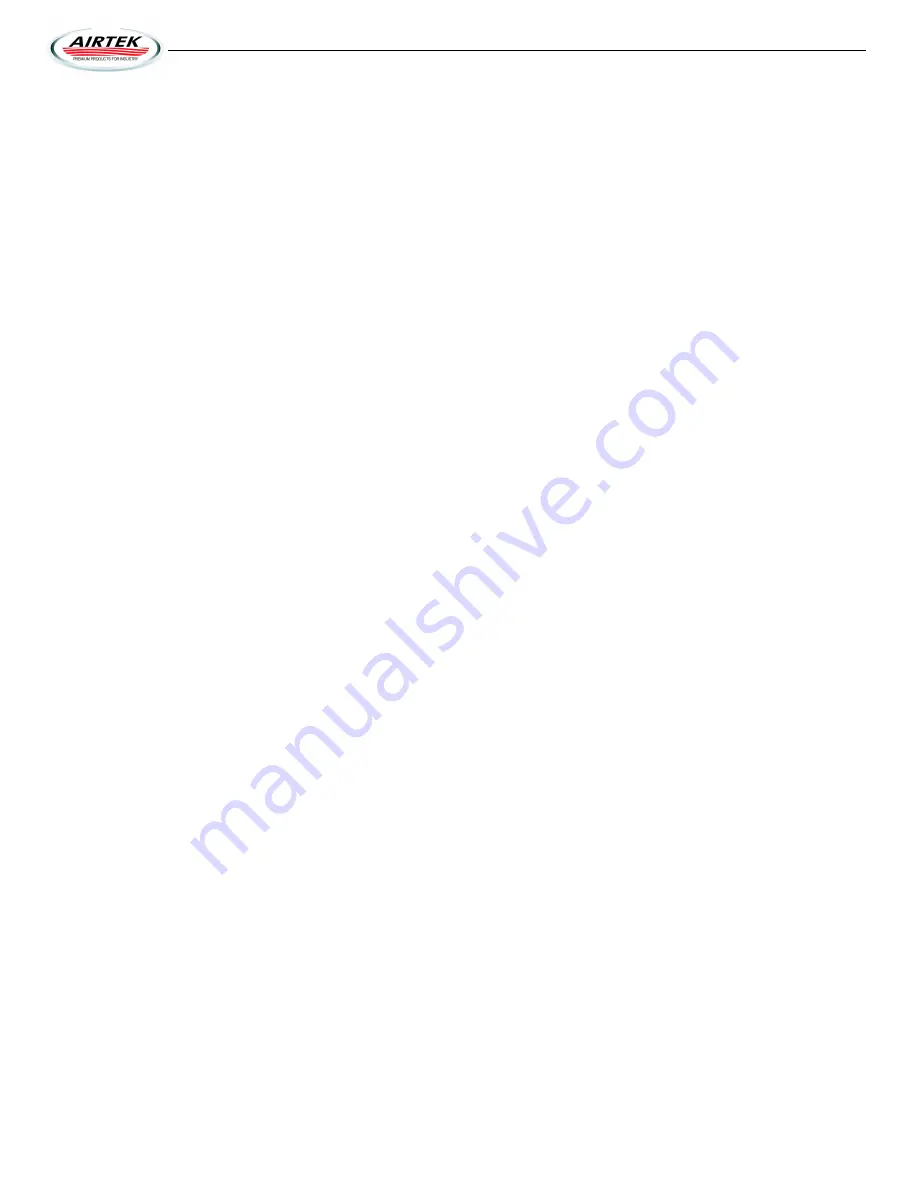
Pg. -5-
AIRTEK 4087 WALDEN AVENUE, LANCASTER, NY 14086 Tel: (716) 685-4040 Fax: (716) 685-1010
3.
A.
START-UP
Please read and understand the entire manual before
operating the dryer.
Check and read over wiring diagram that pertain to your unit
and make sure the correct power supply is connected, but
do not energize circuit at this time. Provide proper short
circuit protection. Follow all applicable codes.
Before starting the dryer your compressor should be
running, your air system pressurized and the dryer by-
passed and not yet pressurized.
