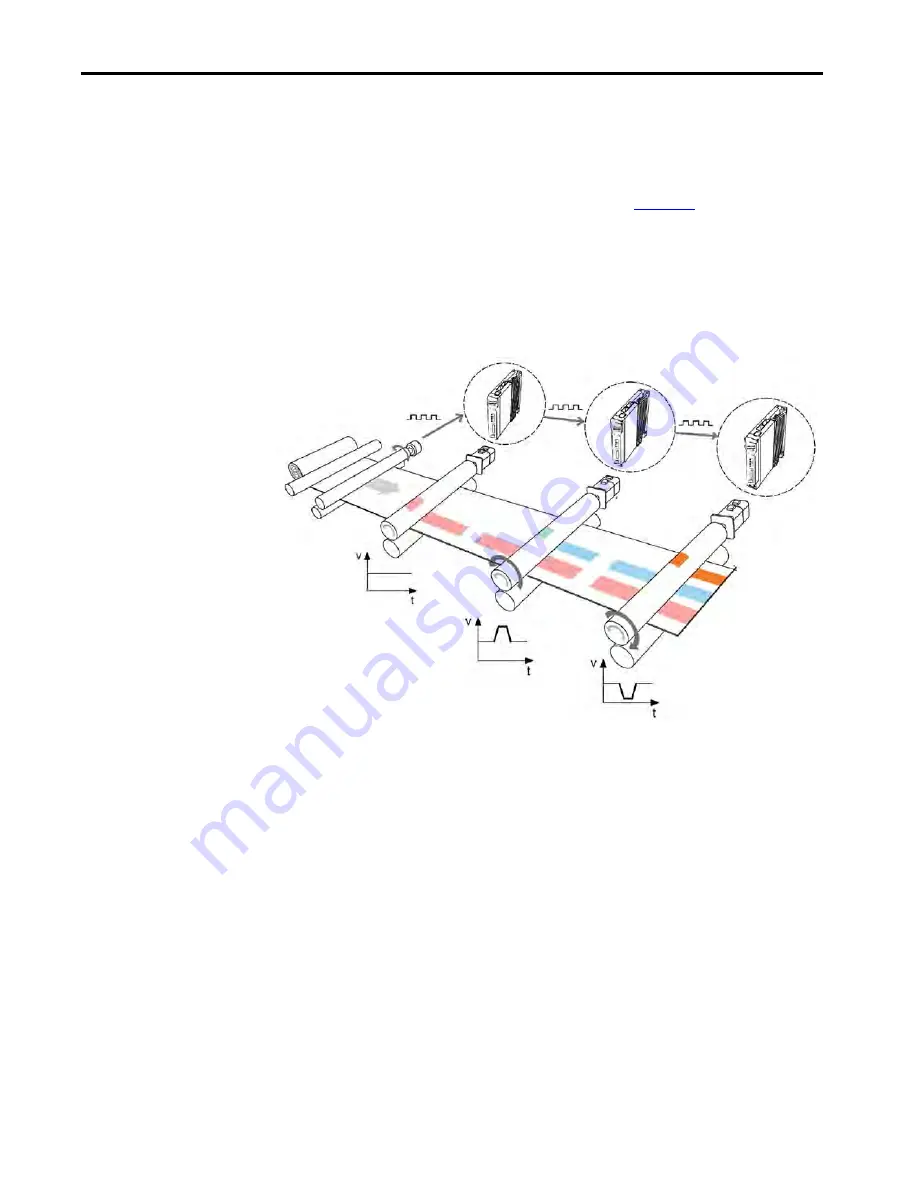
366
Rockwell Automation Publication 2198-UM004A-EN-P - October 2019
Chapter 12
Motion Control Applications
When the electronic cam is operating, if you want to change the slave axis speed or cam
phase, you can use the PR position increment command. The cam phase alignment
function and macro application of the rotary shear are used to correct the phase position
of the slave axis.
Taking the three-axis synchronous printing machine in
feeding axis is used as the master axis. The master axis pulse signals are transmitted to the
three slave axes whose E-Cam curve are the same. In general, the phases of these three
servo drives must be the same. If phases differ during the application, you can use this
phase correction function to perform the cam phase alignment. Generate a positive offset
phase by setting the forward incremental command and generate a reverse offset phase by
setting the reverse incremental command.
Figure 187 - E-Cam Phase Correction
E-Cam Troubleshooting
If the E-Cam does not work properly, you can check the following points for
detection:
• Control Mode — Make sure that the control mode is PR mode and the
servo drive is actually activated (Servo On).
• Pulse Source of Master Axis — Make sure that the pulse source of the
master axis (ID376 (P5.088.Y)) is set properly. The count of the number
of master axis pulses can be read by ID374 (P5.086)
ECamMasterAxisPosition or by monitor variable 059. When the input is
from terminal I/O connector, the count of the pulse command can be
observed by ID310 (P5.018) PulseCmdPosition. When the input is from
MFB terminal connector, the count of the auxiliary encoder pulses can be
observed by ID309 (P5.017) AuxEncoderPosition.
Summary of Contents for Kinetix 5100 2198-E1004-ERS
Page 499: ......