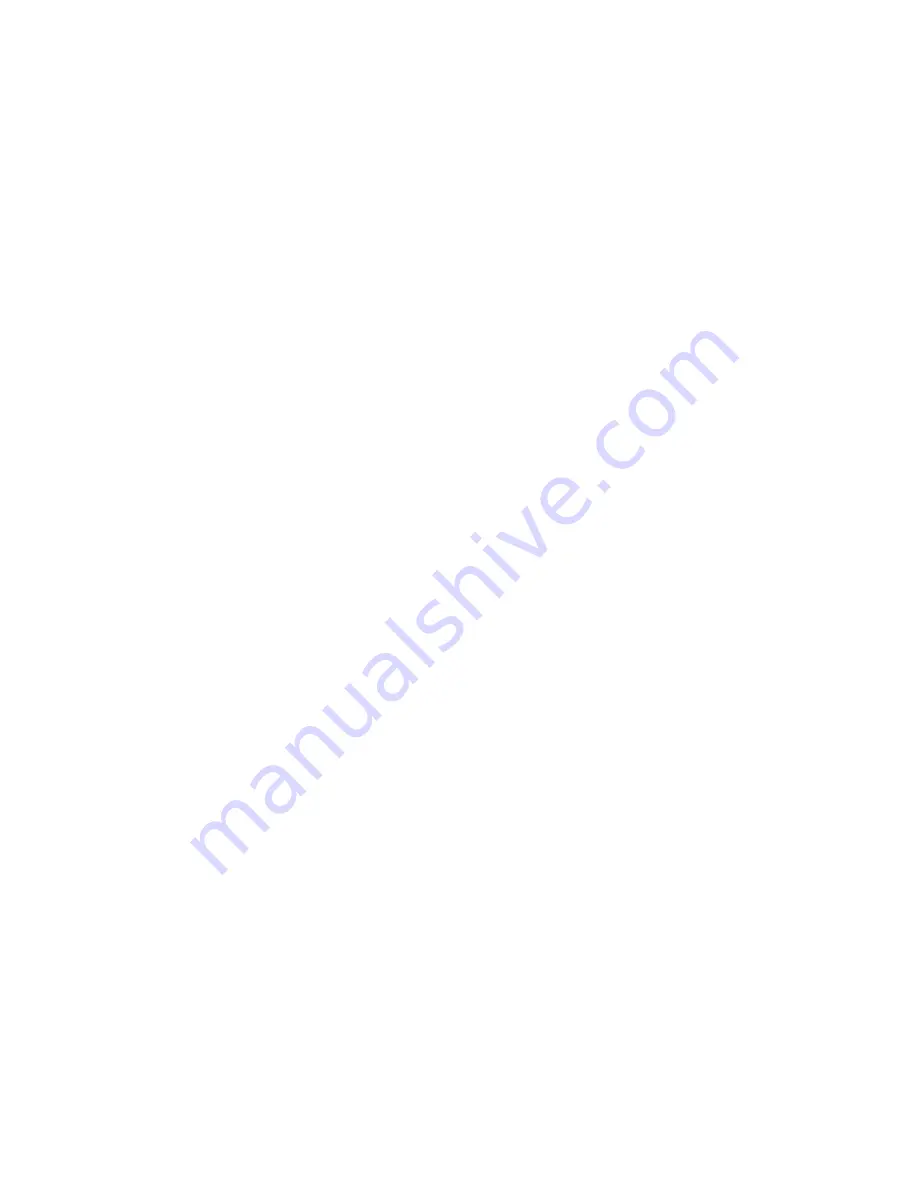
4 - Principles of Operation
52
The SCR, connected across the output, will fire and short the output when an overvoltage condition is
detected. The SCR is controlled by the OV_SCR* signal from the crowbar control circuit (described in the
next section).
Two current shunt resistors (RmHi and RmLo) monitor the output current. RmHi monitors the high current
range; RmLo monitors the low current range. Shunt clamps are connected in parallel across RmLo to limit
the current to approximately 25 mA (the maximum rating of the low current range).
The output filter capacitor provides additional filtering of the dc output.
Control Circuits
As shown in Figure 4-2, the control circuits consist of the CV/CC control, output voltage/current monitor,
bias supplies, and SCR control.
The CV/CC control circuits provide a CV control loop and a CC control loop. For any value of load
resistance, the supply must act either as a constant voltage (CV) or as a constant current (CC) supply.
Transfer between these modes is accomplished automatically by the CV/CC control circuit at a value of
load resistance equal to the ratio of the programmed voltage value to the programmed current value. A low
level CV_Detect* or CC_Detect* signal is returned to the secondary interface to indicate that the
corresponding mode is in effect.
With the CV loop in control, the output voltage is regulated by comparing the programmed voltage signal
CV_Prog (0 to -5V) with the output voltage monitor signal VMon. The VMon signal is in the 0 to +5 V
range, which corresponds to the zero to full-scale output voltage range of the supply. If the output voltage
exceeds the programmed voltage, the Control signal goes low, causing the output regulator to conduct less
and decrease the output voltage. Conversely, if the output voltage is less than the programmed voltage, the
Control signal goes high, causing the regulator to conduct more and increase the output voltage. Depending
upon the position of the Sense switch, the output voltage is either monitored at the supply's output terminals
(local), or at the load (remote), using the +S and -S terminals with remote sense leads connected to the load.
If the output voltage goes higher than the programmed value, the downprogramming stage is turned on.
With the CC loop in control, the output current is regulated by comparing the programmed current signal
CC_Prog (0 to -5V), with the output current monitor signal Imon_H. The Imon_H signal is produced by
measuring the voltage drop across current monitoring resistor and is in the 0 to +3.5 V range, which
corresponds to the zero to full-scale output current range. If the output current exceeds the programmed
value, the Control signal goes low, causing the output regulator to conduct less and thus decrease the output
current. Conversely, if the output current is less than the programmed value, the Control signal goes high,
causing the output transistors to conduct more and increase the output current. A gross current limit circuit
protects the output if the output current exceeds the maximum current rating of the unit.
When the downprogramming stage is turned on (in either CV or CC mode), the CV/CC control circuit
causes the Control signal to go low, which in turn causes the downprogramming transistors to conduct
current away from the load and speed up downprogramming.
During operation, a PM_Inhibit signal will cause the output stage bias/shutdown circuit to turn off the gated
15 V bias voltages and shut down the output if any of the following occur:
The output is programmed off.
An overvoltage condition is detected (OV_Detect* signal is received).
The line voltage falls below 90 volts (approximately).
Summary of Contents for 6612B
Page 8: ......
Page 25: ...Troubleshooting 3 25 Figure 3 1 Sheet 3 Main Flowchart...
Page 46: ......
Page 49: ...Principles of Operation 4 49 Figure 4 1 A2 A3 Block Diagram...
Page 51: ...Principles of Operation 4 51 Figure 4 2 A1 Block Diagram...
Page 54: ......
Page 57: ...Replaceable Parts 5 57 Figure 5 1 Mechanical Parts ldentification...
Page 67: ...Figure 6 1 A1 Board Component Locations...
Page 68: ...Figure 6 2 A4 Board Component Locations...
Page 69: ...Figure 6 3 A1 Board schematic sheet 1...
Page 70: ...Figure 6 3 A1 Board schematic sheet 2...
Page 71: ...Figure 6 3 A1 Board schematic sheet 3...
Page 72: ......