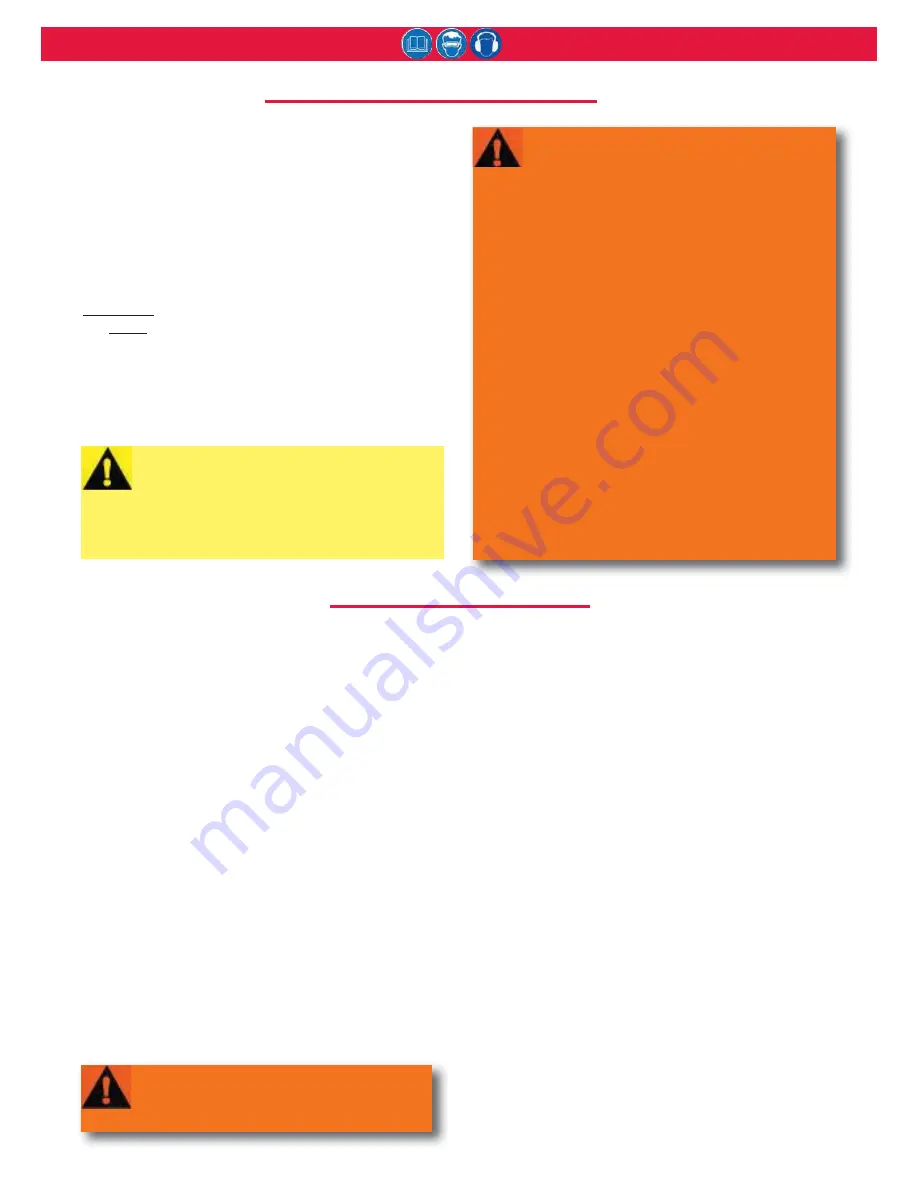
2024 series Tooling
(HK1077)
Alcoa Fastening Systems
7
S
ERVICING
THE
TOOL
GENERAL
1. The effi ciency and life of any tool depends
upon proper maintenance. Regular inspection
and correction of minor problems will keep tool
operating effi ciently and prevent downtime. The
tool should be serviced by personnel who are
thoroughly familiar with how it operates.
2. A clean, well-lighted area should be available for
servicing the tool. Special care must be taken
to prevent contamination of pneumatic and
hydraulic systems.
3. Proper hand tools, both standard and special,
must be available.
4. All parts must be handled carefully and
examined for damage or wear. Always replace
Seals, when tool is disassembled for any reason.
Components should be disassembled and
assembled in a straight line without bending,
cocking, or undue force. Disassembly and
assembly procedures outlined in this manual
should be followed.
5.
Service Parts Kit 2024KIT
includes consumable parts
and should be available at all times. Other
components,
as experiece dictates, should also be available.
DAILY
1. If a Filter-Regulator-Lubricator unit is not being
used, uncouple air disconnects and put a few
drops of Automatic Transmission Fluid or light
oil into the air inlet of the tool. If the tool is in
continuous use, put a few drops of oil in every two
to three hours.
2. Bleed the air line to clear it of accumulated dirt or
water before connecting air hose to the tool.
3. Check all hoses and couplings for damage or air
leaks, tighten or replace if necessary.
4. Check the tool for damage or air/hydraulic leaks,
tighten or replace if necessary.
5. Check the nose assembly for tightness or
damage, tighten or replace if necessary.
6. Check stroke periodically, if stroke is short add
oil.
WEEKLY
1. Disassemble, clean, and reassemble nose
assemblies per applicable nose assembly
instructions.
2. Check the tool and all connecting parts for
damage or oil/air leaks, tighten or replace if
necessary.
as experiece dictates, should also be available.
WARNING: Inspect tool for damage or
wear before each use. Do not operate if
damaged or worn, as severe personal
injury may occur.
O
PERATING
I
NSTRUCTIONS
BLIND FASTENER INSTALLATION:
The fastener may be placed either in the work hole or in
the end of the nose assembly. In either case, tool and nose
assembly must be held against work and at right angles to
it. Depress trigger and hold it depressed un l fastener is
installed and pintail breaks. Release trigger.
MAGNA GRIP® FASTENER INSTALLATION:
Place pin in work-hole and place collar over pin. See
WARNINGS
. (If collar has only one tapered end, that
end
MUST
be out toward tool.) Hold pin in hole. Push
nose assembly onto pin protruding from collar un l anvil
touches collar. Press trigger and hold down un l collar is
swaged and pintail breaks. Release trigger.
WARNINGS:
Inspect tool for damage or wear before
each use. Do not operate if damaged or
worn as severe personal injury may occur.
Pulling on a pin (fastener) without a collar,
or with collar chamfer against workpiece,
may result in pin becoming a high speed
projectile when pin grooves are stripped
or pintail breaks off. Fatal or severe injury
is possible to anyone in the pins line of
fl ight. This includes pins that ricochet.
Broken pintails eject from defl ector with
speed and force. Be sure pintail defl ector
is directed safely away front operator
or the personnel in the area. Ejecting
pintails striking anyone may cause serious
personal injury. For Models 202B and
202V, pintail bottles must always be used.
Replace damaged pintail defl ectors and
bottles as serious personal injury may
occur from pintails when using these
defective parts.
CAUTION: Remove excessive gap from
between sheets for enough of the pintail
to stick out of the collar for all of the
jaw teeth to grip into the pintail grooves.
Jaws not fully gripping pintail grooves
will be stripped or broken
.