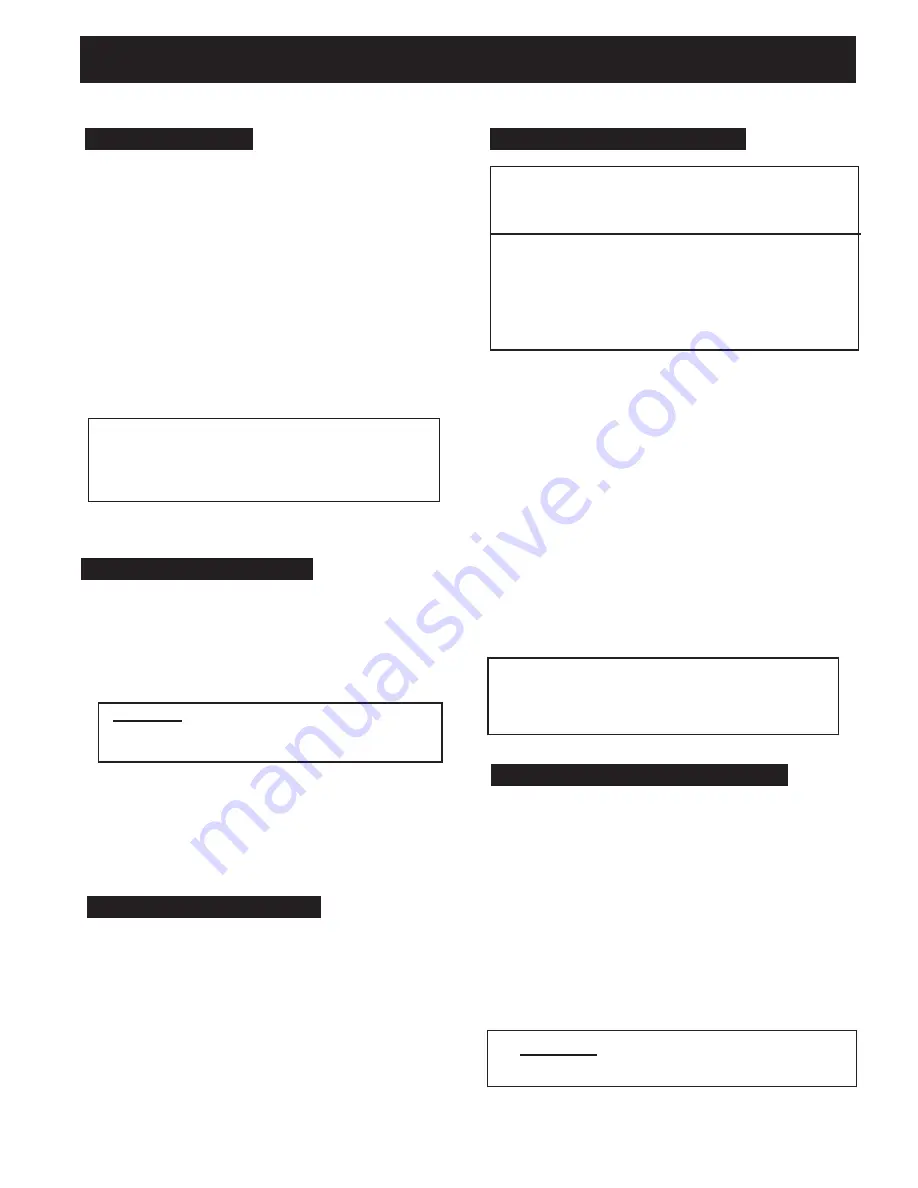
8
9
4. Prime the Pump
a. Allow pump to operate until paint comes from gun.
b. Release the trigger and engage the gun safety latch.
c. Turn Prime Valve OPEN to the prime position
ensuring the pressure is released from the system.
d. Turn Pressure Control Knob to minimum
pressure.
e. Install spray tip onto gun.
f. Close the prime valve to the pressure position.
g. Turn the pressure control knob to desired spray
pressure.
h. Disengage the gun safety lock and you are ready
to start spraying.
5. Adjusting the Pressure
a. Turn the Pressure Control Knob clockwise to
increase pressure and counterclockwise to
decrease pressure.
b. Always use the lowest pressure necessary to
completely atomize the material.
CAUTION - Operating the sprayer at higher
pressure than needed wastes material, causes
early tip wear and shortens sprayer life.
c. If more coverage is needed use a larger tip rather
than increasing the pressure.
d. Check the spray pattern. The tip size and angle
determines the pattern width and flow rate.
6. Reducing Clutch Wear
a. The first 50 feet of airless spray hose should be 3/8",
the larger diameter works as a pulsation damper and
saves unnecessary cycling of the clutch. A minimum
of 100 feet of hose should be used.
b. Adjust the Engine Speed and Pump Pressure.
First set the throttle lever to the maximum RPM
setting (fully left). Trigger the gun onto a test paper
to check the spray pattern and atomization. Adjust
the Pressure Control Knob until you get a good
pattern. Reduce RPM of engine to support pressure
without laboring engines.
WARNING: If you spray into the paint bucket,
always use the lowest spray pressure and
maintain firm metal to metal contact between
gun and container. See page 7, Fig 5.
IMPORTANT WARNING
Always follow the Pressure Relief Procedure on page 8
before perfoming any service or maintenance procedure.
WARNING:
Never hold your body, fingers,
or hand in a rag in front of the spray tip when
cleaning or checking it for a cleared tip. Always
point the gun toward the front or into a waste
container when checking to see if the tip is
cleared or when using a self-cleaning tip.
a. Follow the Pressure Relief Procedure on page 10.
b. Clean the front of the tip frequently (with toothbrush
only) during the day to keep material from building up
and clogging the tip.
c. To clean and clear a tip if it clogs, refer to the separate
instruction manual received with your gun and nozzle.
There is an easy way to keep the outside of the tip clean from
material build-up:
Every time you stop spraying, for even a minute, lock the
gun and submerge the gun into a small bucket of thinner
comparable with the material sprayed. Thinner will dissolve
the build up of paint on the outside of tip, tip guard and gun
much more effectively than if the paint dries out completely.
8. When Shutting Off the Sprayer
a. Whenever stop spraying, even for a short break, fol-
low the Pressure Relief Procedure Warning on page
10.
b. Clean the tip and gun as recommended by your
separate gun instruction manual.
c. Flush the sprayer at the end of each work day if the
material you are spraying is waterbased, or if it could
harden in the sprayer overnight. See "Flushing" page
6. Use a compatible solvent to flush, then fill the pump
and hoses with an oil based sovent such as mineral spir-
its.
d. For long term shutdown or storage, refer to page 6.
WARNING
-
Be sure to relieve pressure in the
pump after filling with mineral spirits.
WARNING:
Clogged standard flat tip - clean
only after the tip is removed from the gun.
Follow the Pressure Relief Procedure Warning
on Page 10.
7. Cleaning a Clogged Tip
STARTING UP - continued