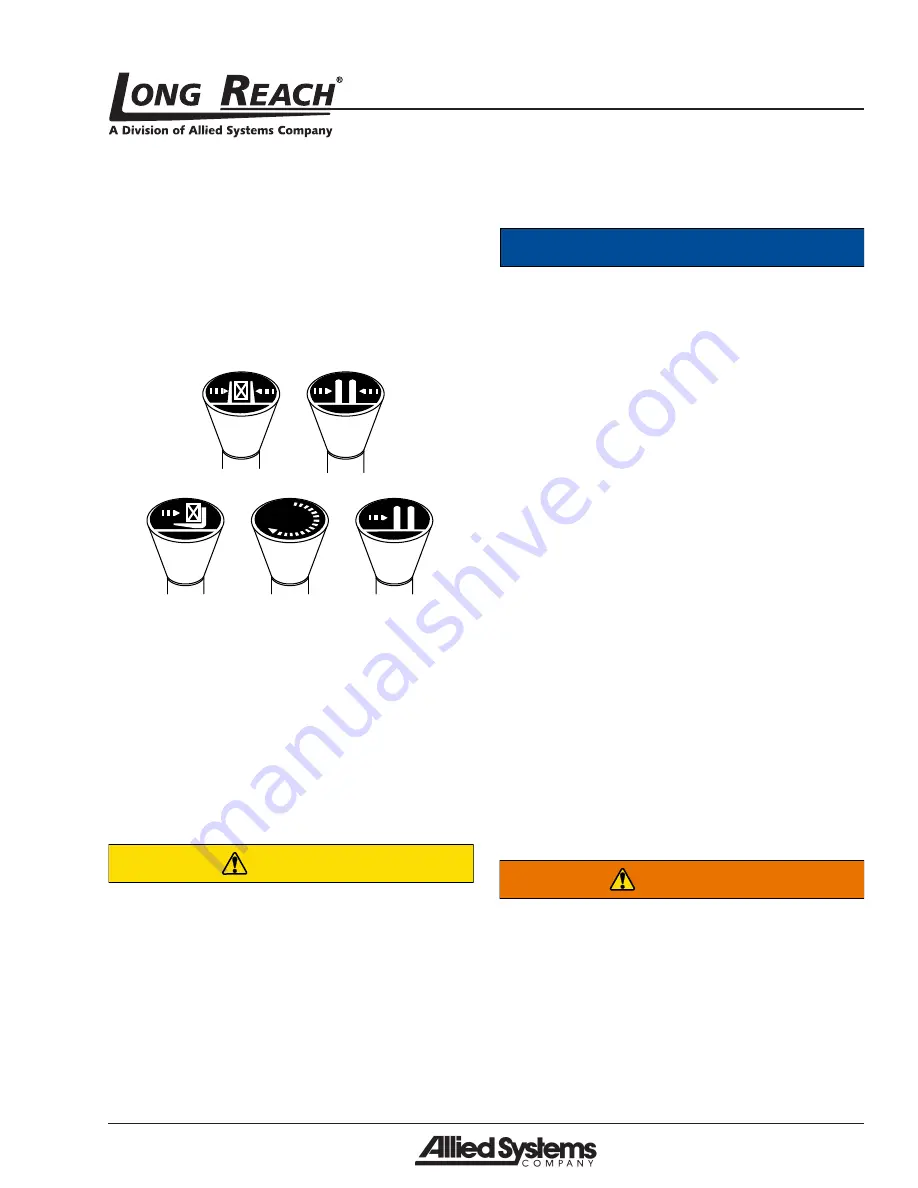
B
45-015, REV. 9/21
3.14 Operator’s Controls
Some lift trucks are equipped with a single lever to
control both hoist and tilt functions, others have separate
levers for each function. Refer to your lift truck manual
for more information.
For clarity, the direction of arm movement is shown on
the control handle. To move the arms in the direction
shown, pull the handle towards the operator. To move
the arms in the opposite direction, the push the handle
away from the operator. (Figure 3-5)
Clamp
Fork position
Push/pull
Rotate
Sideshift
Figure 3-5 Operator controls
Lifting speed is controlled by the speed of the engine
and the position of the control lever. Engine speed has
no effect on lowering speed.
Before going on the job, shift the truck control levers
one way and then the other to determine which direc-
tion the attachment moves when the levers are shifted.
Make sure the attachment moves smoothly throughout
its travel, without binding or pinching hoses.
CAUTION
Equipment damage hazard.
Injury or equipment damage may result
if the attachment does NOT operate
smoothly.
Do not take malfunctioning equipment on
the job. Check with your supervisor about
needed repairs.
3.15 Industry Standards
ANSI/ITSDF B56.1-2016 is the published sequence and
direction standard for lever- and hand-type controls.
Notice
The chart on the following page shows
industry standards. Your equipment
may be different. If you do not routinely
operate this equipment, refresher
training is recommended. You must
reacquaint yourself with this manual and
the equipment before starting, and then
proceed slowly.
Special controls such as automatic devices should be
identified, preferably according to the recommendations
in Figure 3-6.
When a function is controlled by a pair of push buttons,
they should operate in the same sense as the lever
controls. For example, pushing a button located to the
rear (relative to the operator’s position) should serve
the same function as moving a control lever to the rear.
3.16 Clamp Open Control
Effective October 7, 2010, safety standard ANSI/ITSDF
B56.1, Section 7.25.7 covers all lift trucks with a load
bearing clamp (paper roll clamp, carton clamp, etc.),
and requires the driver to make two distinct motions
before opening or releasing the clamp. For example,
you must press a switch and then move a lever to
unclamp the load. This requirement applies to new
and used attachments being mounted on trucks which
shipped from the factory after October 7, 2010, and is a
recommended feature to be installed on dealer orders
and existing applications.
WARNING
Load loss hazard.
Injury or equipment/load damage may
result if a fork positioner attachment is
used to clamp a load. The fork positioner
does not have enough clamping force to
safely hold a load.
Always support the load with the forks.
Do not use fork positioning attachments
as clamps.