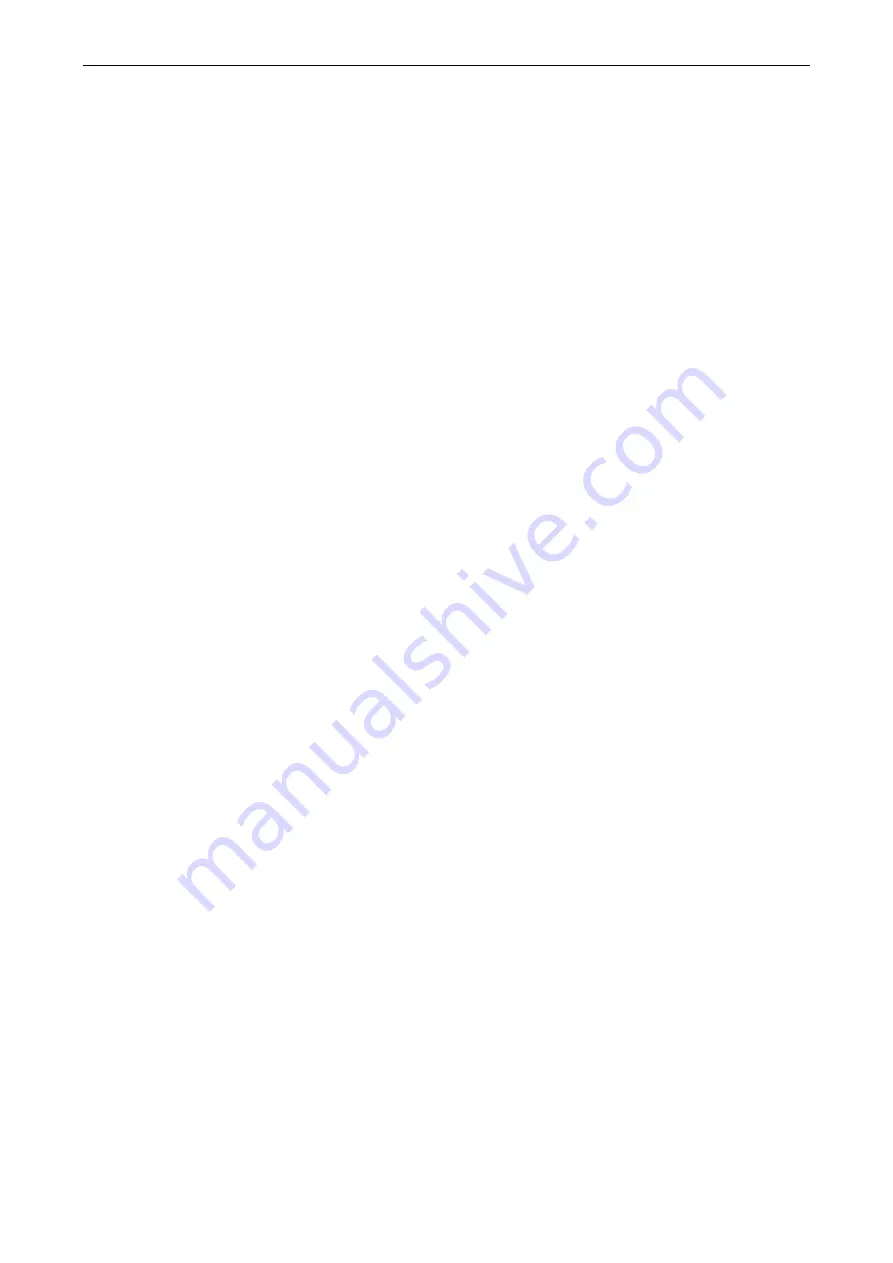
AEROPRAKT-32 Pilot Operating Handbook
A32-iS-129-POH
12
3.2.3.2 in level flight
1. Airspeed
– 110 km/h (59 kts) – best glide.
2. Landing area
– SELECT (consider altitude and wind).
3. Engine
– RESTART (if time and altitude permit), see section
4. Unable to restart
– follow emergency landing procedure, see section
3.2.4 Restarting engine in flight
1. Throttle
– IDLE.
2. Fuel level
– CHECK.
3. Fuel valves
– BOTH OPEN.
4. Fuel pump 1
– ON and 2 – OFF.
5. Lane A and B
– CHECK ON.
6. EMERGEN POWER switch
– ON.
7. START button
– PRESS until engine start (maximum 10 seconds).
8. Fuel pump 2
– ON.
9. Throttle
– AS REQUIRED.
10. EMERGEN POWER switch
– OFF (if engine runs smoothly and at least one of the Lane
A or Lane B warning lights is not permanently ON).
11. EMS lamps A and B ON
– perform PRECAUTIONARY LANDING see section
3.2.5 Emergency landing without engine power
1. Airspeed
– 110 km/h (59 kts) – best glide.
2. Flaps
– position 1.
3. Fuel pumps 1 and 2
– OFF.
4. Fuel valves
– CLOSE.
5. Landing area
– SELECT, consider altitude and wind. (No place suitable for landing – use
recovery system.)
6. Emergency call
– TRANSMIT (121.5 MHz or nearest airfield frequency).
7. Flaps
– EXTEND FULLY on final.
8. Landing
– in the SELECTED place, avoid colliding with obstacles.
9. Touchdown
– at minimum speed.
3.2.6 Precautionary landing with engine power
(In case of decision to discontinue the flight with engine running)
1. Airspeed
– SELECT SAFE for the particular situation.
2. Throttle
– SET to maintain selected airspeed.
3. Fuel
– CHECK level and valves.
4. Map
– CHECK for nearest airfields/area suitable for landing.
5. Landing area
– SELECT.