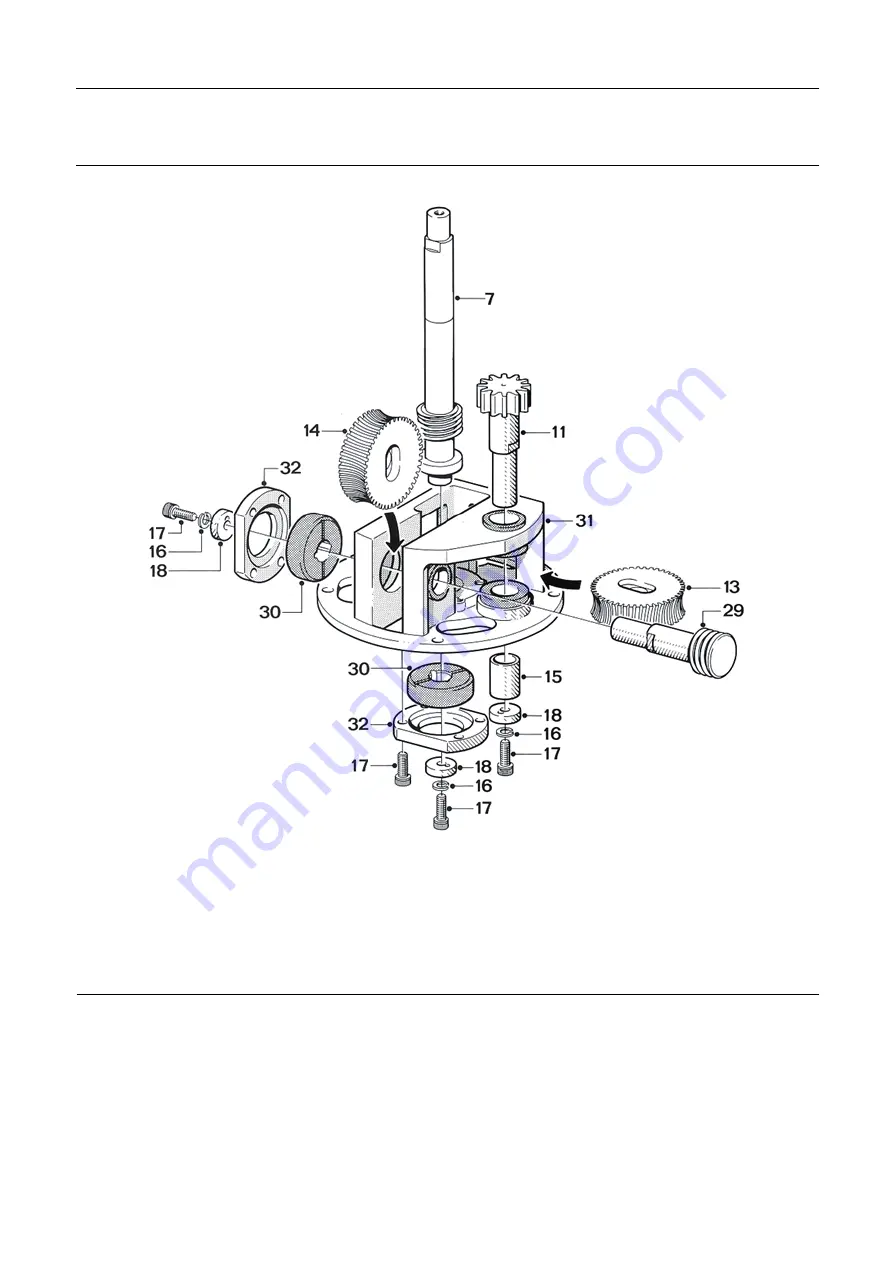
6 Maintenance
Gear Subassembly
TD523327
3. Insert 1st stage Worm wheel (pos. 14) and Horizontal shaft (pos. 29). Mount Washer (pos. 18), Spring washer (pos. 16)
and fix with Screw (pos. 17). Check rotation.
4. Insert Turbine shaft (pos. 7). Mount Washer (pos. 18), Spring washer (pos. 16) and fix with Screw (pos. 17). Use faces on
Turbine shaft to hold against rotation when tightening screw.
5. Hold Turbine shaft (pos. 7) against 1st stage Worm wheel and tighten Screws (pos. 17) in Horizontal shaft (pos. 29) and
Pinion (pos. 11). Check rotation on Turbine shaft.
31
Summary of Contents for Toftejorg MultiJet 50
Page 2: ......
Page 23: ...6 Maintenance Top Assembly 23 ...
Page 25: ...6 Maintenance Bottom Assembly TD523346 25 ...
Page 27: ...6 Maintenance Hub Assembly TD523347 27 ...
Page 29: ...6 Maintenance Stem Subassembly TD523326 29 ...
Page 35: ...6 Maintenance Replacement of Ball races Support TD523329 Support TD52333 35 ...
Page 48: ...10 Parts list and drawing service kits and tools 10 1 MultiJet 50 with 2 nozzles 4109 0024 48 ...
Page 50: ...10 Parts list and drawing service kits and tools 10 2 MultiJet 50 with 4 nozzles 4109 0025 50 ...