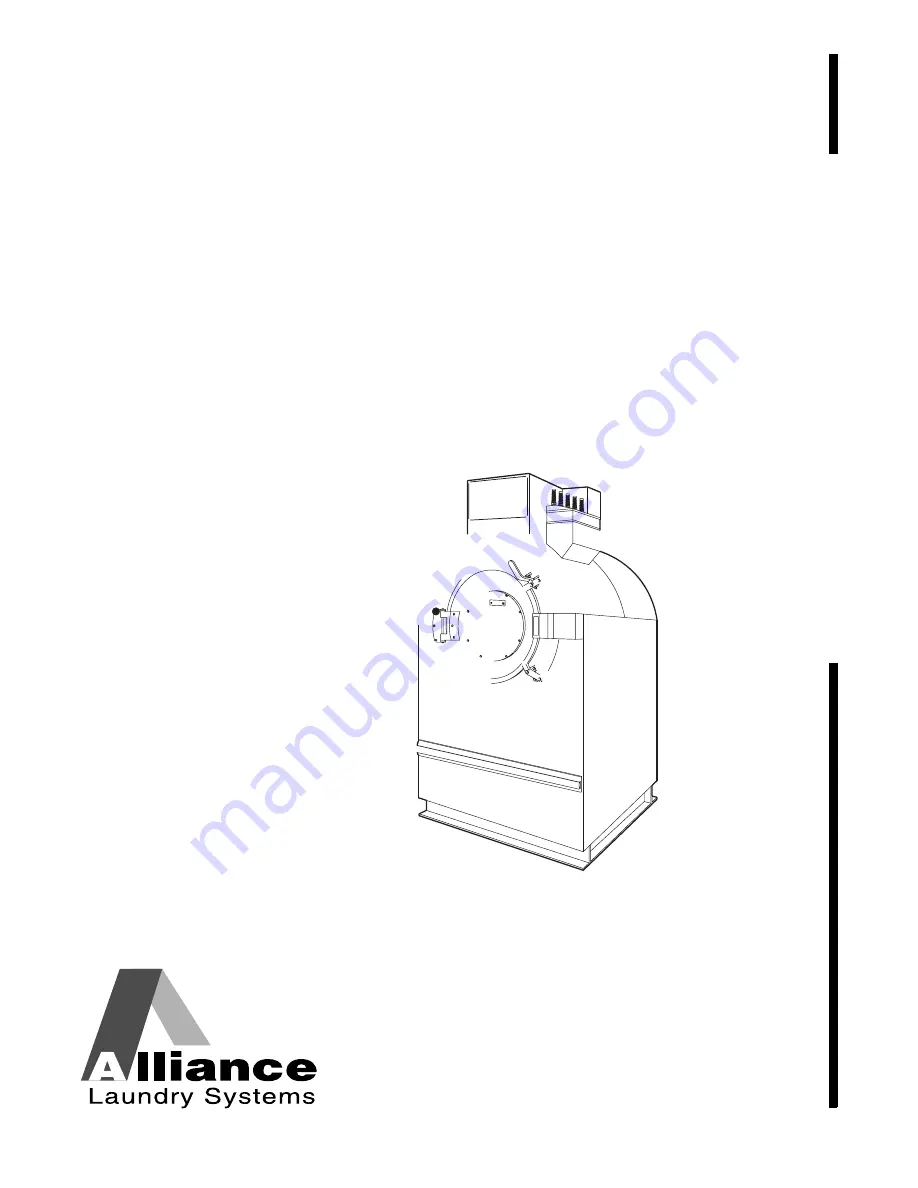
Operation/Maintenance
www.comlaundry.com
Washer-Extractors
Pocket Hardmount
Variable Speed
V-Series Microcomputer
Refer to Page 7 for Model Identification
Operation/Maintenance
www.comlaundry.com
Washer-Extractors
Pocket Hardmount
Variable Speed
V-Series Microcomputer
Refer to Page 7 for Model Identification