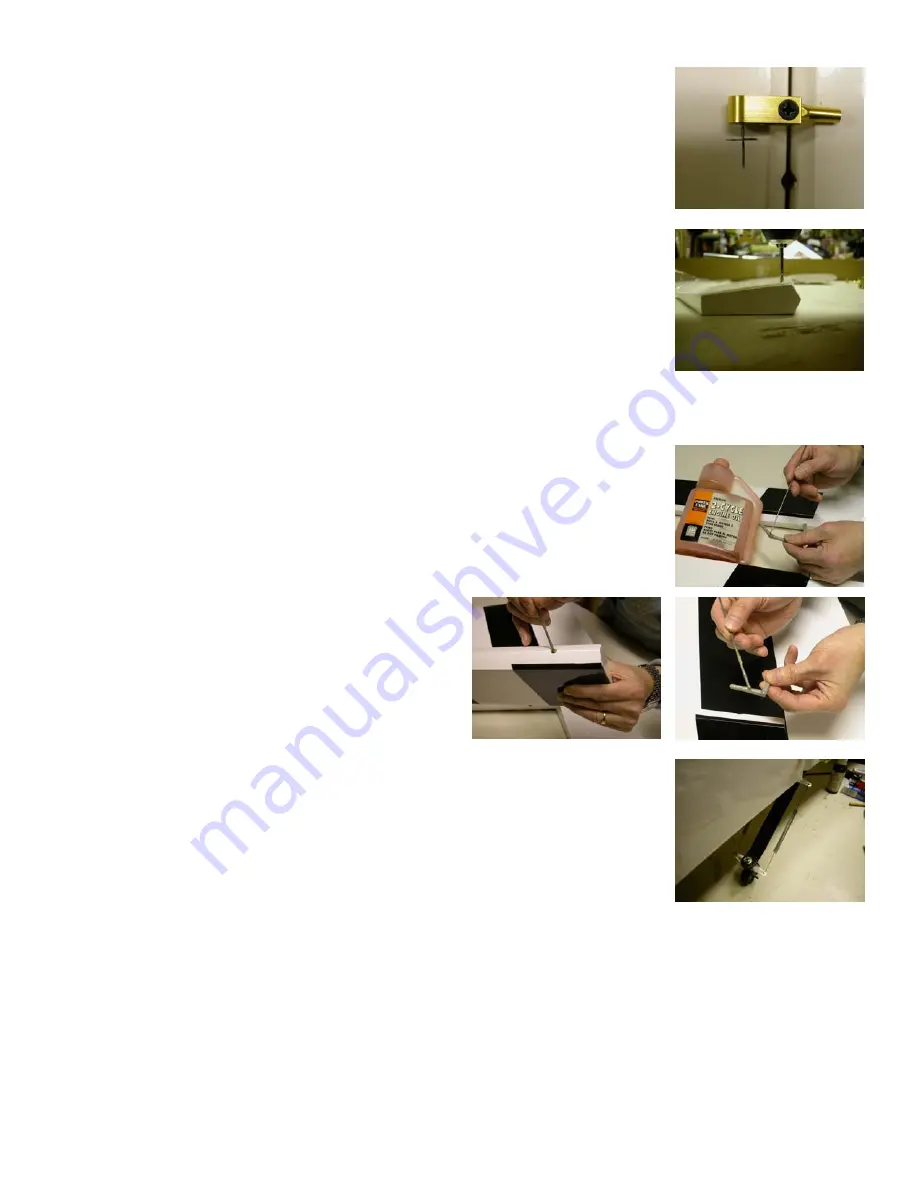
13
Next, you will need to drill holes for the aluminum M4 bolts in the control
surfaces. Locate the 5/8th hardwood dowel mounting locations for each
control surface. This can be accomplished using your covering iron as
mentioned in chapter 2.
Using the bottom of the control surfaces, measure how far back to place
your bolt in order to keep the clevis pivot point on the hinge line. Also
make sure that you are center of the hardwood mounting location and mark
the location and center punch the location. Repeat this step for all the
control surfaces except for the rudder.
Drill a vertical hole from the bottom in each of the control surface ensuring
with the top of the surface flat on your work surface.
For the rudder,
measure how far back to place your bolt in order to keep the
clevis pivot point on the hinge line. Measure half the width on the leading edge of the control surface
just in front of the horn location and place it flat on your drilling surface. Raise the trailing edge of the
surface the same distance to achieve a vertical entry for your drill bit. Drill
a hole in each of the control surfaces ensuring the hole is perfectly vertical.
Now were going to prep the hinges for installation. Take a small drop of oil
and place it in each of the pivot points of your hinges. The oil prevents
excess epoxy from bonding the joint.
Working with one panel and control surface at a time, apply epoxy into the
hinge holes of the trailing edge hinge line.
Apply epoxy to one side of the hinges and insert
them into the holes. Apply epoxy into the
leading edge holes of the control surface and the
other side of the hinges.
Carefully insert the control surface into the
hinges and butt the two surfaces together. Move
the surface up and down a couple of times to make sure all the hinges are
aligned correctly and the desired throw is attained. 35 degrees for ailerons
and 45 degrees for all others.
Use some masking tape to hold the surfaces together and let cure for at least
eight hours. Repeat this step until all of the surfaces are epoxied in place.
Install the tiller springs you set aside in chapter 2 to the tiller horn and tiller.
Tip#5 Optional step. After your epoxy has cured, it would be a good time to seal all of your hinge gaps prior
to installing you hardware. This can provide you with a better flying aircraft by increasing control surface
performance and preventing possible flutter. Clear or matching covering material can be ironed in place to
fill any gaps on the bottom of your control surfaces.
Take approximately a one-inch strip of covering the length of your surface. Fold it in half while placing into
the gap with the control surface fully deflected up and iron it in place. Check to make sure you still have full
surface travel once you have completed.