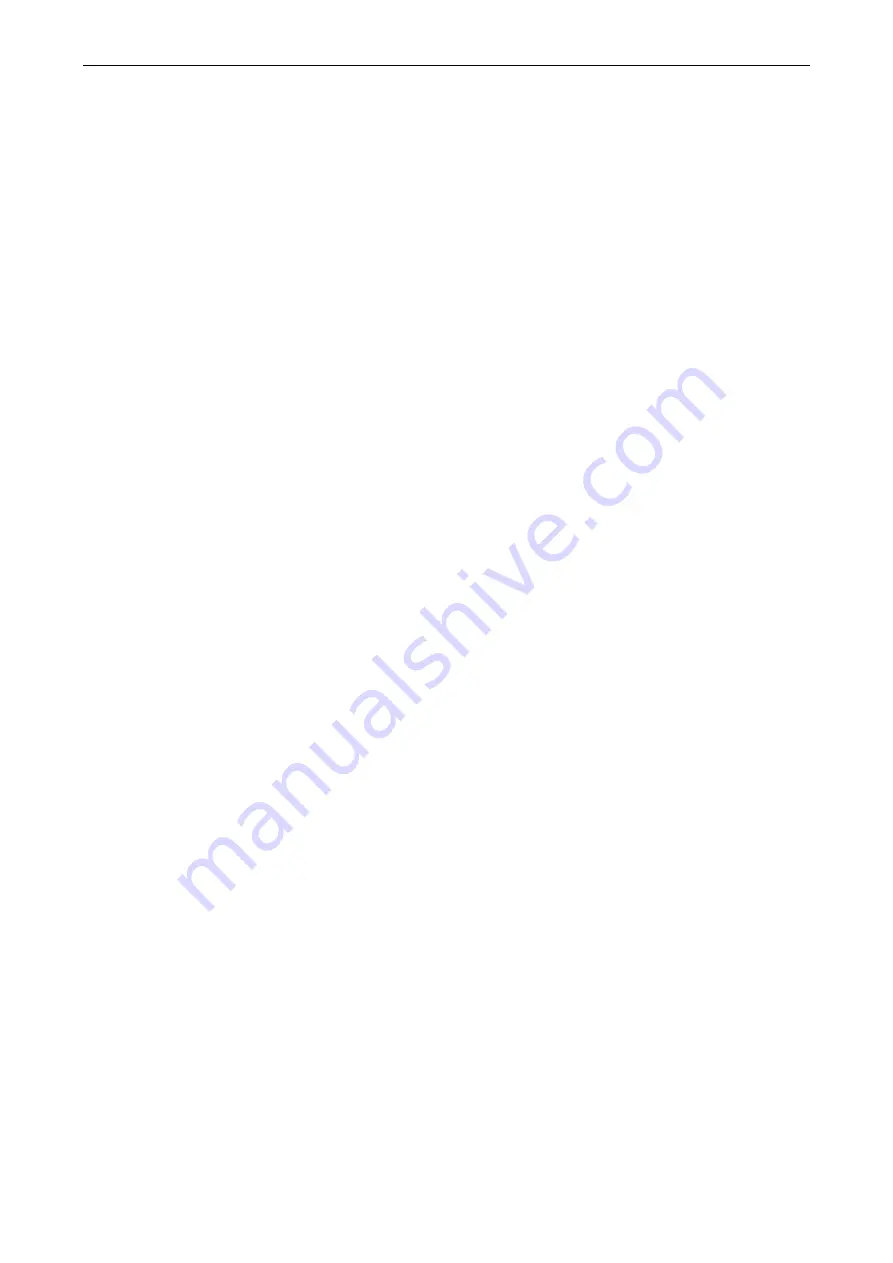
AEROPRAKT-32 Pilot Operating Handbook
A32-060-POH
11
3.2.3.2 in level flight
1. Airspeed
– 110 km/h (59 kts) – best glide.
2. Landing area
– SELECT (consider altitude and wind).
3. Engine
– RESTART (if time and altitude permit), see section 3.2.4.
4. Unable to restart
– follow emergency landing procedure, see section
3.2.4 Restarting engine in flight
1. Throttle
– IDLE.
2. Fuel valves
– check OPEN.
3. Fuel level
– CHECK.
4. Ignition
– ON.
5. Master key
– turn to START.
3.2.5 Emergency landing without engine power
1. Airspeed
– 110 km/h (59 kts) – best glide.
2. Flaps
– position 1.
3. Ignition
– OFF.
4. Fuel valves
– CLOSE.
5. Landing area
– SELECT, consider altitude and wind. (No place suitable for landing – use
recovery system.)
6. Emergency call
– TRANSMIT (121.5 MHz or nearest airfield frequency).
7. Flaps
– EXTEND FULLY on final.
8. Landing
– in the SELECTED place, avoid colliding with obstacles.
9. Touchdown
– at minimum speed.
3.2.6 Precautionary landing with engine power
(In case of decision to discontinue the flight with engine running)
1. Airspeed
– SELECT SAFE for the particular situation.
2. Throttle
– SET to maintain selected airspeed.
3. Fuel
– CHECK level and valves.
4. Map
– CHECK for nearest airfields/area suitable for landing.
5. Landing area
– SELECT.
6. Radio
– REPORT decision to land on the selected place if necessary.
7. Landing
– follow NORMAL or SHORT-FIELD landing procedure as appropriate.