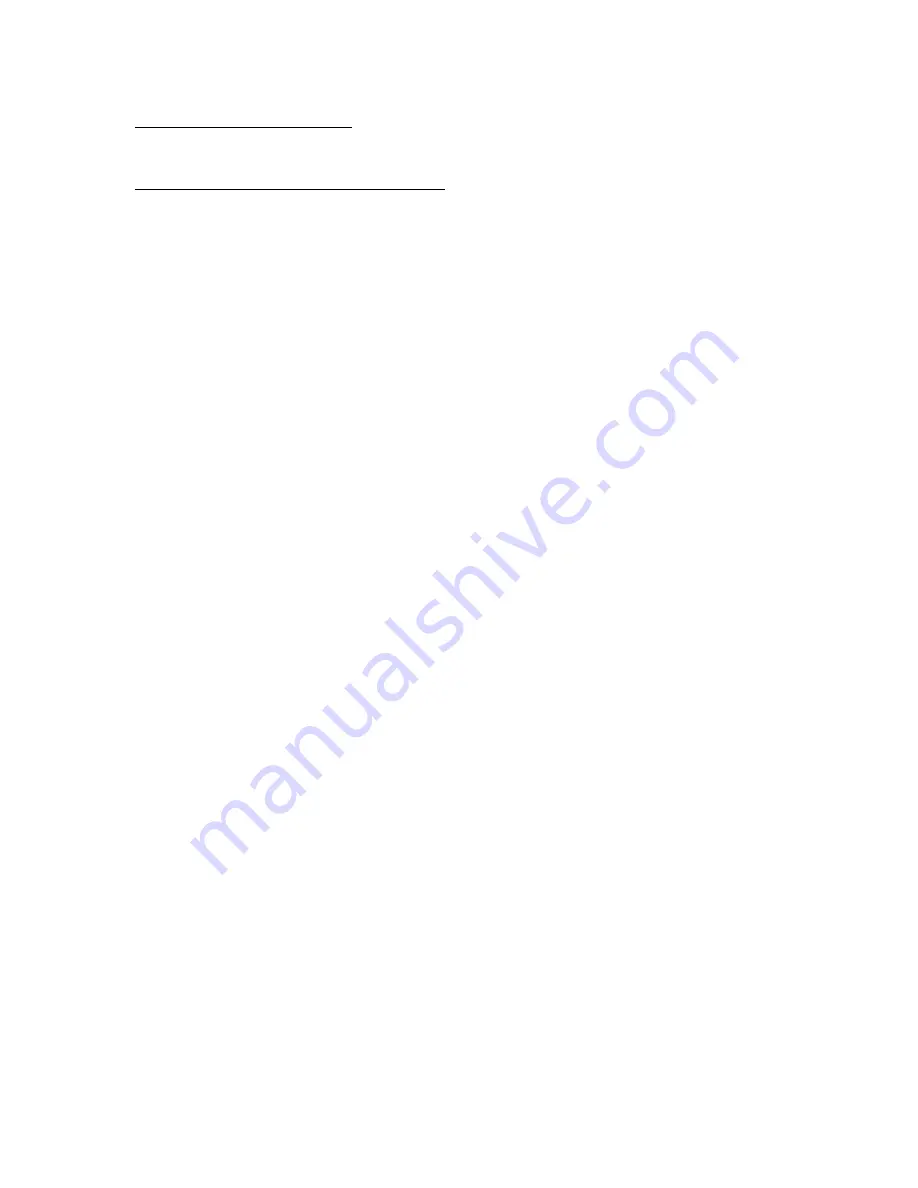
16
MODEL 250C WELD GUN
DISASSEMBLY OF THE WELD GUN
(Refer to Illustration No. 1 page 17)
A.
Remove handle cover screws (items 28, 29, & 45).
B.
Lift off the handle cover (item 38).
C.
Remove the nut, washer, and cap screw (items 34, 35, & 36) from the welding
lead (item 40).
D.
Remove the control wires (item 32, & 33) from the trigger switch (item 37), and
remove the switch from the handle.
E.
Lift out the welding and control lead assemblies (item 40, & 30), from the handle.
F.
Loosen the cap screw of the cable clamp assembly (item 39), and slide both wires
out of the clamp.
G.
Unscrew the end cap (item 1) from the gun housing.
H.
Unscrew the stop nut (item 15) from the end of the shaft.
I.
Unscrew the knurled spring retainer (item 17) from the gun housing.
J.
Remove the washer (item 3)
K.
Remove the spring (item 4) from the gun shaft.
L.
Unscrew the three (3) screws (item 9 & 22) from the housing.
M.
Remove the collet adaptor assembly and dust boot (items 25 & 12) from the shaft
assembly (item 6).
N.
Check to be sure there are no burrs on the end of the gun shaft. If necessary use a
file or emery paper to smooth it off. Slide the faceplate (item 10) off shaft
assembly.
O.
Slide the shaft assembly (item 6) out of the gun housing, making sure the pigtail
assembly (item 7) feeds through the slot in the housing and handle.
To assemble the gun, repeat these operations in the reverse order.
Summary of Contents for JS-1
Page 17: ...17 ILLUSTRATION NO 1 Not Shown 2615 M ADAPTER ASSEMBLY INCLUDES ITEMS 25 13 14 24...
Page 32: ...32 WIRING DIAGRAM JS 1...
Page 34: ...34 Illustration No 2...
Page 35: ...35 Illustration No 3...
Page 36: ...36 Illustration No 4...