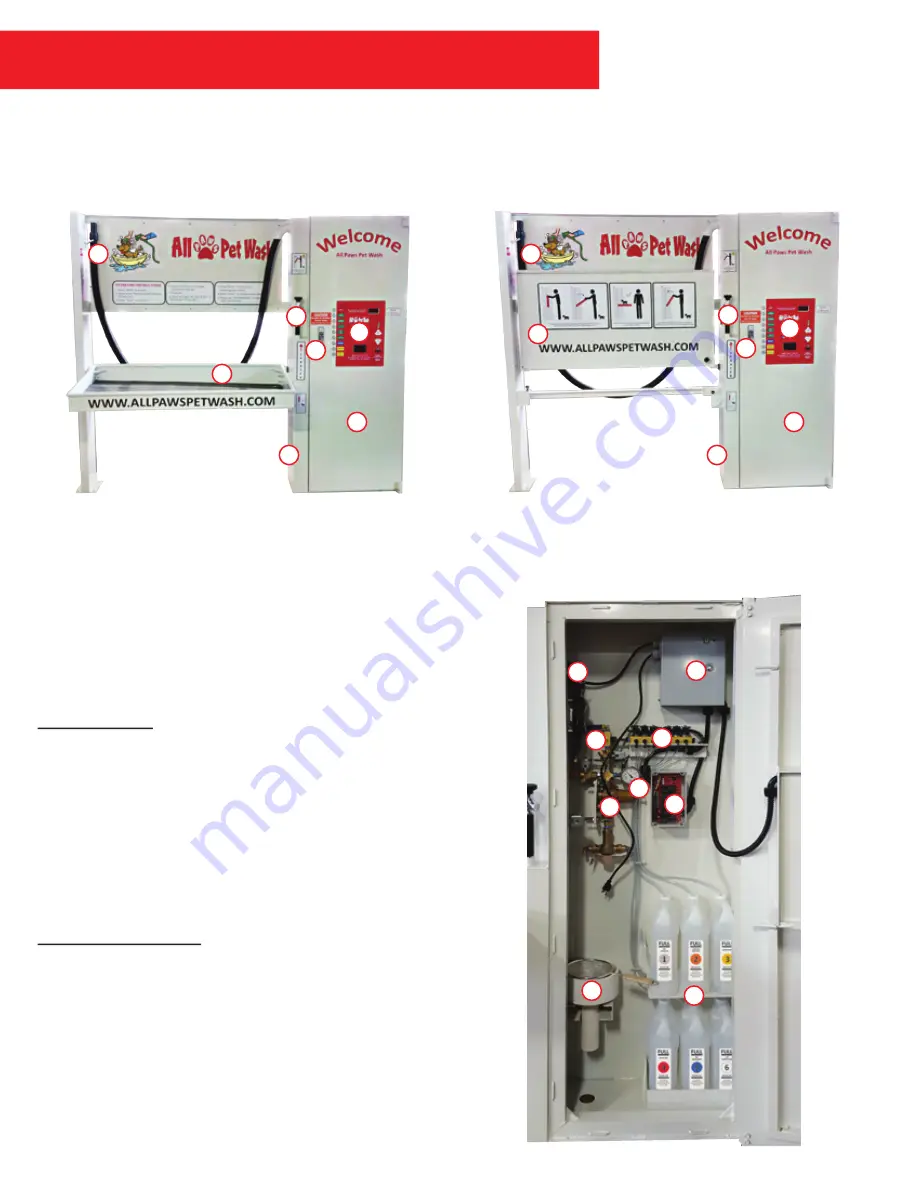
10
3
1. Equipment
Inside Cabinet
APW Flip-Tub (open)
APW Flip-Tub (closed)
Flip-Tub
A. Wash Tub
B. Cabinet
C. Sprayer
D. Dryer
E. Spray Control (9 button [shown] or 3 Button)
F. T-Handle Lock
G. Hot and Cold Hook-Ups
Inside Cabinet
1. Electrical Box
2. Water Column
3. Solenoid Valves
4. Flow Screw
5. Pressure Gauge
6. Blow Dryer
7. Relay Board
8. Soaps and Treatments
9. P-trap and Hair Strainer
Common Problems & Solutions
TROUBLESHOOTING
I. OVERVIEW
A
B
C
D
D
C
B
E
F
E
F
G
1
2
3
4
5
6
7
8
9
G
A
Problem:
No water pressure flow in the wash tub.
Solution:
Check water flow from incoming water line. Check pressure gauge on water column
in cabinet of APW. The unit requires 40-50 PSI to function properly. If you have sufficient flow
form the incoming water line, and 40-50 PSI of required pressure, you will need to adjust the
flow screw [
Reference image on page 3 / #4 Inside Cabinet
]. Start by counting the number of
turns it takes to close the screw when tightening (clockwise). The flow at the wash tub should
not be very low. Now loosen the screw (turning counter-clockwise) approximately 1
¾
- 2
turns, which should increase the flow. Keep in mind the more you loosen the flow screw to the
left the more you will increase the flow, but will be decreasing the suction for the shampoo.
Problem:
One of the shampoos or treatments in not flowing correctly.
Solution:
With the sprayer in the on and locked position, select the soap or treatment that’s
malfunctioning. If everything is working properly, you should have a low pressure flow with
soap and water. If you’re not receiving any soap along with the water, head to the equipment
room and locate the soap containers. Screw off the cap of the soap or treatment that’s mal-
functioning and examine the suction strainer. Make sure the screen is clean, if not, run the
suction strainer under some clean water. Next, examine the clear tube running from the soap
to the water column. If you are getting air bubbles in the tube, the soap is flowing but your
concentrate may be too diluted to see the soap coming out of the sprayer. If you are still
having issues you can increase the flow by loosening the material volume screw.
Problem:
Water is not pumping out of the hair strainer tank.
Solution:
The pump float switch is stuck. Simply unlodge the pump float. Rinse out tank as
needed.
Still having trouble?
1-800-537-8231
We have a large variety of helpful resources available
to you. Check out our Owners Hub on our website,
www.AllPawsPetWash.com. This page is password
protected, the password is:
Pawtastic!
(Case sensitive,
include the exclamation point)
You can also check out our Tech Support page and our
YouTube channel (YouTube.com/allpawspetwash) for
videos on how to set up your pet wash.
Feel free to give us a call if you don’t find what you’re
looking for online!