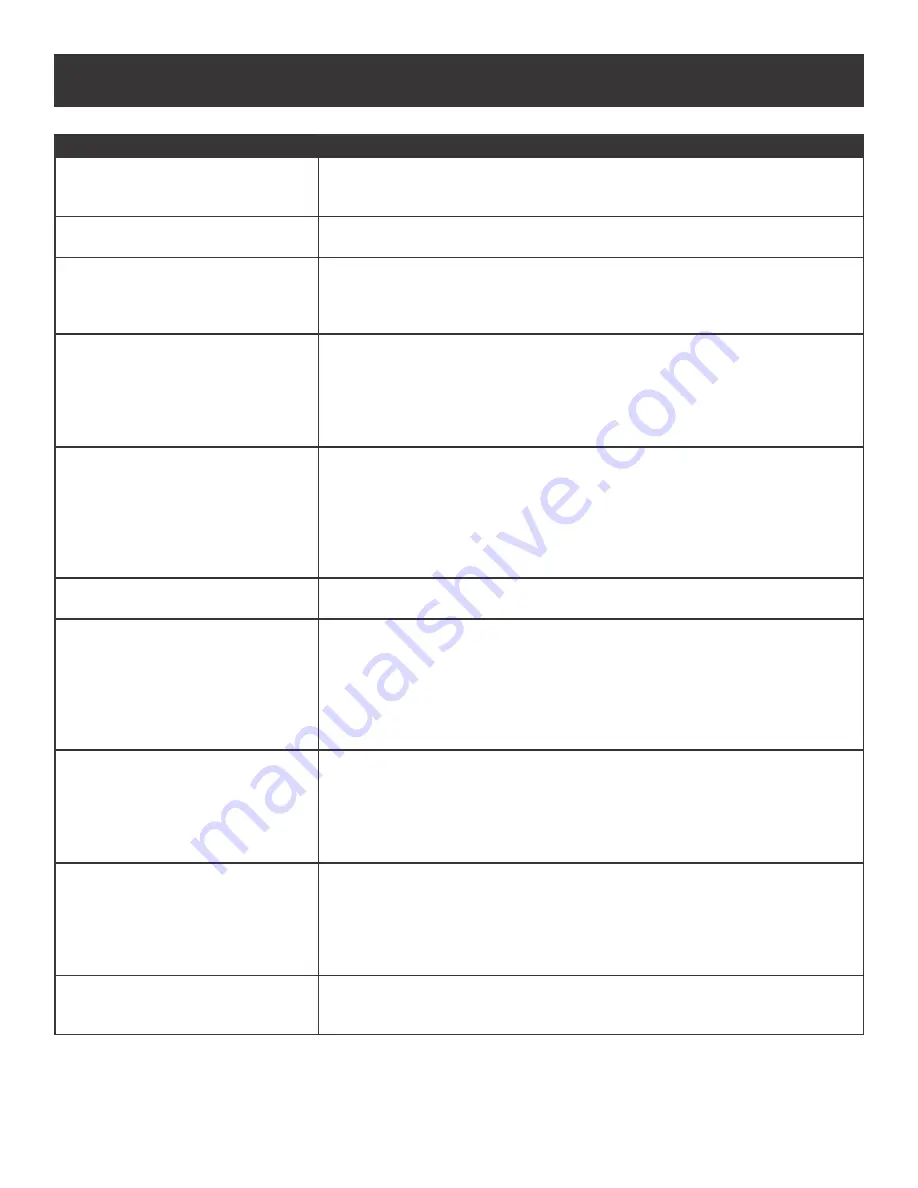
26
27
Cause
Steps
Control Settings
STEP 1:
After making sure that the machine is plugged into the wall, verify that
the on-off switch is in the ON position and that the pressure control knob is
turned all the way to the right (clockwise for maximum pressure).
Thermal Breaker
STEP 2:
Using your multi-meter, test the breaker for continuity or replace with a
new Breaker. If the Breaker reads good, move on to step three.
Power Source
STEP 3:
Using a Phillips Head screwdriver, remove the four screws holding
the pressure control assembly. Locate the red light on the board indicating that
there is power (it will be red.) If the light is OFF proceed to step four. If the light
is ON go to step six.
Power Source
STEP 4
: Locate the L1 and L2 terminals on the board, and then using your
multi-meter check to make sure you have 110 volts AC across the two terminals
(the cord wires will still be attached). If there is no voltage at these leads, there
is no power getting to the machine. Check your power source (outlet, circuit
fuse, extension cord, and power cord). If you have AC voltage at the L1 and L2
terminals, go to step 5.
Thermal Overload
STEP 5:
Disconnect the two red motor leads (S1 & S2) and test for continuity
between them. No continuity means that the thermal coupler has opened due
to excessive motor heat. If the motor is still hot to the touch, allow it to cool and
then retest. If the motor is cool and there is not continuity on the red leads,
contact Airlessco Technical Support to repair/replace the thermal coupler.
Continuity shows that the motor's thermal coupler has not tripped. Proceed to
step six.
Pressure Control Assembly (Board)
STEP 6:
If everything checks out in steps one through five and the power
indicating light is still out, replace the pressure control assembly.
Motor
STEP 7:
Remove the motor brush covers and turn the machine on. Set the
potentiometer (POT) at maximum pressure and check for DC voltage across
both brush terminals. You should read greater than 80 volts DC. I
F YOU DO
NOT HAVE DC VOLTAGE GO TO STEP EIGHT.
If you have DC voltage,
turn the machine off and unplug it from the wall. Check to make sure that the
brushes are making good contact with the armature. Replace the brushes if
they are less than 1/2" long. If the brushes are good, replace the motor.
Sensor
STEP 8:
Plug another sensor into the board and perform the zero calibration
procedure. If the machine starts to run, the sensor was bad. If there is no
replacement sensor available, use a multi-meter to test the resistance across
the red and black wires of the sensor (be sure to test at the plug). You should
read 1.5 - 3.5k ohms. A faulty sensor usually reads no continuity (open). If the
sensor passes all the tests move to step nine.
Pressure Control Knob
(Potentiometer)
STEP 9:
Plug another potentiometer (POT) into the control board. If the
machine starts, the old POT is bad. When a replacement POT is not available,
remove the POT lead (with the machine turned off) from the control board and
test the resistance between the red and black wires (be sure to test at the plug).
The resistance should read between 8-12k ohms if it is outside of this range
replace the POT.
Pressure Control Assembly (Board)
STEP 10:
If you have DC voltage at the motor brushes and all of the
components check out fine in steps eight and nine, replace the pressure control
assembly.
TROUBLESHOOTING - MACHINE DOES NOT START