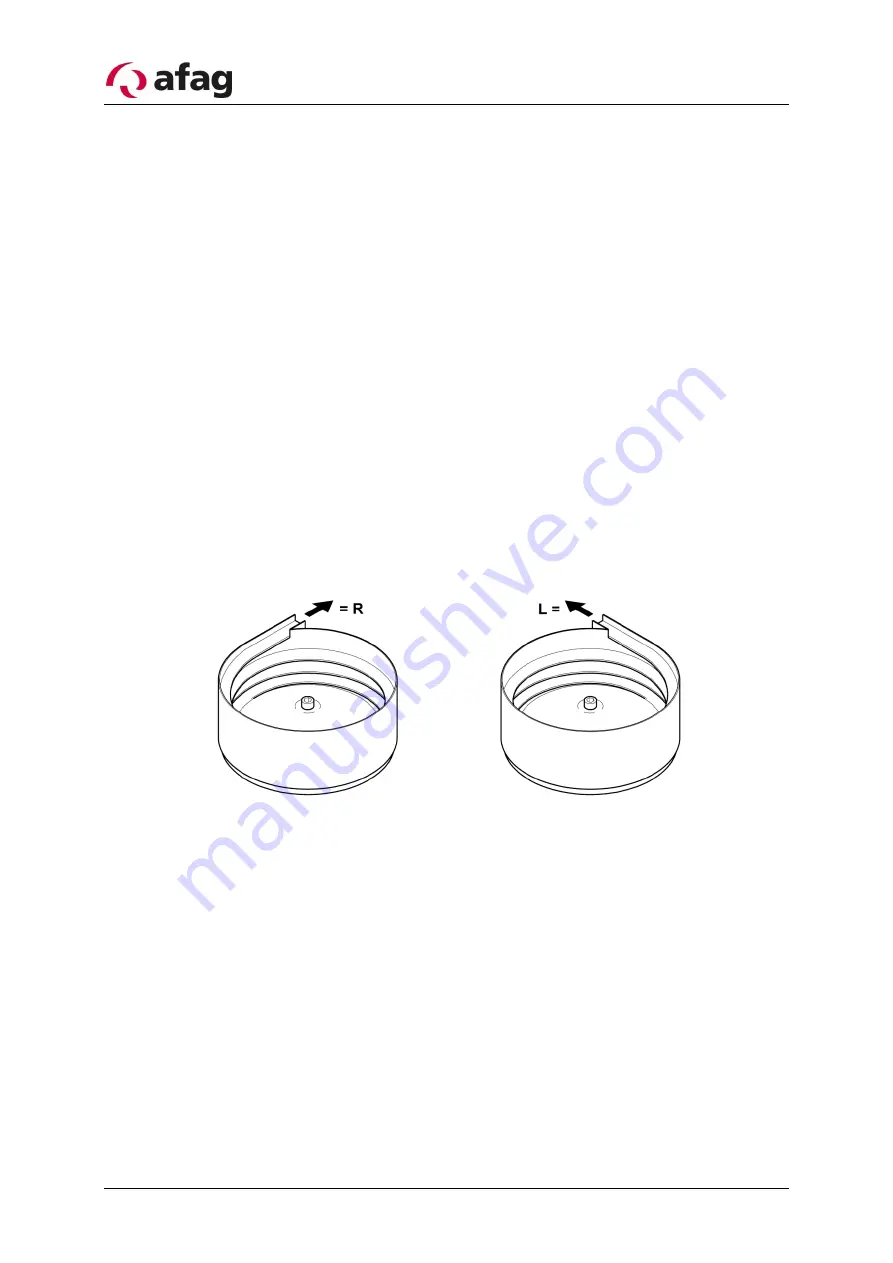
Page 8
16/05/2019
R01.0
The magnet, connected to the support, creates a force which attracts reps. releases the
oscillating plate dependent on the oscillation frequency of the power supply.
The pulsating movement of the oscillation plate causes the material to jump from the rail
at each oscillation and is conveyed as a result of the angle of inclination of the leaf springs.
On a cycle of the 50 Hz alternating current supply, the magnet achieves twice its maximum
pulling force while this is independent of the direction of the current flow. The magnet
thereby produces an oscillating frequency of 100Hz. This 100Hz oscillation is necessary
to achieve a smooth and gentle transport for small or light work pieces.
With heavy or large work pieces however, it is necessary to use an oscillating frequency
of 50Hz. A half-wave of the mains supply is thereby blocked.
2.3
Definition of the feed direction
The feed directions for the WV are defined as follows:
Left-hand (L)
, in
anti-clockwise
direction
Right-hand (R)
, in
clockwise
direction
Figure
2
Summary of Contents for WV 630-1
Page 18: ...Page 18 16 05 2019 R01 0 ...