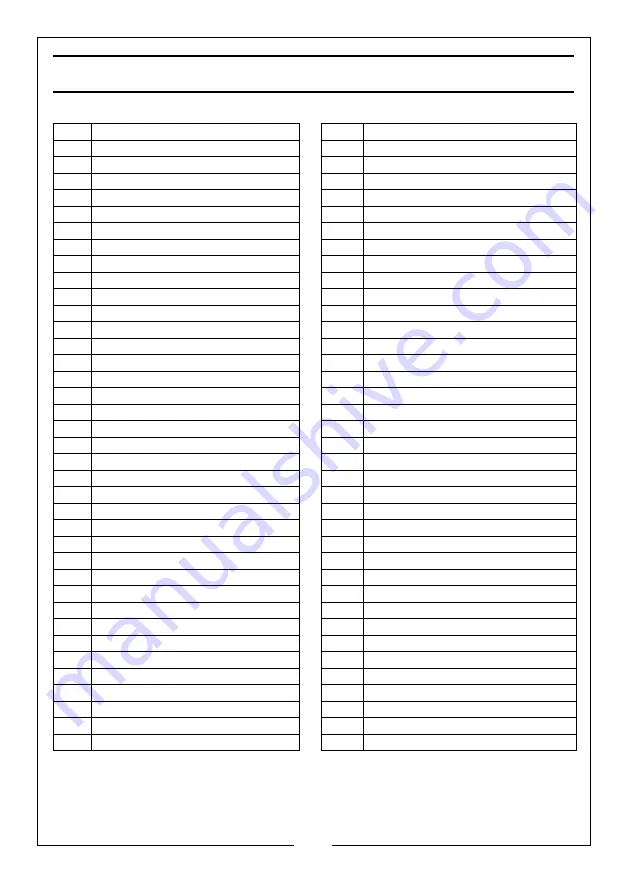
22
PARTS LIST
1
CRANKCASE
39
FAN
2
CRANKSHAFT
40
BEARING SEAT
3
OILSEAL GASKET
41
WAVE GASKET
4
FRONT COVER
42
STATOR
5
OIL DRAIN PLUG
43
BALL BEARING
6
OIL SIGHTGLASS SEAL
44
ROTOR
7
OIL SIGHTGLASS
45
BALL BEARING
8
BOLT
46
OIL SEAL
9
BREATHER
47
OVERLOAD PROTECTOR
10
SCREW
48
TANK
11
CONNECTING ROD
49
HOLE PLUG
12
RETAINING RING
50
NUT
13
PISTON PIN
51
SPRING WASHER
14
PISTON
52
FLAT WASHER
15
OIL RING
53
WHEEL
16
COMPRESSION RING
54
BOLT
17
CYLINDER GASKET
55
DRAIN VALVE
18
CYLINDER
56
BOLT
19
STUD BOLT
57
FOOT
20
SPRING WASHER
58
FLAT WASHER
21
NUT 59
SPRING
WASHER
22
VALVE PLATE GASKET
60
NUT
23
VALVE PLATE
61
HANDLE PLUG
24
VALVE REED
62
SAFETY VALVE
25
ALUMINUM GASKET
63
PRESSURE SWITCH
26
CYLINDER HEAD GASKET
64
PRESSURE GAUGE (50 MM)
27
ELBOW
65
CONNECTOR
28
CYLINDER HEAD
66
REGULATOR
29
HEX BOLT
67
BALL VALVE
30
AIR FILTER
68
PRESSURE GAUGE (40 MM)
31
NUT
69
NUT
32
CAPACITOR
70
TUBE
33
FLAT WASHER
71
CHECK VALVE
34
SPRING WASHER
72
NUT
35
LONG BOLT
73
EXHAUST PIPE
36
SHROUD
74
POWER CABLE
37
BOLT
75
MOTOR CABLE
38
CIRCLIP
Summary of Contents for 1499490
Page 19: ...19 DECLARATION OF CONFORMITY ...
Page 20: ...20 DECLARATION OF CONFORMITY ...
Page 21: ...21 COMPONENT PARTS ...
Page 23: ...23 RELATED PRODUCTS AVAILABLE ...
Page 24: ......