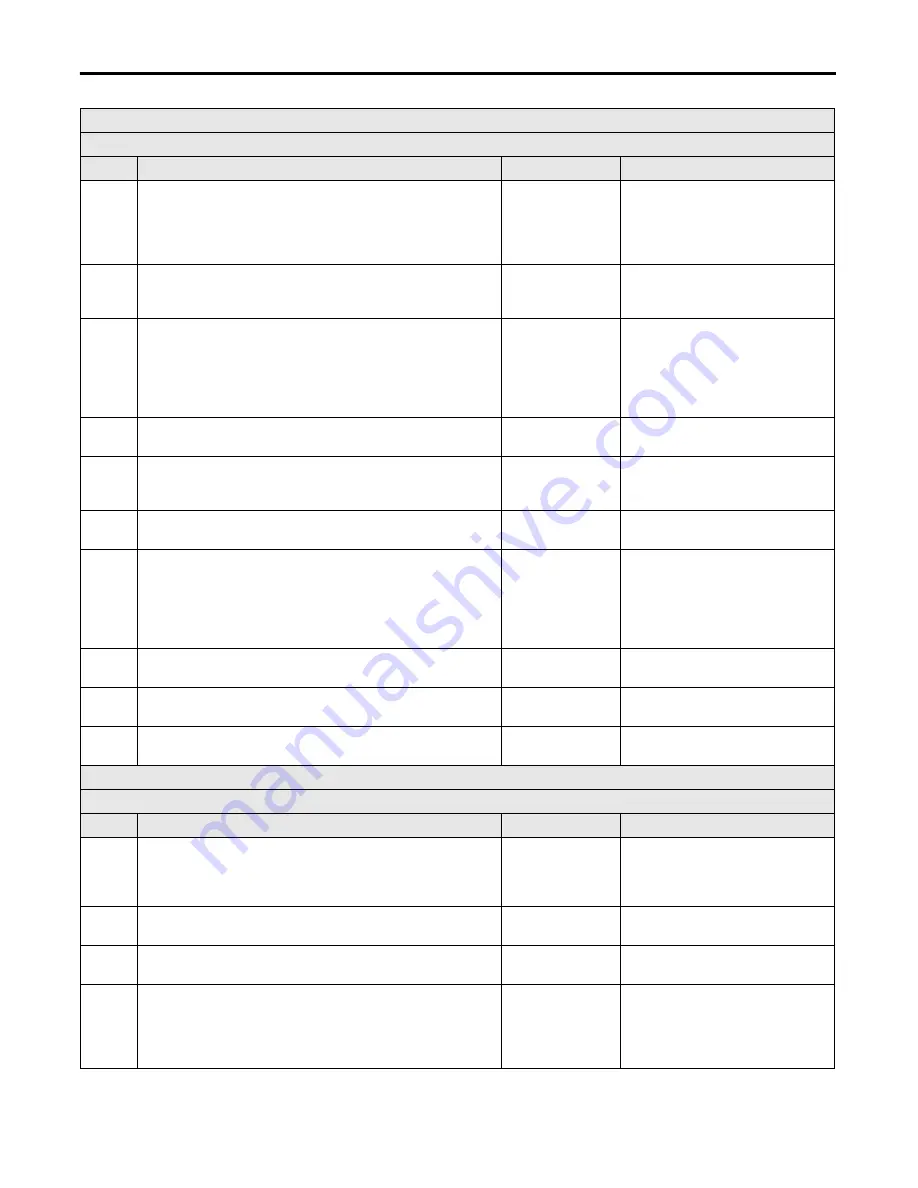
20
Rockwell Automation Publication SAFETY-AT140A-EN-P - May 2015
Safety Function: Actuator Subsystems – Stop Category 1 via the PowerFlex 525 and PowerFlex 527 Drives with Safe Torque-off
Validation of Safe Response to Abnormal Operation - The safety system responds properly to all foreseeable faults with corresponding diagnostics.
Guardmaster Dual-input Safety Relay- Guardmaster Multifunction-delay Expansion Module Tests
Test Step
Validation
Pass/Fail
Changes/Modifications
1
While the machine continues to run, remove the wire from L12 of the Guardmaster
multifunction-delay expansion module. The hazardous motion must coast to a stop.
The Logic IN and OUT status indicators of the Guardmaster multifunction-delay
expansion module must be OFF. The Guardmaster dual-input safety relay is not
affected.
2
Press the external Stop button. Restore the connection. The Guardmaster
multifunction-delay expansion module Logic IN and OUT status indicators are steady
green. Press the external Start button to resume the hazardous motion.
3
While the hazardous motion continues to run, jump 24V to the L12 terminal of the
Guardmaster multifunction-delay expansion module. After a second or two, the
hazardous motion coasts to a stop. The Logic IN and OUT status indicators of the
Guardmaster multifunction-delay expansion module are OFF. The OUT status indicator
of the Guardmaster dual-input safety relay is OFF. The PWR/Fault indicator of the
Guardmaster dual-input safety relay blinks red to show that it is faulted.
4
Remove the jumper. Press and release the Reset button. The Guardmaster dual-input
safety relay must not respond.
5
Cycle power to the Guardmaster dual-input safety relay. It responds. The PWR/Fault,
and IN1 and IN2 status indicators are steady green. The OUT status indicator blinks
green.
6
Press and release the Reset button. Press the external Start button. The hazardous
motion must resume.
7
While the hazardous motion continues to run, jump 0V to the L12 terminal of the
Guardmaster multifunction-delay expansion module. After a second or two the
hazardous motion coasts to a stop. The Logic IN and OUT status indicators of the
Guardmaster multilfunction delay expansion module are off. The OUT status indicator
of the Guardmaster dual-input safety relay is OFF. The PWR/Fault status indicator of
the Guardmaster dual-input safety relay blinks red to show that it is faulted.
8
Remove the jumper. Press and release the Reset button. The Guardmaster dual-input
safety relay must not respond.
9
Cycle power to the Guardmaster dual-input safety relay. It responds. The PWR/Fault,
and IN1 and IN2 status indicators are steady green. The OUT indicator blinks green.
10
Press and release the Reset button. Press the external Start button. The hazardous
motion must resume.
Validation of Safe Response to Abnormal Operation - The safety system responds properly to all foreseeable faults with corresponding diagnostics.
Guardmaster Multifunction-delay Expansion Module - PowerFlex Drive Tests
Test Step
Verification and Validation
Pass/Fail
Changes/Modifications
1
While the machine continues to run, remove the wire from terminal S1 of the
PowerFlex drive. The hazardous motion must coast to a stop.The Guardmaster dual-
input safety relay and the Guardmaster multifunction-delay expansion module are
not affected. The PowerFlex drive has an STO fault.
2
Replace the wire to terminal S1. Press the drive’s Start button. The drive must not
respond. The STO fault remains.
3
Cycle power to the drive. The STO fault is cleared. Press the Start button. The hazardous
motion starts.
4
While the hazardous motion continues to run, jump 24V to terminal S1 of the
PowerFlex drive. Open the guarded gate. The hazardous motion coasts to a stop. The
Guardmaster dual-input safety relay and the Guardmaster multifunction-delay
expansion module behave in the normal way to the gate opening. The PowerFlex drive
has an STO fault.