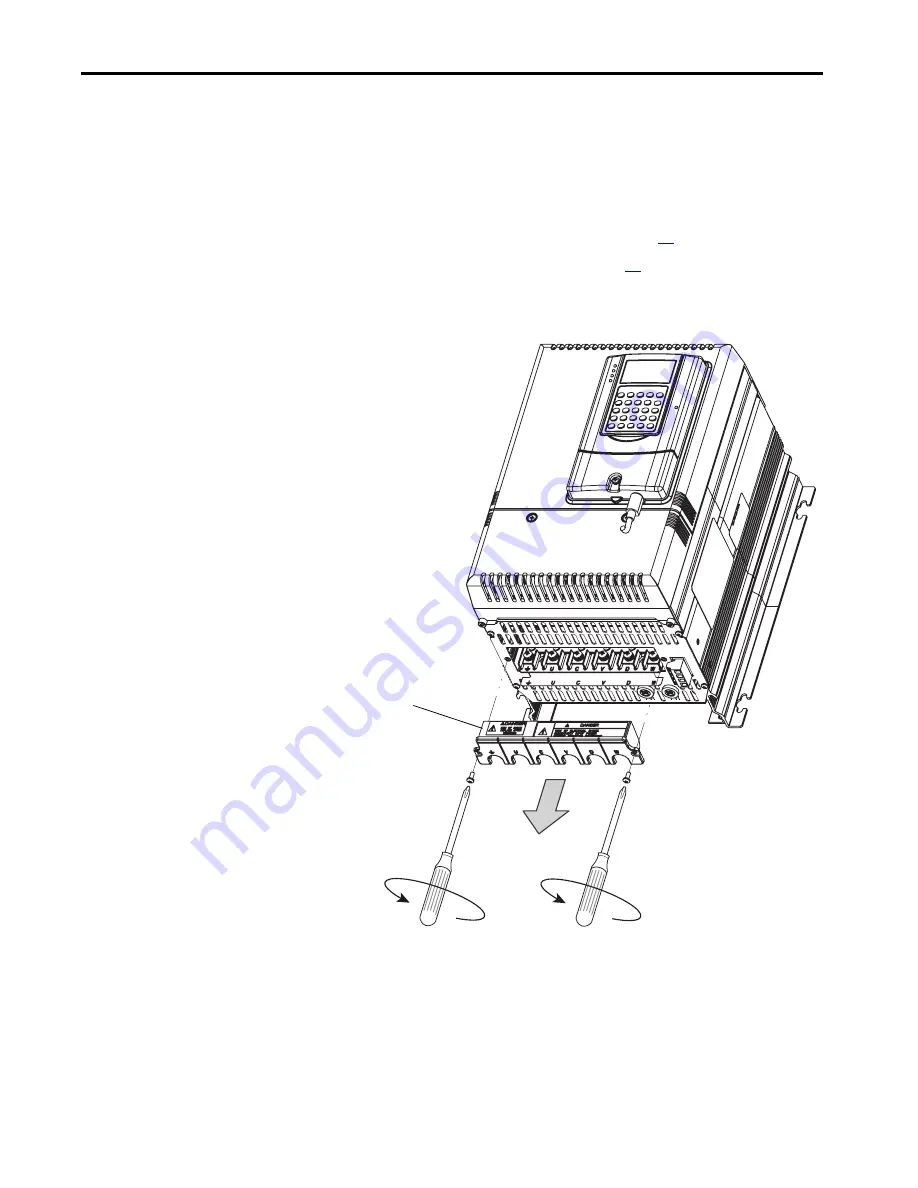
50
Rockwell Automation Publication 20P-TG001C-EN-P - February 2018
Chapter 3
Part Replacement Procedures
Protective Cover
Replacement
Remove the Protective Covers
You must remove both the lower protective cover and the power terminal cover
to access the power terminals. Follow these steps to remove the protective
covers.
1. Read the General Safety Precautions on page
2. Remove power from the drive (see page
3. Loosen the two screws that secure the power terminal cover to the drive
and slide the cover down and off the chassis.
3
Tightening torque:
1.0 N•m (8.9 lb•in)