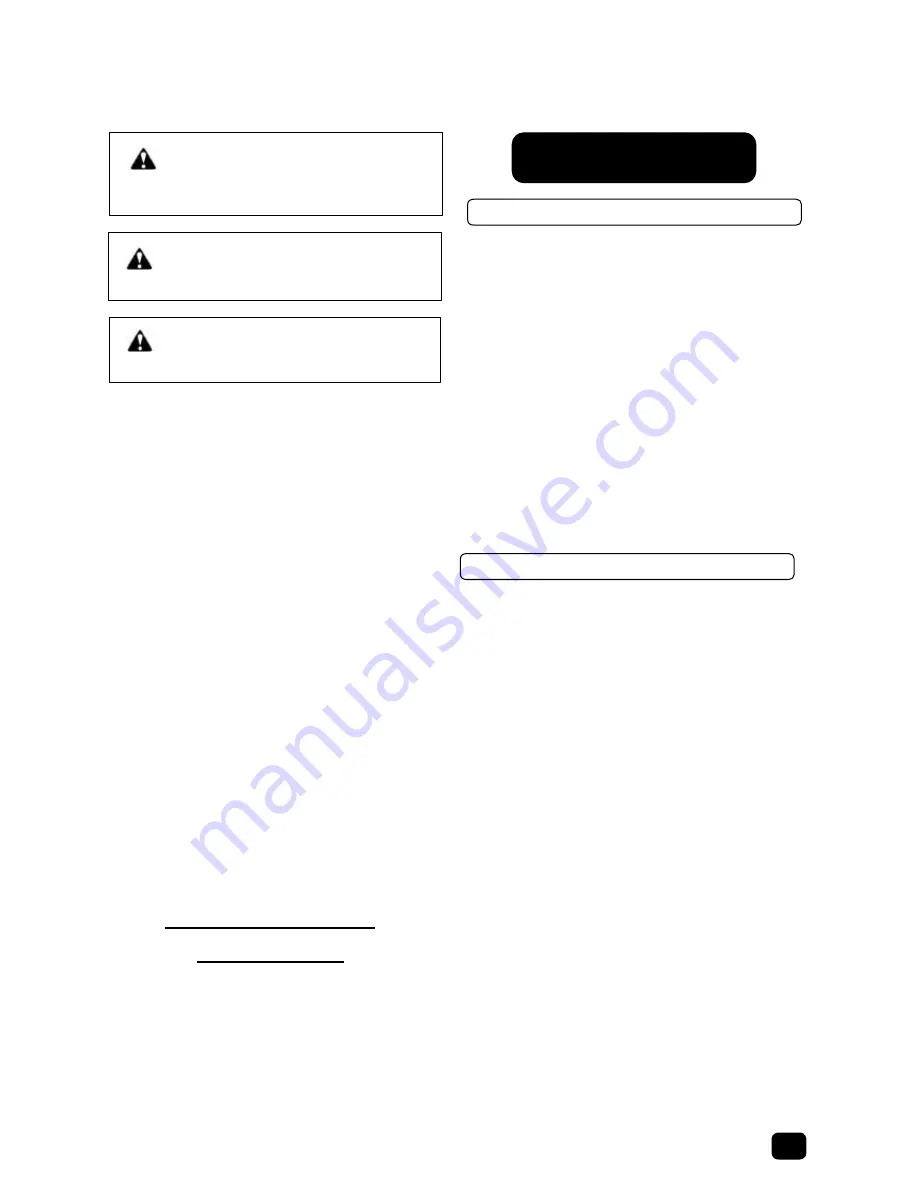
3
Safety & Installation
Safety Continued, Pre Start-Up, Start-Up
05-12-06 Z08-02830A
10. If a water leak is found,
DO NOT OPERATE THE
MACHINE.
Shut off the motor and repair.
11. Do not start the machine unless the gun assembly is
firmly gripped by the machine operator. Failure to do
this could result in injury from a flying hose and gun
assembly.
12. All guards, shields, and covers must be replace after
adjustment are made to prevent accidental contact
with hazardous parts.
13. If chemicals are used in conjunction with this
equipment, read and follow the product label
directions.
14. Do not refuel the machine while it is running or hot.
Allow it to cool sufficiently to prevent ignition of any
spilled fuel. .
15. Drive belts must be inspected and tightened
periodically to operate at optimum levels.
16. Inspect machine for damaged or worn components
and repair or replace to avoid potential hazards.
Do not operate the machine if any mechanical
failure is noted or suspected.
17. Always use the correct size spray tip specified in
the GENERAL section of the
MODEL
SPECIFICATIONS
or
MODEL EXPLODED VIEW
.
18. Do not start the engine until you have observed all
safety instructions and operating found in the
operating manual.
SAVE THESE SAFETY
INSTRUCTIONS
1.
The first time the machine is operated, after repairs
have been made, or if the machine has set for a period
of time (30 days or more) follow the following
procedures.
A. Check the tension of the belt (if so equipped)
per instructions in
MACHINE MAINTENANCE
.
B. Flush the machine per instructions in
MACHINE
MAINTENANCE
.
2.
CAUTION:
Always use the factory supplied wash
hose with your machine.
Do not
substitute other
hoses as a potential safety problem may develop.
CAUTION:
If machine has been exposed
to sub-freezing temperatures, it must be thoroughly
warmed to above freezing before operating. Failure
to warm machine can cause damage to the pump
packings and other components.
♦
Refer to the
MAINTENANCE SCHEDULE
for any
maintenance to be performed before
operation
♦
OIL LEVEL
: Check the oil level in the water pump.
♦
BELT
: Make sure belt tension and condition is as
specified in MACHINE MAINTENANCE.
♦
METERING VALVE (
if so equipped): Make sure the
metering valve is closed before operation. If air enters
the system through this valve, poor performance and
machine damage will occur. Refer to the metering
valve insert for proper operation.
♦
WATER SUPPLY
: This machine must have a water
supply meeting or exceeding the maximum discharge
volume specified in the PERFORMANCE section, and
a minimum water inlet pressure of 40 PSI /12.1KGM.
1. Turn water supply.
2. With the gun assembly in hand (on trigger gun models
hold the trigger gun valve in open position) and with
a good flow of water turn the switch to the “pump”
position.
CAUTION:
A good flow of water must be flowing
from the end of a gun for 30 seconds, before
proceeding. Lack of water can cause damage to
the water pump and like components.
4
Supersedes 08-19-04 Z08-02830A
WARNING:
Avoid the exhaust areas as they are
dangerously hot during and a short time after
operation.
WARNING:
Never put hands or fingers in wash
spray. DO NOT point the gun assembly toward
your body or at anyone else. Failure to do this could
result in serious injury.
WARNING:
DO NOT run engine in an enclosed
area. Exhaust gases contain carbon monoxide,
an odorless and deadly poison.
PRE START-UP
OPERATION
START-UP