SLOWLY open the inlet isolation valve admitting com-
pressed air to the dryer. It is important to pressurized the
dryer slowly to prevent fluidization of the desiccant bed.
The dryer outlet isolation valve should be closed at this
time.
SLOWLY open dryer outlet isolation valve. At this point all
valves are in their “normal” positions, air is flowing through
both towers and downstream.
Close the dryer bypass valve. Bypass valve must be bubble
tight to prevent moisture from migrating around the dryer
and contaminating the dry air outlet.
It is recommended that the dryer be started without the
mufflers installed. This will expedite removal of excess
desiccant dust and prevent premature clogging of the
exhaust mufflers.
CAUTION: USE EAR AND EYE PROTECTION WHEN
OPERATING DRYER WITHOUT MUFFLERS. EXCESSIVE
NOISE WILL BE CREATED. DUST AND PARTICLES
FROM THE SURROUNDING AREA MAY BECOME
AIRBORNE. OPERATION WITHOUT MUFFLERS EX-
CEEDS OSHA LIMITS.
Checking the cycle setting. It should normally be set to the
standard 10-minute cycle.
Energize the electrical circuit. The dryer will begin to cycle.
At this point one tower will exhaust its air to atmosphere.
See cautionary statement above.
Check and adjust the setting of the purge flow in accor-
dance with the specifications for your dryer. See Section 8.
Purge flow is typically 15% of design flow for the dryer. Note
that even if you are operating under a light load the purge
can not be reduced if you are operating in the PowerLoc
mode, CycleLoc mode, or a fixed timed cycle other than the
standard 10-minute cycle.
Never service the Dryer or Filters without first relieving
pressure.
Check all air connections for leaks and tighten as required.
Downstream air leaks will affect dewpoint. Bypass air leaks will
affect dewpoint. Only soft seat bypass valves may be used.
Dryer will not perform without proper pre-filtration, conden-
sate drainage, and purge flow. Dryers may require up to 48
hours of operation to reach normal operating dewpoints.
Therefore, indicators and/or alarms should not be recog-
nized until that time. Applications requiring dewpoints lower
than –40, or with nonstandard operating conditions, may
require additional time to reach equilibrium. Exhaust valves
and/or exhaust mufflers may have to be cleaned due to
dusting in shipping and start-up.
4.
A.
SHUTDOWN PROCEDURE:
1.
Allow the dryer to reach a repressurization step & fully
repressurize.
2.
While fully repressurized, remove power from the dryer.
After shutdown airflow will continue through one tower, if
there is downstream demand, the dryer should be immedi-
ately bypassed to prevent loading of the beds while the
dryer is out of service.
3.
Always remove all pressure & disconnect all power
before servicing the dryer.
4.
If a PowerLoc is installed and the dryer will be out of
service for an extended period of time, remove the probe
and store in a safe, dry location. The probe will be dam-
aged if exposed to prolonged periods of saturation condi-
tions.
No other special procedures are required.
5.
A.
THEORY OF OPERATION:
Adsorption is the process of removing water VAPOR from
the air to be dried. All condensed liquid water should be
removed from the inlet air stream prior to reaching the dryer
by suitable separators, traps, filters and drains. The dryer
can not be burdened with liquid condensate carry-over.
All Desiccants are adversely affected by oil, oil aerosols,
dirt, rust, scale or liquid water. Effective pre-filtration in
conjunction with automatic condensate drainage is a must
for proper dewpoint depression and long desiccant life.
The saturated inlet air is alternately cycled through each of
the two desiccant beds. One bed is “on-line” at full line
pressure and flow, adsorbing water vapor from the satu-
rated inlet air. This is the drying bed. The other bed is “off-
line” at atmospheric pressure (0 PSIG) being regenerated
by a depressurized portion of the dried outlet air (purge air).
This is the regenerating bed.
The quantity of purge air for a standard pressure dryer is
approximately 15% of inlet design flow. This air is taken
from the dry air outlet, directed through the purge flow
controls, desiccant bed, and finally exhausted to atmo-
sphere to accomplish regeneration. Purge air consumption
is typically the largest cost involved with operating a
heatless desiccant air dryer. (Purge air is “nonrecoverable”
and the air system in question must be designed to allow for
this usage.)