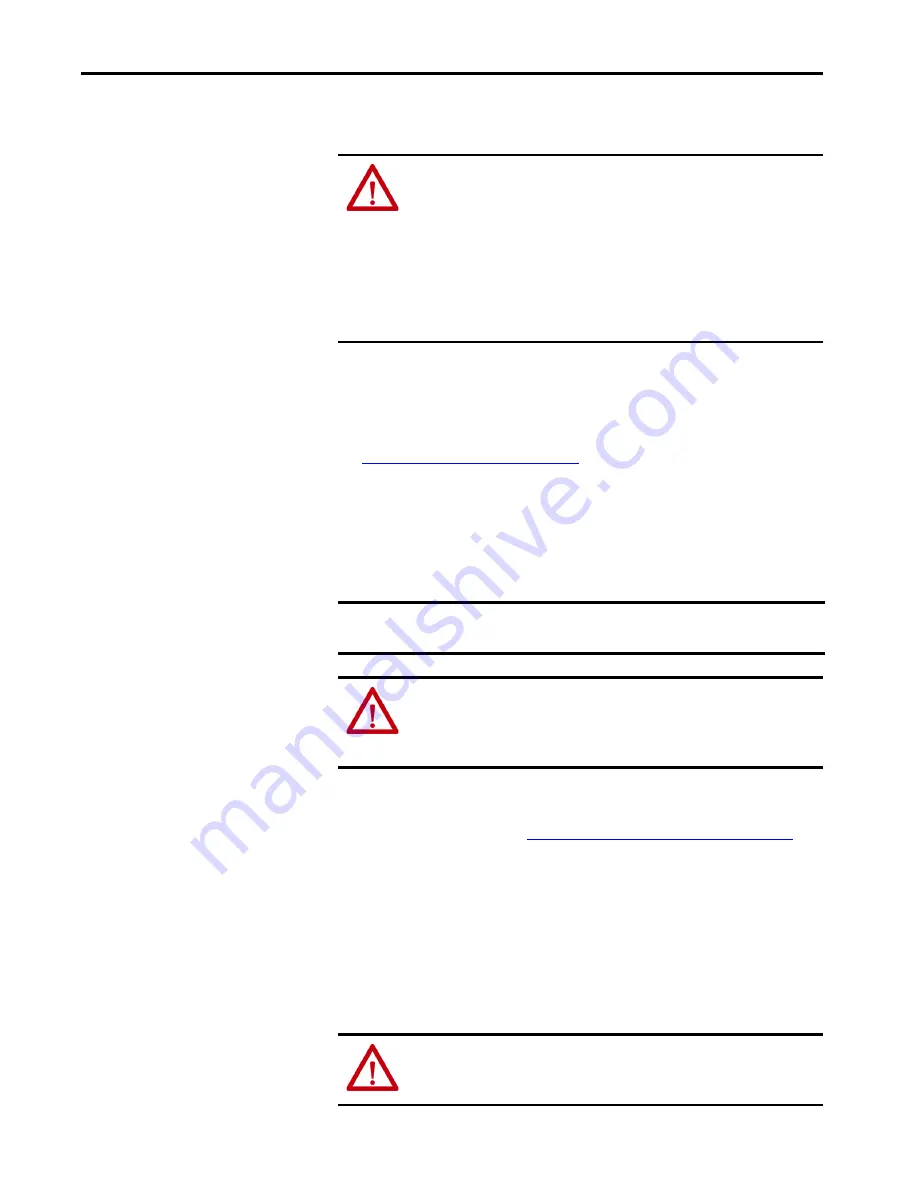
46
Rockwell Automation Publication 442L-UM005B-EN-P - April 2017
Chapter 4
Mounting
Response Time T
S
of the SafeZone Mini Device
The response time T
S
of the SafeZone Mini device depends on the following:
• The basic response time of the SafeZone Mini device.
• The multiple sampling set.
See
OSSD Response Times on page 84
Stationary Application in
Vertical Operation for
Hazardous Point Protection
Hazardous point protection is necessary if the operator must remain near the
dangerous state of the machine. Hand protection is required for hazardous
point protection.
To help protect the protective device against inadvertent adjustment or
manipulation, you must use the contour of the surroundings as a reference for
Use the Contour as a Reference on page 35
Minimum Distance
For hazardous point protection, a minimum distance must be observed
between protective field and hazardous point. This safety distance helps ensure
that the hazardous point can only be reached after the dangerous state of the
machine has been stopped completely.
ATTENTION:
The total response time of the SafeZone Mini device must not
be more than 80 ms for access protection.
If a critical response time is exceeded, a person may no longer be detected
under certain circumstances.
In specific cases agreed with the responsible authorities higher response
times may be allowed (for example by increasing the detection time
available by positioning the safety laser scanner at an angle). In this case,
verify that the areas the safety laser scanner cannot see are protected by
additional measures.
IMPORTANT
The SafeZone Mini device must be configured with a resolution of at least
40 mm (1.6 in.)
ATTENTION:
Never use the SafeZone Mini device for safety applications in
which finger protection is required.
Due to the finest possible resolution of 30 mm (1.2 in.), the SafeZone Mini
device is not suitable for finger protection.
ATTENTION:
Prevent reaching around or behind the protective field.
Always mount the safety laser scanner such that reaching around and behind
is impossible. Provide suitable additional precautions as necessary.
Summary of Contents for 442L-SFZNMN
Page 1: ...SafeZone Mini Safety Laser Scanner Catalog Number 442L SFZNMN User Manual OriginalInstructions...
Page 10: ...10 Rockwell Automation Publication 442L UM005B EN P April 2017 Preface Notes...
Page 60: ...60 Rockwell Automation Publication 442L UM005B EN P April 2017 Chapter 4 Mounting Notes...
Page 107: ......