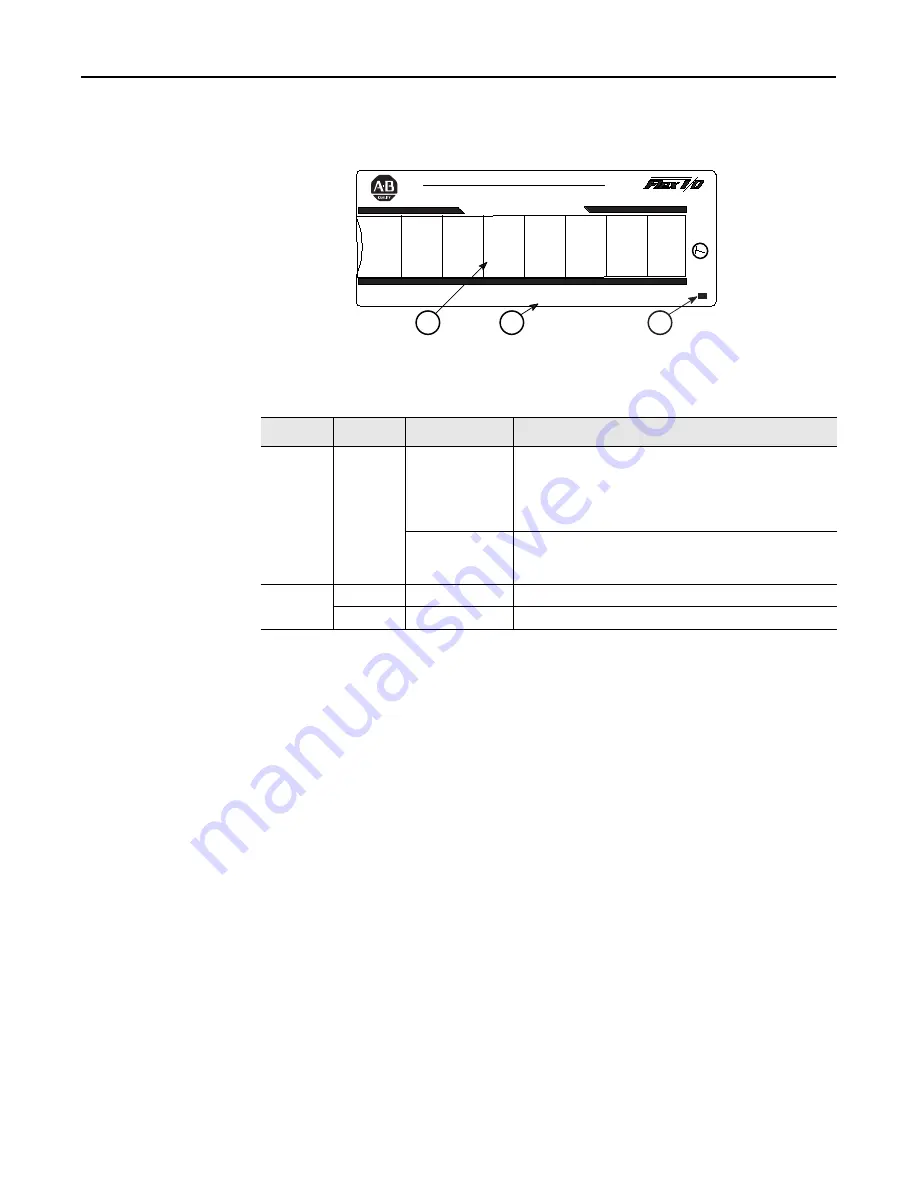
Publication 1794-6.5.12 - November 1997
How to Install Your Thermocouple/RTD/mV Input Module
2
-13
Module Indicators
The Thermocouple/RTD/mV module has one status indicator (PWR) that
is on when power is applied to the module and one fault indicator (F) for
each input.
Chapter Summary
In this chapter, we told you how to install your input module in an existing
programmable controller system and how to wire to the terminal base
units.
C
A
IN 0
IN 2
IN 4
IN 6
IN 1
IN 3
IN 5
IN 7
TC RTD INPUT 8 CHANNEL
3
1794-IRT8
Allen-Bradley
PWR
C
= Power Indicator - indicates power applied to module
A
= Insertable label for writing individual input designations
F
F
F
F
F
F
F
F
B
B
= Fault Indicator - indicates successful power up or noncritical fault
Indicator
Color
State
Meaning
Fault
Red
On
At power up – Channel 0 indicator lights at powerup until all
internal diagnostics are checked. After successful powerup, the
indicator goes off if no fault is present.
After successful powerup – Indicates a critical fault (diagnostic
failure, etc.)
Blinking (when
faults are enabled,
and bit set)
Indicates a noncritical fault (such as open sensor.) Input data
set to maximum, and indicator flashes at 1Hz rate.
Power
Off
Module not powered
Green
On
Module receiving power.