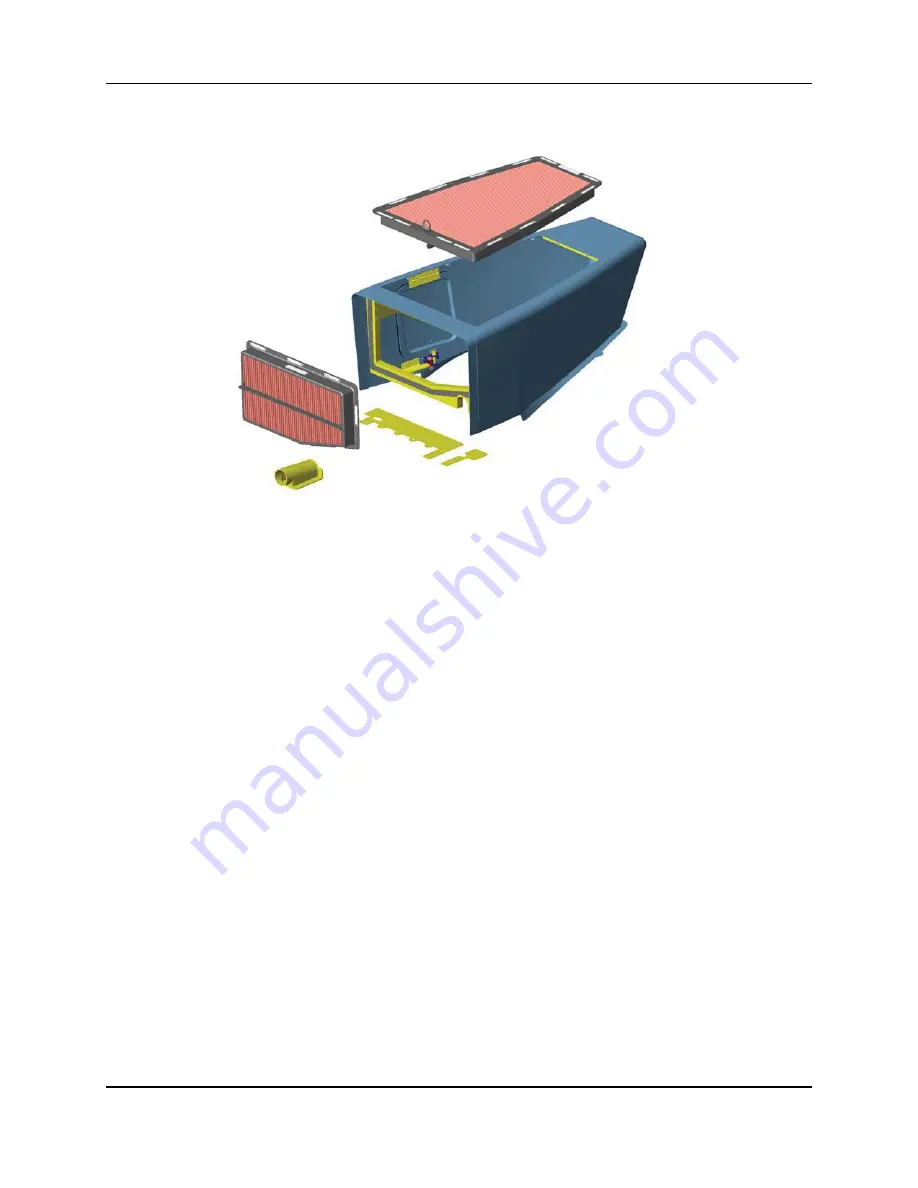
Aerospace Filtration Systems, Inc.
MD500-IBF-KIT-OMM/IPL
Proprietary
Information
Use or disclosure of this material is subject
MD500 IBF Operation & Maintenance Manual/
to the restrictions on the title page
Illustrated Parts List - Revision B
2
Figure 1: AFS MD500 Inlet Barrier Filter System
1.2 P
RE
-F
LIGHT
I
NSPECTION
Pre-flight inspection shall be made by the pilot to inspect the filters (forward and upper) for
damage, excessive accumulation of debris (straw, leaves, insects, etc.) or snow/ice, missing or
damaged fasteners, or the need for servicing or repair of the filters. After extended operation in
precipitation (i.e., rain, or a combination of rain and sleet/snow), the sand and dust collected on
the external side of the filter media (dirty side) may coagulate in the corners of the filter media
pleats. If visual inspection indicates existence of any of the above conditions, the decision
whether to service the filter assemblies will reside with the flight crew. Damaged or missing
fasteners should be replaced to maintain maximum seal integrity. The filter assemblies use
captive fasteners and should not need replacement during normal service. If the fastener should
become damaged, perform fastener replacement per manufacturer’s recommendations (see
paragraph 4.3). Operation with either missing fasteners and/or filter damage can severely
degrade IBF system separation efficiency and result in possible performance loss, wear, and/or
damage to the engine. Damaged filter elements should be either repaired as described in
paragraph 4.0 below or replaced.
Summary of Contents for MD500 Series
Page 2: ......