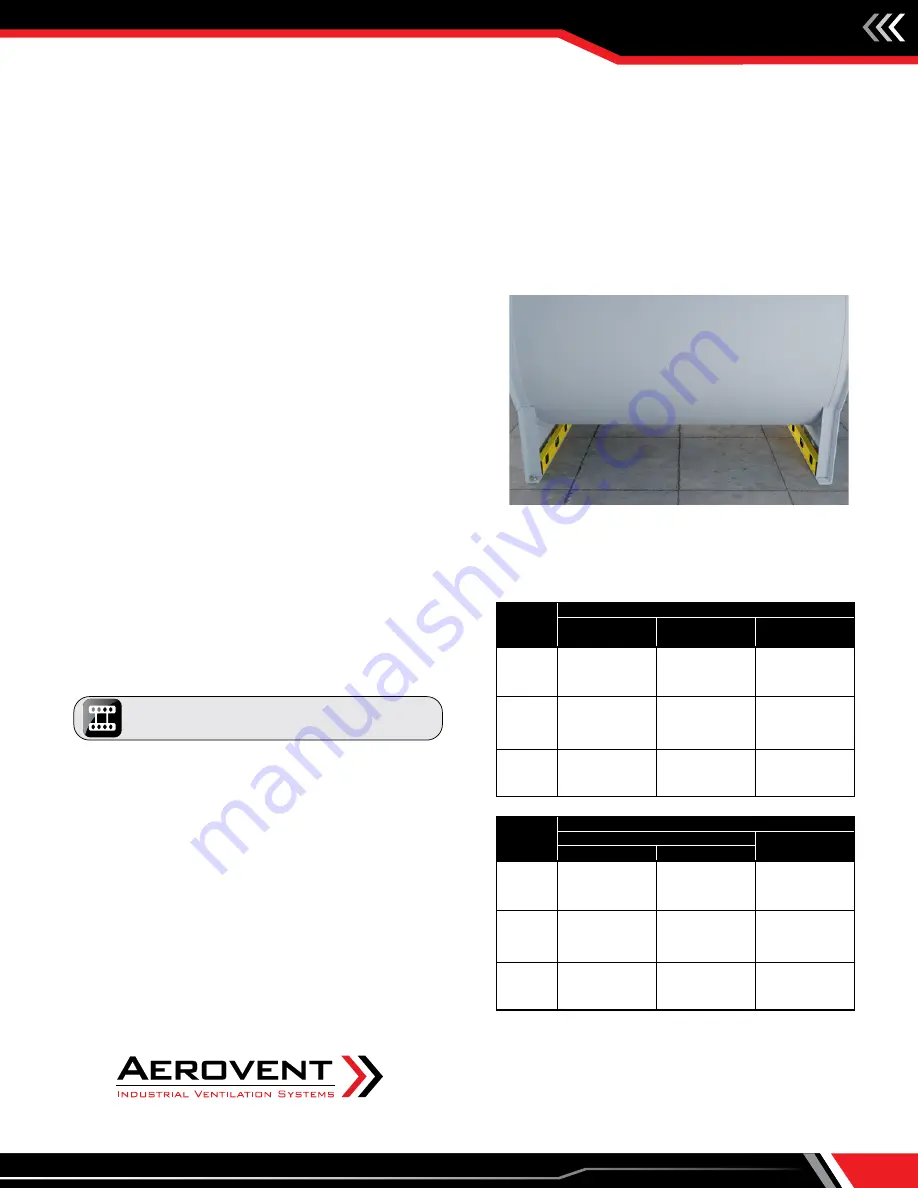
Installation, Operation & Maintenance Manual
IM-166
9
Fan Installation – Factory Assembled Units
(refer to lifting/safety section)
All fan impellers are statically and dynamically balanced using state of the art equipment in the factory. Final trim balancing is
performed on factory assembled fans, unless the specified electrical characteristics of the motor are outside the limits of the factory
test equipment. If the motor and drives are supplied, the complete assembly is run tested and balanced. Infrequently, fans are
supplied with unusual electrical characteristics and cannot be tested with the motor. In this situation the fans are run and balanced
using a factory driver. Likewise, if motors and/or drives are not supplied, the fan is tested with the factory driver. Final balancing, at
the buyer’s expense, should be performed in the field after the motor and/or drives are installed. This service is available from TCF,
otherwise this should be entrusted to a qualified technician.
Follow proper handling instructions as given earlier.
1. Move the fan to the final mounting position.
2. Remove skid, crates and packing materials carefully.
3. Attach vibration isolators (if used) to appropriate mounting
locations on fan. Locate fan in position using lifting
instructions on page 5.
4. Place the fan on mounting structure. Carefully level the unit
on the foundation and shim as necessary using stainless
steel shims on both sides of each anchor bolt. Back off
leveling nuts if used. Be careful not to force the fan to the
mounting structure/foundation. This may cause the bearings
to become misaligned or pinched causing vibration and
premature failure.
5. Check the alignment of the bearings. Shim or reposition the
bearings if necessary.
6. Check alignment of sheaves on belt driven fans.
7. Check tension of belts to see if it is sufficient. Sheaves on
belt driven fans are often provided with taper lock bushings.
When tightening bushing bolts, proceed in a progressive
manner to avoid cocking the tapered surfaces between the
bushing and the sheave. Torque per tables on the right.
8. Check the tightness of the impeller on the shaft. Check the
tightness of foundation bolts, motor bolts, sheaves and
bearings. Make sure there is no rubbing or binding and that
the impeller-inlet cone clearances and overlap are correct.
9. Check that bearings are fully lubricated. For spherical roller
bearings with split pillow block housings, the bottom half
of the housings should be 1/3 full of grease. For oil lube
bearings, the oil level should reach the midpoint of the
bottom roller or ball.
10. Install any accessories shipped loose from the factory.
The above torque values are for nonlubricated fasteners and Browning
Bushings. For bearing set screws, use manufacturer’s recommendations.
If other bushings are used, utilize bushing manufacturer's specifications.
Tolerance: +/-
5%
For impeller set screws use Grade 2 values.
SIZE
FASTENER - TIGHTENING TORQUE (Ft. Lbs.)
GRADE 2
GRADE 5
GRADE 8
#10
—
—
—
1
⁄
4
-20
5.5
8
12
5
⁄
16
-18
11
17
25
3
⁄
8
-16
22
30
45
7
⁄
16
-14
30
50
70
1
⁄
2
-13
55
75
110
9
⁄
16
-12
—
—
—
5
⁄
8
-11
100
150
220
3
⁄
4
-10
170
270
380
7
⁄
8
-9
165
430
600
1-8
250
645
900
1
1
⁄
4
-7
500
1120
1500
SIZE
TAPER BUSHINGS - TIGHTENING TORQUE (Ft. Lbs.)
SPLIT
QD
FOR DRIVE
IN IRON
IN ALUM. HUB
#10
—
—
5
1
⁄
4
-20
7.9
7.5
9
5
⁄
16
-18
16
13
15
3
⁄
8
-16
29
24
30
7
⁄
16
-14
—
—
—
1
⁄
2
-13
70
—
60
9
⁄
16
-12
—
—
75
5
⁄
8
-11
—
—
135
3
⁄
4
-10
—
—
—
7
⁄
8
-9
—
—
—
1-8
—
—
—
1
1
⁄
4
-7
—
—
—
Tightening Torque
Carefully level the fan on the foundation