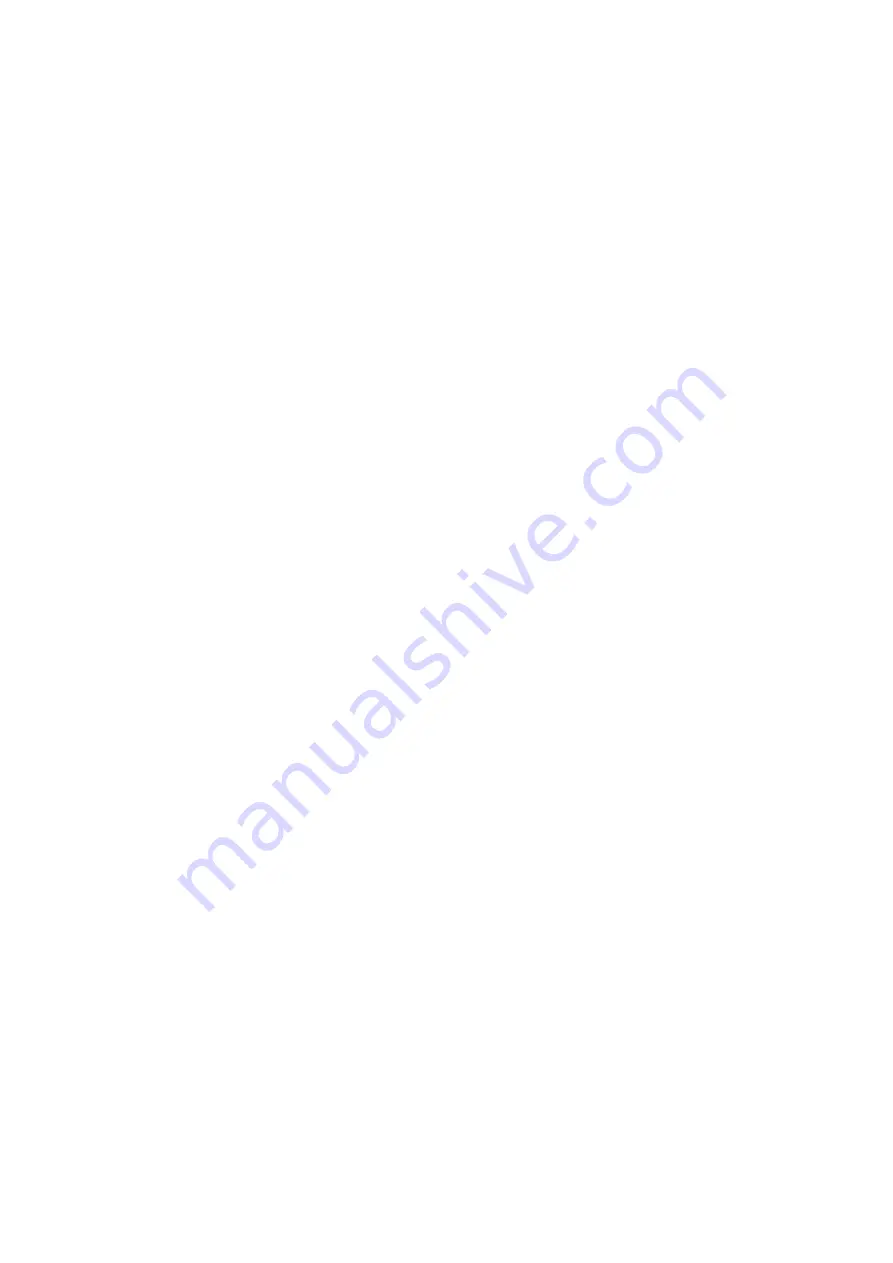
11
- The cover BE should be reliably tightened
- Power and communication cables external diameter shall be from 5 to
8.8 mm
- The cable glands should be reliably tightened.
3.4.6. The power and communication cables are fixed on the wall wherever
possible. To avoid mechanical damages, it is recommended to place
them in a metal tube or sleeve. The signal (communication) and power
cables may be placed in one tube (sleeve).
DO NOT fix cables to the heated pipeline.
3.4.7. To provide electrical connection, it is necessary to connect the pipeline
sections cut in the wafer type MFT mounting location by wires (jumpers)
via a terminal located on the BE; wires should be of 4 mm
2
cross
section as a minimum (see Appendix A). If the pipeline has cathode
protection, cross section of the jumpers shall correspond to the value of
cathode protection current. Use the M5 threaded holes on cylindrical
surface of the flanges to connect the jumpers.
When mounting flanged type flowmeters, it is necessary to connect
the PFC flanges and the mating pipeline flanges by wires with cross
section of no less than 4 mm to ensure appropriate electrical connection
(see Appendix B).
When mounting flowmeters with the threaded coupling, connection
of the wires is not required as the electrical connection of the cut
pipeline parts is ensured by the
flowmeter’s components.
3.4.8. The need for protective grounding is determined by power supply and
environment conditions under which the flow meter is operated.
To prevent failures of the flow meter, the grounding terminal must
not be connected to the lightning protection system.
As a grounding wire, you must use a mechanically protected
copper wire of 2.5 mm
2
cross-section as a minimum or a copper wire
without mechanical protection of 4 mm
2
cross section as a minimum.
The grounding conductor is connected to the fixing screw on the
electronic block.
CAUTION! If the pipeline is equipped with cathode protection,
do not ground the flowmeter.
3.4.9. After completing the wiring of the flow meter, install in place the back
cover of the electronics block, and for the flow meter in the remote
version
– the cover of the switching block.
4. DISMOUNTING
4.1. The order of dismounting the flowmeter before dispatching for regular
calibration or repair is as follows:
- Turn off power, then disconnect network and signal cables from the
flowmeter
- Disconnect wires (connecting jumpers, if any) from the pipeline flanges
- Cut off liquid at the PFC location, make sure that pressure is released
and drain the liquid
- Remove PFC