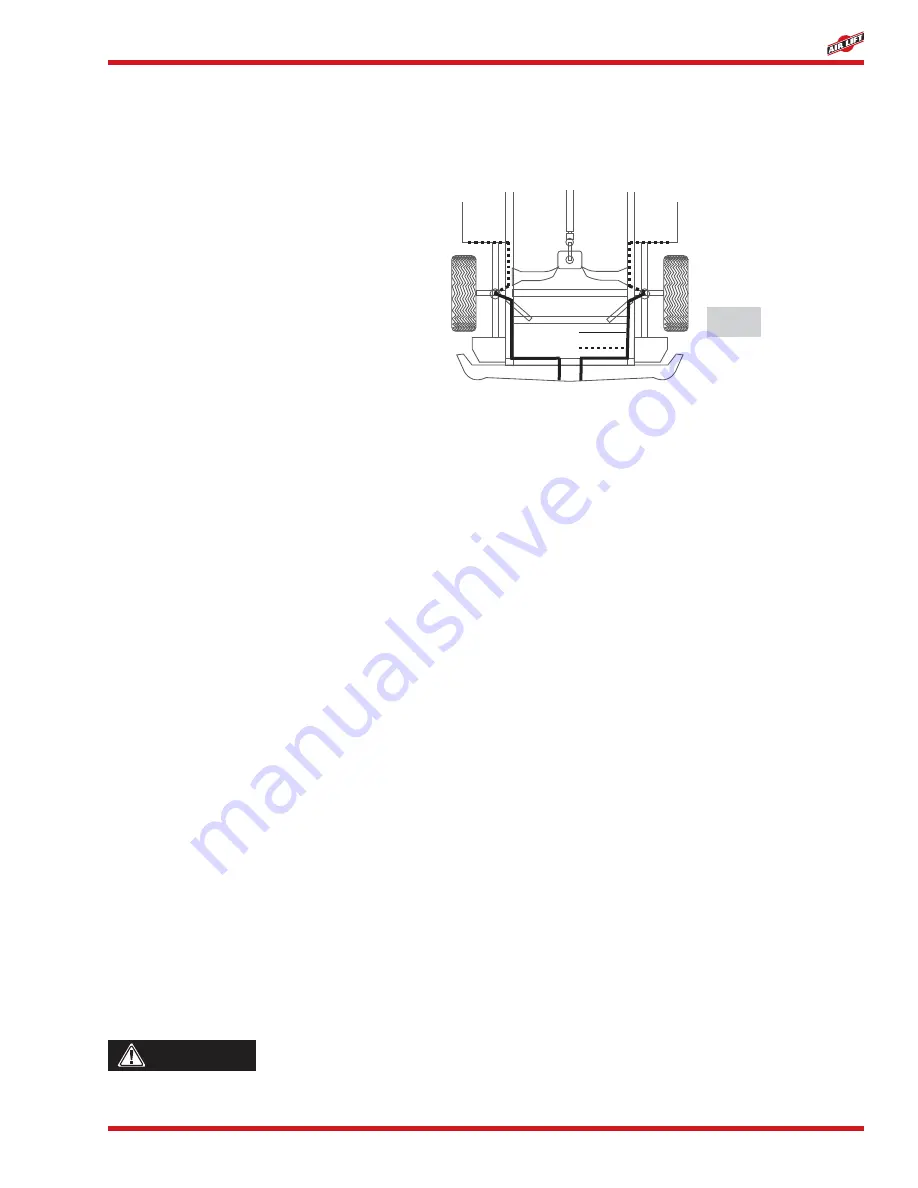
9
MN-822
LoadLifter 5000 Ultimate
CAUTION
6 . Route the air line along the frame to the air fitting on the air spring (fig . 12) . Keep AT
LEAST 6” of clearance between the air line and heat sources, such as the exhaust pipes,
muffler, or catalytic converter . Avoid sharp bends and edges . Use the plastic tie straps
to secure the air line to fixed, non-moving points along the chassis . Be sure that the tie
straps are tight, but do not pinch the air line . Leave at least 2” of slack to allow for any
movement that might pull on the air line .
7 . Cut off the air line, leaving approximately 12” of extra air line . A clean square cut will
ensure against leaks (see fig . 10) . Insert the air line into the air fitting . This is a push-
to-connect fitting . Simply push the air line into the 90° swivel fitting until it bottoms out
(9/16” of air line should be in the fitting) .
8 . Install the minimum/maximum air pressure decal in a highly visible location . We suggest
placing the decal on the driver-side window, just above the door handle .
CHECKING FOR LEAKS
1 . Inflate the air spring to 30 PSI .
2 . Spray all connections and the inflation valves with a solution of 1/5 liquid dish soap and
4/5 water . Spot leaks easily by looking for bubbles in the soapy water .
3 . After the test, deflate the springs to the minimum pressure required to restore the system
to normal ride height . Do not deflate to lower than 10 PSI .
4 . Check the air pressure again after 24 hours . A 2 - 4 PSI loss after initial installation is
normal . Retest for leaks if the loss is more than 5 lbs .
FIXING LEAKS
1 . If there is a problem with the swivel fitting:
a. Check the air line connection by deflating the spring and removing the line by pulling
the collar against the fitting and pulling firmly on the air line. Trim 1” off the end of
the air line. Be sure the cut is clean and square (see fig. 10). Reinsert the air line
into the push-to-connect fitting.
b. Check the threaded connection by tightening the swivel fitting another ½ turn. If it still
leaks, deflate the air spring, remove the fitting, and re-coat the threads with thread
sealant . Reinstall by hand tightening as much as possible and then use a wrench
for an additional two turns .
2 . If there is a problem with the inflation valve:
a . Check the valve core by tightening it with a valve core tool .
b. Check the air line by removing the air line from the barbed type fitting. Cut the air line
off a few inches in front of the fitting and use a pair of pliers or vice grips to pull/twist
the air line off of the fitting.
DO NOT CUT OFF THE AIR LINE COMPLETELY AS THIS WILL USUALLY NICK THE
BARB AND RENDER THE FITTING USELESS .
3 . If the preceding steps have not resolved the problem, call Air Lift customer service at
(800) 248-0892 .
fig. 12
Option 1
Option 2