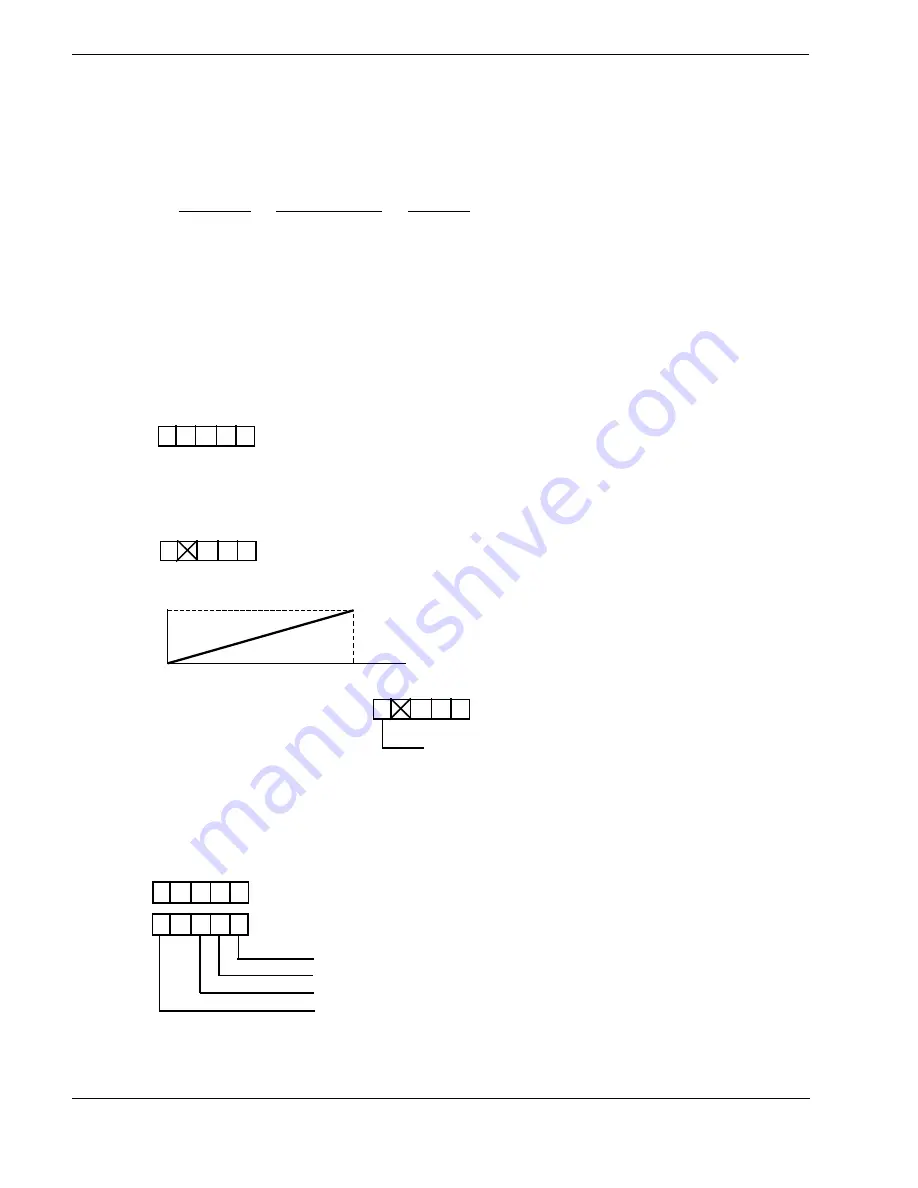
The shaft driving the incoming roller is turning at 1000 rpm, and the shaft driving the outgoing roller
is turning at 1250 rpm.
You want the tachometer to:
1. Compute Speed A (Incoming roller) and Speed B (out-going roller) in FPM.
SF fpm = 60 x
π
x D’ = 60 x 3.1416 x 3’ = 565.4880
PPR 48 48
C
1
= 565.5
C
2
= 48.00
C
3
= 565.5
C
4
= 48.00
2. Send the percentage of elongation to Display, ratio to Setpoints I and 2, and Speed B only to
Analog Output.
C
11
= x 5 5 2 9
3. Have Display show FPM with autoranging fixed to one decimal place.
C
5
=1000
C
12
= 1
4. Have the Analog Output drive an auxiliary 4 - 20mA recorded which has a range of 0 to 5000fpm.
20mA
4mA
0 fpm 5000
C
6
= 0000
C
12
= 1
C
7
= 5000
blank
5. Use the setpoints for web break detection, with Setpoint 1 going to alarm if the ratio is less than
0.5, and Setpoint 2 going to alarm if the ratio is less than 1.0. Relays are latching.
C
8
= 0.500
C
9
= 1.000
C
10
= x 0 0 0 0 (no hysteresis)
C
12
= x 5 5 1
autoranging fixed to one decimal place
latching relay
latching relay
analog output is 4 - 20mA
12
Summary of Contents for TACHTROL 3
Page 1: ...TACHTROL 3 ...
Page 23: ...2 NEMA 4X 3 X STYLE 4 LESS ENCLOSURE STYLE 19 ...