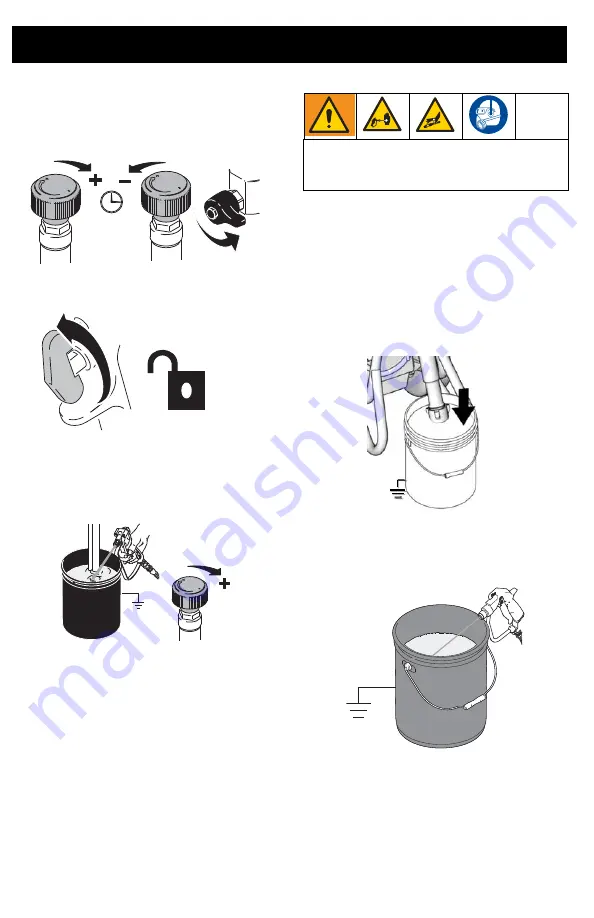
Startup (Electric Models)
20
3A4102C
7.
Increase pressure enough to start
hydraulic motor stroking and allow fluid
to circulate for 15 seconds; turn pressure
down, turn prime valve horizontal.
8.
Take spray gun trigger safety OFF.
9.
Hold gun against grounded metal
flushing pail. Trigger gun and increase
fluid pressure slowly until pump runs
smoothly.
10. Inspect fittings for leaks. If leaks occur,
turn sprayer OFF immediately. Perform
Tighten leaky fittings. Repeat
Startup
procedure steps 2-8. If no leaks,
continue to trigger gun until system is
thoroughly flushed.
11. Place displacement pump in paint pail.
12. Trigger gun again into flushing fluid pail
until paint appears.
13. Assemble Tip and Guard, page 21.
15
SEC
WLE
ti29213a
FLUSH
WLD
High-pressure spray is able to inject toxins
into the body and cause serious bodily
injury. Do not stop leaks with hand or rag.
ti9695a
ti18248a
Summary of Contents for HSS9950
Page 41: ...Notes 3A4102C 41 Notes...
Page 42: ...Notes 42 3A4102C Notes...