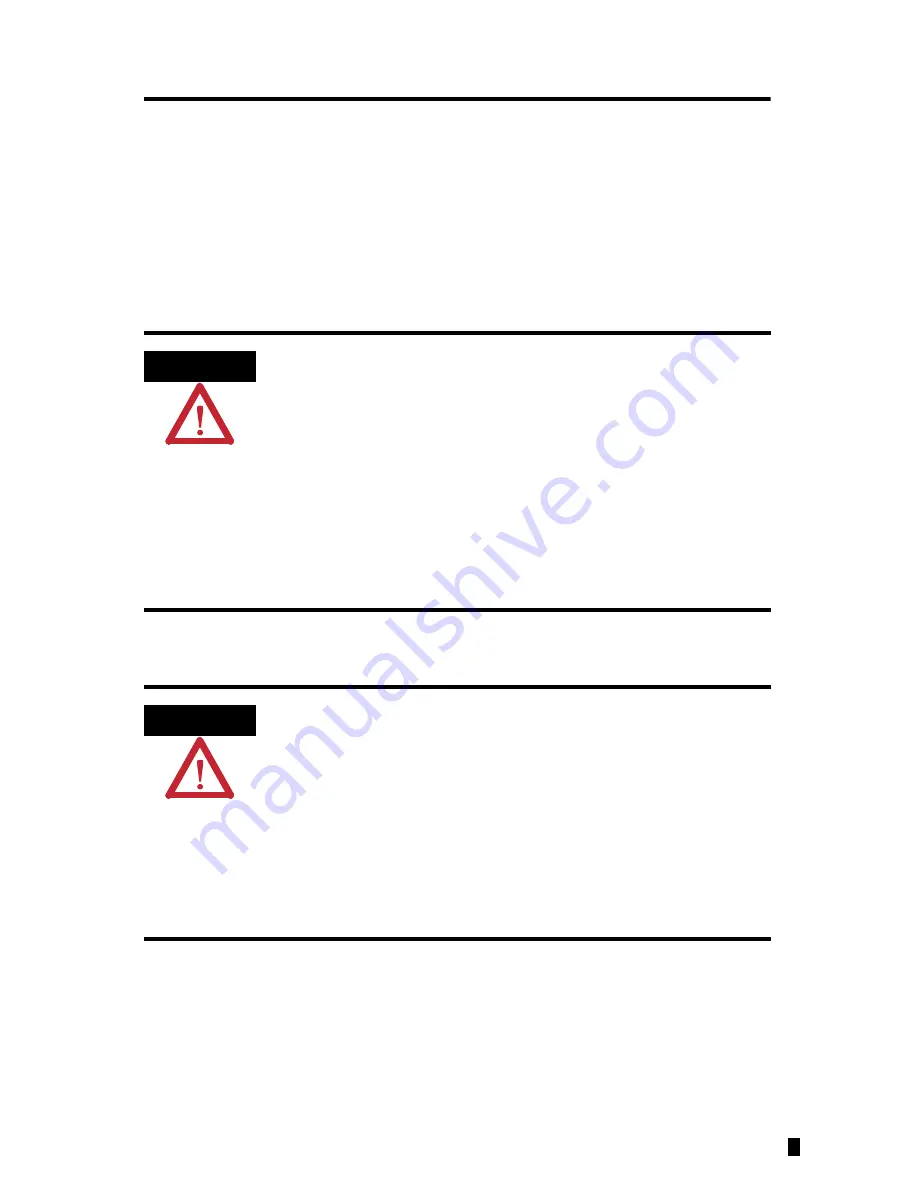
MicroLogix 1200 RTD/Resistance Input Module
3
Publication 1762-IN014B-EN-P - July 2013
Module Installation
1762 I/O is suitable for use in an industrial environment when installed in accordance with these
instructions. Specifically, this equipment is intended for use in clean, dry environments
(Pollution degree 2
(1)
) and to circuits not exceeding Over Voltage Category II
(2)
(IEC
60664-1).
(3)
Prevent Electrostatic Discharge
Remove Power
(1)
Pollution Degree 2 is an environment where, normally, only non-conductive pollution occurs except that occasionally a
temporary conductivity caused by condensation shall be expected.
(2)
Over Voltage Category II is the load level section of the electrical distribution system. At this level transient voltages are
controlled and do not exceed the impulse voltage capability of the product’s insulation.
(3)
Pollution Degree 2 and Over Voltage Category II are International Electrotechnical Commission (IEC) designations.
ATTENTION
Electrostatic discharge can damage integrated circuits or semiconductors
if you touch bus connector pins. Follow these guidelines when you handle
the module:
•
Touch a grounded object to discharge static potential.
•
Wear an approved wrist-strap grounding device.
•
Do not touch the bus connector or connector pins.
•
Do not touch circuit components inside the module.
•
If available, use a static-safe work station.
•
When not in use, keep the module in its static-shield box.
ATTENTION
Remove power before removing or installing this module. When you
remove or install a module with power applied, an electrical arc may occur.
An electrical arc can cause personal injury or property damage by:
•
sending an erroneous signal to your system’s field devices, causing
unintended machine motion
•
causing an explosion in a hazardous environment
•
causing permanent damage to the module’s circuitry
Electrical arcing causes excessive wear to contacts on both the module and
its mating connector. Worn contacts may create electrical resistance.