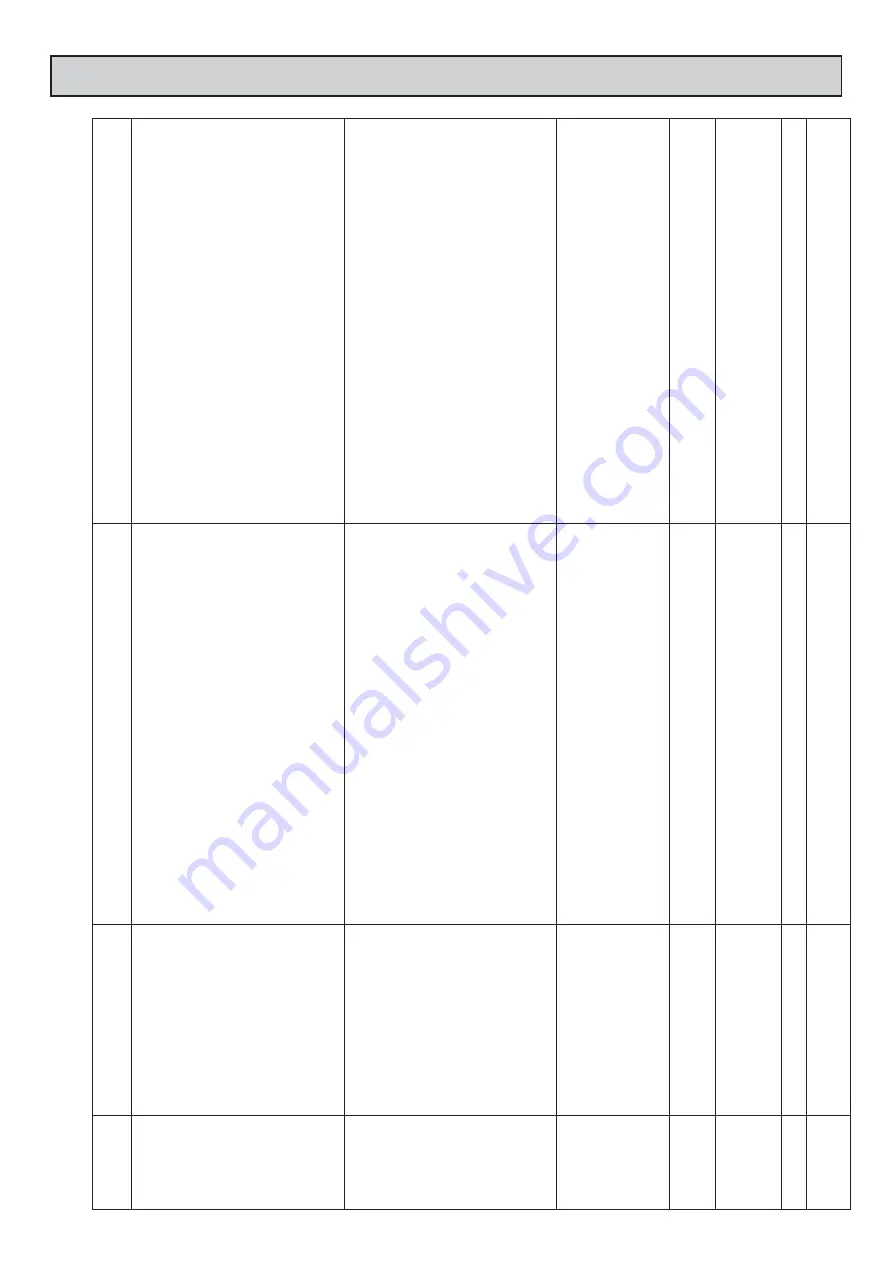
17
Fault Diagnostics
Code
Error
No ignition on cooker
burner af
ter 3 attempt
s
A1
Possible Cause
a.
Ignition wire/plug has become det
ached or is broken.
b.
No current is being received from ionisation probe.
c.
Gas valve is not allowing any gas to the burner/throttle is
not correctly set.
d.
Air proving rubber tube (from valve to air inlet tubing has
become det
ached or is ripped).
e.
Burner fan is not operating correctly
.
f.
Blocked flue and/or air inlet.
Correction
a.
Check both wiring and plug for fault
s.
b.
Remove link wire from ionisation block and check for
μ
A
reading during ignition.
c.
Check electrical connector is fitted to the valve and the
solenoid open during ignition.
d.
Check rubber tube is connected properly and there are no
tears.
e.
Ensure connections to fan are made and it is running
during ignition attempt
s.
f.
Inspect flue/air inlet for any blockages throughout the
system.
A2
No ignition on boiler burner
af
ter 3 attempt
s
a.
Ignition wire/plug has become det
ached or is broken.
b.
No current is being received from ionisation probe.
c.
Blocked condensate trap/pipe earthing ionisation probe.
d.
Gas valve is not allowing any gas to the burner/throttle is
not correctly set.
e.
Air proving rubber tube (from valve to fan has become
det
ached or is ripped).
f.
Blocked flue and/or air inlet.
a.
Check both wire and plug for fault
s.
b.
Remove link wire from ionisation block and check for
μ
A
reading during ignition.
c.
Unscrew condensate trap base, only a small amount of
water should escape otherwise a blockage is likely
.
d.
Check electrical connector is fitted to the valve and the
solenoid opens during ignition.
e.
Check rubber tube is connected properly and there are no
tears.
f.
Inspect flue/air inlet for any blockages throughout the
system.
A3
Boiler Overheat Error/
Pressure Sensor Error
a.
Heating system below required pressure (1 bar) or above
required pressure (3 bar).
b.
Pressure st
at not wired correctly/faulty st
at.
c.
Overheat thermocouple triggered on heat exchanger
body
. (Usually caused by air lock af
ter refilling or by faulty
pump).
a.
Heating system not pressurised correctly/open system
being used.
b.
Check wiring/wire out st
at to determine whether faulty
.
c.
Ensure pump is running and all air is removed from
system/wire out st
at to determine whether faulty
.
A4
Overheat on cooker
a.
Oven temperature found to be >270°C
a.
Check cooker flue for blockage/replace cooker
thermistors.
A5
Dif
ferential between the 2
cooker thermistors >20°C
for longer than 10 minutes
a.
Sensors not fitted correctly/faulty
.
a.
Ensure thermistors are fitted correctly/replace sensors.
A6
Boiler fan error
a.
Wiring connector not fitted correctly/faulty fan.
a.
Check connections/replace fan.
A8
Appliance control board
settings incorrect
a.
Incorrectly inst
alled sof
tware in manufacture
a.
Reprogram control board with correct sof
tware/replace
PCB.
Cooker fault code is shown on R.H. side of screen
Boiler fault code is shown on L.H. side of screen
Summary of Contents for RAYBURN Heatranger 480CD
Page 10: ...Replacement of Parts Electrical Controls 10 FIG 12 DESN 514884...
Page 12: ...Replacement of Parts Boiler Burner 12 FIG 15 DESN 514889...
Page 19: ...19...
Page 20: ...20...
Page 21: ...21...
Page 22: ...22...
Page 23: ...23...