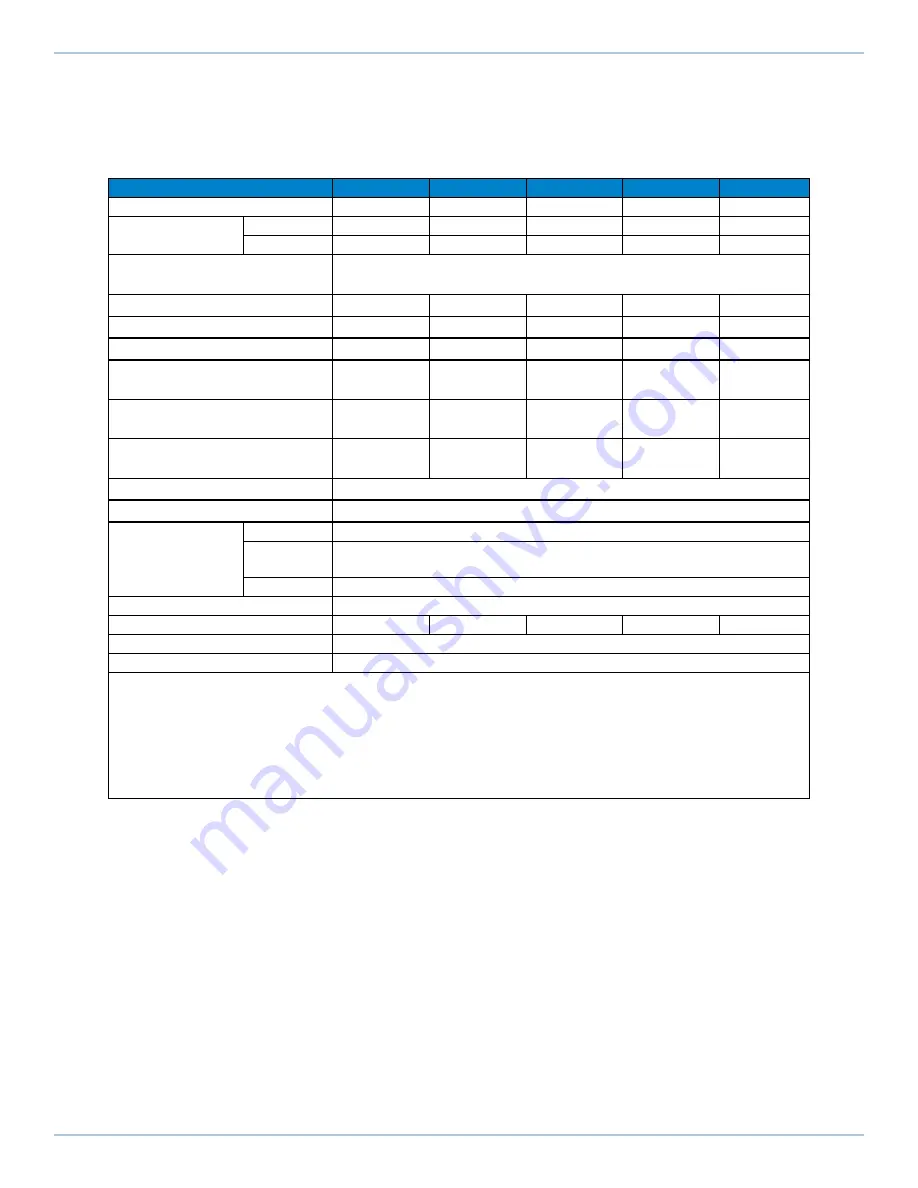
1.3. Basic Specifications
Resolution is dependent on screw pitch, encoder resolution, and controller interpolation.
Table 1-3:
ECO165SL Series Specifications (-050 to -250)
-050
-100
-150
-200
-250
Travel
50 mm
100 mm
150 mm
200 mm
250 mm
Accuracy
(1)
Standard
±6 µm
±6 µm
±8 µm
±8 µm
±9 µm
Calibrated
±1 µm
±1.25 µm
±1.5 µm
±1.75 µm
±2 µm
Resolution
(Minimum Incremental Motion)
0.2 µm
(2)
, 0.75 µm
(3)
Bidirectional Repeatability
(1)
±4 μm
±4 μm
±4 μm
±4.5 μm
±4.5 μm
Straightness
(1)
±2 μm
±3 μm
±4 μm
±5 μm
±6 μm
Flatness
(1)
±2 μm
±3 μm
±4 μm
±5 μm
±6 μm
Pitch
35 μrad
(7.2 arc sec)
40 μrad
(8.3 arc sec)
40 μrad
(8.3 arc sec)
50 μrad
(10.3 arc sec
60 μrad
(12.4 arc sec)
Roll
35 μrad
(7.2 arc sec)
40 μrad
(8.3 arc sec)
40 μrad
(8.3 arc sec)
50 μrad
(10.3 arc sec)
60 μrad
(12.4 arc sec)
Yaw
35 μrad
(7.2 arc sec)
40 μrad
(8.3 arc sec)
40 μrad
(8.3 arc sec)
50 μrad
(10.3 arc sec)
60 μrad
(12.4 arc sec)
Maximum Speed
(4)
300 m/s
Maximum Acceleration
(4)
Function of motor, amplifier, payload, and maximum axial load
Load Capacity
(5)
Horizontal
45 kg
Vertical
(Axial)
25 kg
Side
45 kg
Moving Mass with tabletop
2.8 kg
Stage Mass with no motor
5.4 kg
5.8 kg
6.3 kg
6.8 kg
7.3 kg
Material
Anodized Aluminum
Mean Time Before Failure
20,000 Hours
1. Certified with -PL1 and -PL2 option.
2. Achieved with Aerotech rotary motor with amplified sine encoder.
3. Achieved with Aerotech rotary motor with 2500 counts/rev digital encoder.
4. Requires the selection of an applicable amplifier with sufficient voltage and current.
5. Axis orientation for on-axis loading is listed.
6. Specifications are for single-axis systems measured 25 mm above the tabletop; performance of multi-axis system
depend upon the payload and workpoint. Consult the Aerotech factory for multi-axis or non-standard applications.
7. Specifications listed are non-foldback kit options. Contact the factory for specifications when a foldback kit (-FBx) is used.
1.3. Basic Specifications
ECO165SL Hardware Manual
18
www.aerotech.com