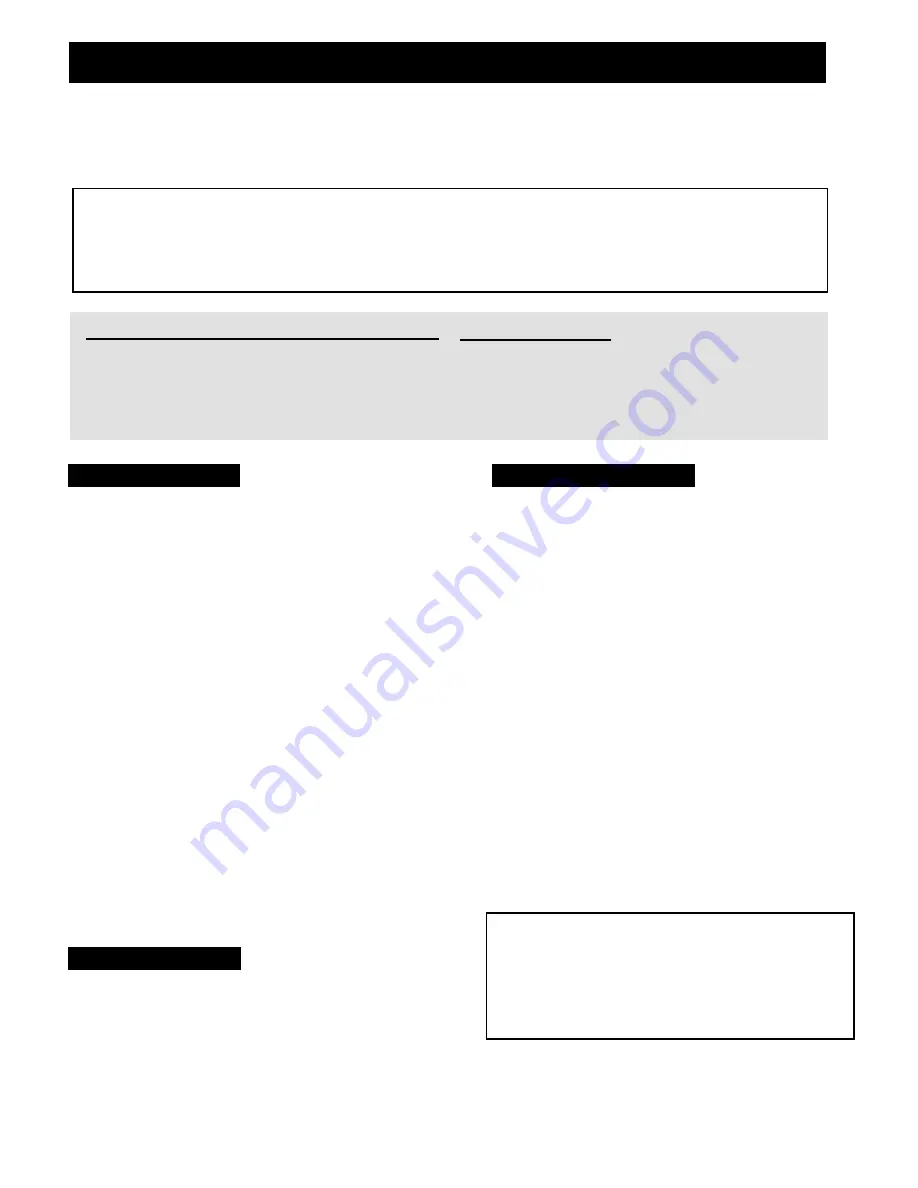
2
3
SAFETY WARNINGS
NOTE: United States Government safety
standards have been adopted under the
Occupational Safety & Health Act. These
standards, particularly the General Standards,
Part 1910 & Construction Standards, Part 1926
should be consulted.
DO NOT USE HALOGENATED SOLVENTS IN THIS SYSTEM.
The prime valve, and most airless guns have aluminum parts and may explode. Cleaning agents, coatings, paints or adhesives
may contain halogenated hydrocarbon solvents. DON'T TAKE CHANCES! Consult your material suppliers to be sure. Some of
the most common of these solvents are: Carbontetrachloride, Chlorobenzene, Dichloroethane, Dichloroethyl Ether,
Ethylbromide, Ethylchloride, Tethrachloethane. Alternate valves and guns are available if you need to use these solvents.
HIGH PRESSURE SPRAY CAN CAUSE EXTREMELY SERIOUS INJURY.
Handle as you would a loaded firearm.
Follow the PRESSURE RELIEF PROCEDURE
.
MEDICAL ALERT
-
Airless Spray Wounds
If any fluid appears to penetrate your skin, get
EMERGENCY MEDICAL CARE AT ONCE.
DO NOT TREAT AS A
SIMPLE CUT
.
Tell the doctor exactly what fluid was injected
.
NOTE TO PHYSICIAN
: Injection in the skin is a traumatic
injury.
It is important to treat the injury surgically as
soon as possible. DO NOT DELAY treatment to research
toxicity.
Toxicity is a concern with some exotic coatings injected
directly into the blood stream. Consultation with a plastic surgeon
or reconstructive hand surgeon may be advisable.
GENERAL PRECAUTIONS
•
NEVER
alter equipment in any manner.
•
NEVER
smoke while in spraying area.
•
NEVER
spray highly flammable materials.
•
NEVER
use around children.
•
NEVER
allow another person to use sprayer unless
he is thoroughly instructed on its safe use and
given this operators manual to read.
•
ALWAYS
wear a spray mask, gloves and protective
eye wear while spraying.
•
ALWAYS
ensure fire extinquishing equipment is
readily available and properly maintained
.
NEVER LEAVE SPRAYER UNATTENDED
WITH PRESSURE IN THE SYSTEM.
FOLLOW PRESSURE RELIEF
PROCEDURES.
• Fluids under high pressure from spray or leaks can
penetrate the skin and cause extremely serious injury,
including the need for amputation.
•
NEVER
point the spray gun at anyone or any part of
the body.
•
NEVER
put your hand or fingers over the spray tip. Do
not use a rag or any other materials over your fingers.
Paint will penetrate through these materials & into the hand.
•
NEVER
try to stop or deflect leaks with your hand or body.
•
ALWAYS
have the tip guard in place when spraying.
•
ALWAYS
lock the gun trigger when you stop spraying.
•
ALWAYS
remove tip from the gun to clean it.
•
NEVER
try to "blow back" paint, this is not an air spray
sprayer.
•
ALWAYS
follow the
PRESSURE RELIEF
PROCEDURE
before cleaning or removing the spray tip or servicing any
system equipment.
• Be sure the equipment safety devices are operating properly
before each use.
• Tighten all of the fluid connections before each use.
MEDICAL TREATMENT
\
• If any fluid appears to penetrate your skin, get
EMERGENCY
CARE AT ONCE! DON'T TREAT AS A SIMPLE CUT.
• Go to an emergency room immediately.
• Tell the doctor you suspect an injection injury.
• Tell him what kind of material you were spraying with
and have him
read NOTE TO PHYSICIAN above.
INJECTION HAZARD
Summary of Contents for LP 400
Page 24: ...22 Packing Replacement Procedures Continued FIGURE 16 FIGURE 15...
Page 30: ...28 NOTES...
Page 31: ...29 NOTES...