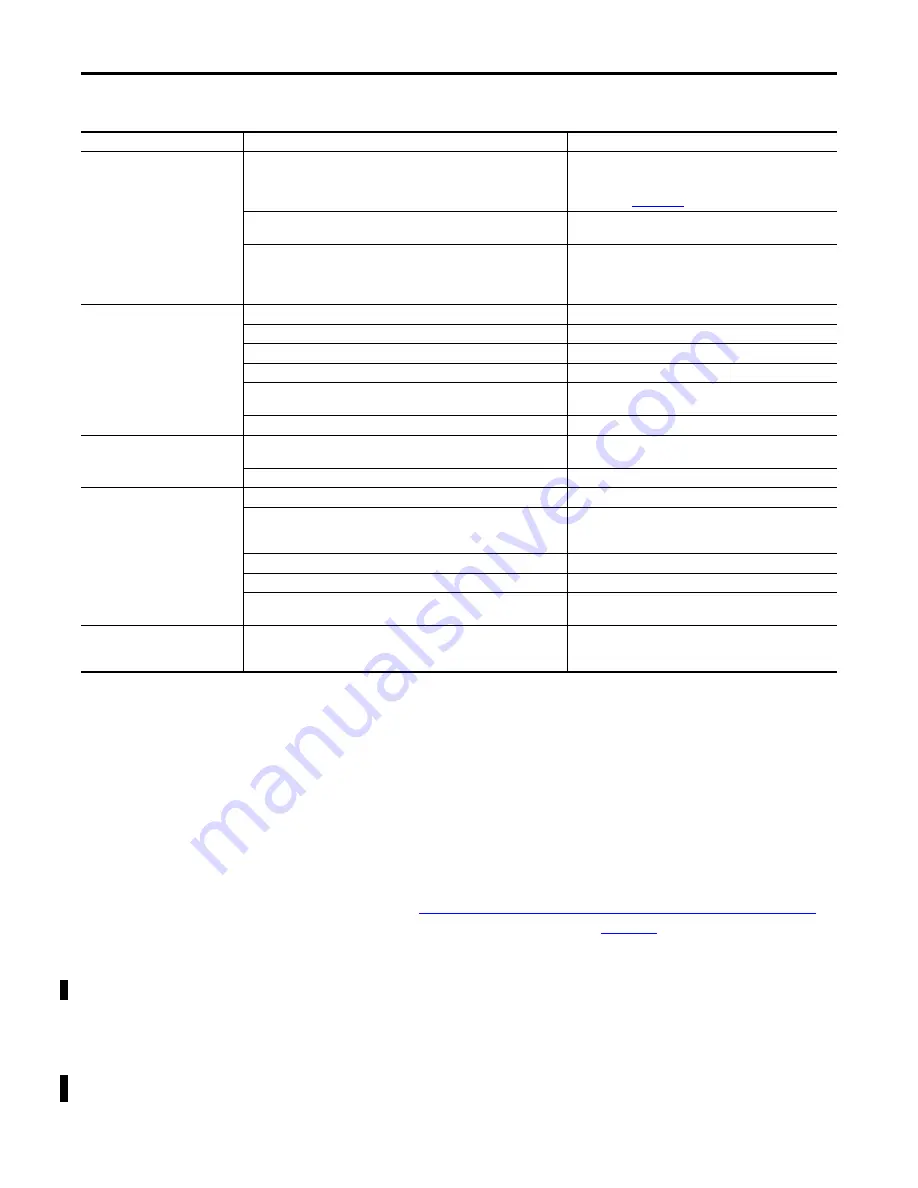
Rockwell Automation Publication 520-UM002B-EN-E - December 2017
129
Troubleshooting
Chapter 7
Logix5000 Controller and
Drive Behavior
By using the Logix Designer application, you can configure how the
PowerFlex 527 drives respond when a drive fault/exception occurs.
The drive supports fault action for Ignore, Alarm, Minor Fault, and Major Fault
as defined in
PowerFlex 527 Drive Exception Action Definitions on page 130
See the drive behavior tables beginning on
fault and stopping actions apply to each of the exception fault codes.
The drive supports these configurable stopping actions
(1)
:
•
Disable and Coast
•
Current Decel and Disable
•
Ramped Decel and Disable
(1)
Disable and Coast
and
Current Decel and Disable
are available in Frequency Control, Velocity Loop and Position Loop.
Ramped Decel and Disable
is available in Frequency Control and Velocity Loop only and is not supported in Position Loop.
Presence of noise on command or
motor feedback signal wires.
Recommended grounding per installation instructions have not been
followed.
•
Verify grounding.
•
Route wire away from noise sources.
•
See System Design for the Control of Electrical Noise,
publication
.
Line frequency can be present.
•
Verify grounding.
•
Route wire away from noise sources.
Variable frequency can be velocity feedback ripple or a disturbance caused by
gear teeth or ballscrew, and so forth. The frequency can be a multiple of the
motor power transmission components or ballscrew speeds resulting in
velocity disturbance.
•
Decouple the motor for verification.
•
Check and improve mechanical performance, for example,
the gearbox or ballscrew mechanism.
No rotation
The motor connections are loose or open.
Check motor wiring and connections.
Foreign matter is lodged in the motor.
Remove foreign matter.
The motor load is excessive.
Verify the induction system sizing.
The bearings are worn.
Return the motor for repair.
The motor brake is engaged (if supplied).
•
Check brake wiring and function.
•
Return the motor for repair.
The motor is not connect to the load.
Check coupling.
Motor overheating
The duty cycle is excessive.
Change the command profile to reduce accel/decel or increase
time.
The rotor is partially demagnetized causing excessive motor current.
Return the motor for repair.
Abnormal noise
Motor tuning limits are set too high.
Run Tune in the Logix Designer application.
Loose parts are present in the motor.
•
Remove the loose parts.
•
Return motor for repair.
•
Replace motor.
Through bolts or coupling is loose.
Tighten bolts.
The bearings are worn.
Return motor for repair.
Mechanical resonance.
Notch filter can be required (See Axis Properties dialog box,
Output tab in the Logix Designer application).
Erratic operation - Motor locks into
position, runs without control or with
reduced torque.
Motor power phases U and V, U and W, or V and W reversed.
Check and correct motor power wiring.
General Troubleshooting
Condition
Potential Cause
Possible Resolution
TIP
The INIT FLT xxx faults are always generated after powerup, but before the
drive is enabled, so the stopping behavior does not apply.
NODE ALARM xxx faults do not apply because they do not trigger stopping
behavior.
Summary of Contents for PowerFlex 527
Page 4: ...4 Rockwell Automation Publication520 UM002B EN E December 2017 Summary of Changes Notes...
Page 8: ...8 Rockwell Automation Publication 520 UM002B EN E December 2017 Table of Contents Notes...
Page 173: ...Rockwell Automation Publication520 UM002B EN E December 2017 173 Notes...
Page 174: ...174 Rockwell Automation Publication 520 UM002B EN E December 2017 Notes...
Page 175: ......