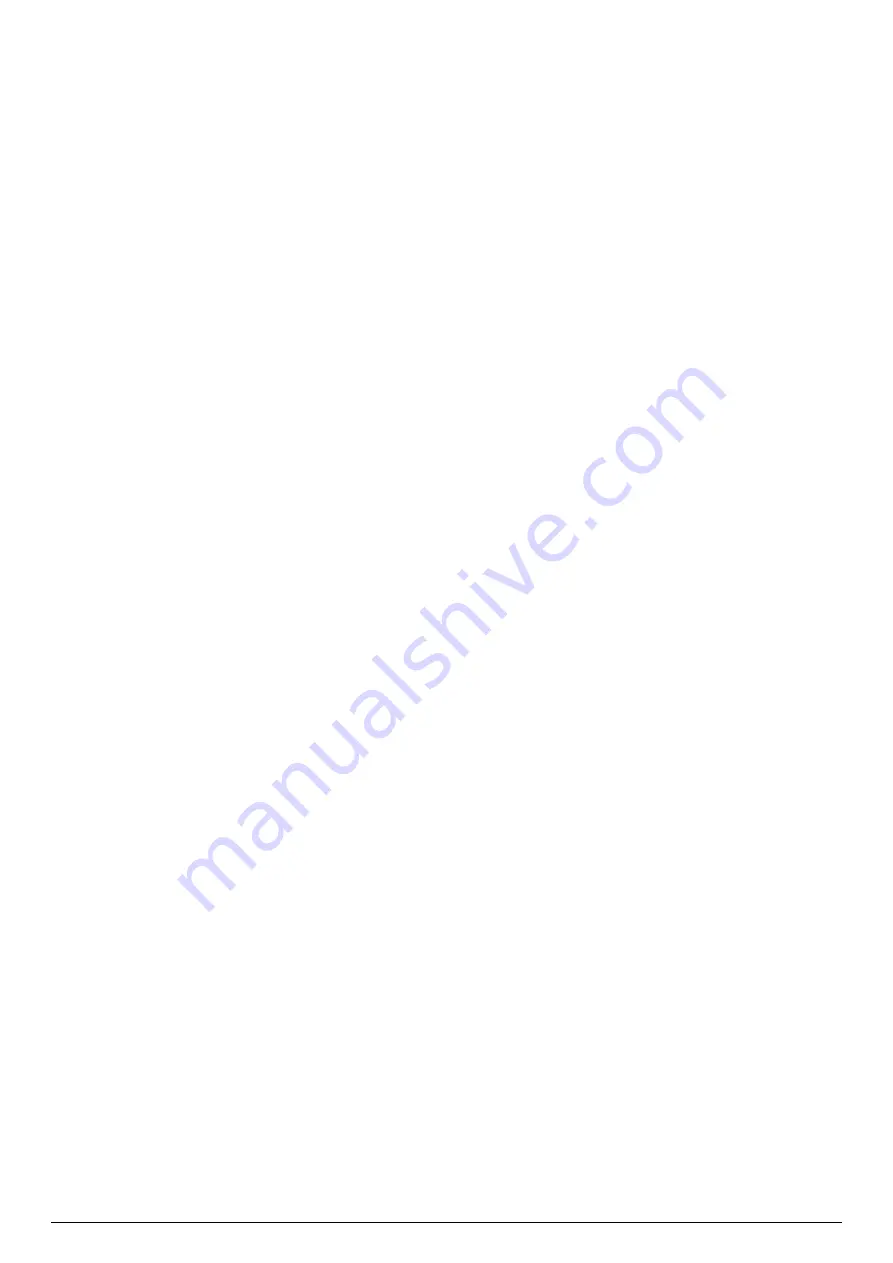
22.05 – 5890720_04
7
22.05 – 5890720_04
7
3
UNIT COMPONENTS DESCRIPTION
REFRIGERANT CIRCUIT
Compressors
High-efficiency scroll hermetic compressors with 2-pole electric motors. All the
compressors are equipped with inner electronic thermal protection device.
System side heat exchanger
Brazed plate heat exchanger in stainless steel. It is externally insulated with closed
cell neoprene anti-condensation material.
Source side heat exchanger
Brazed plate heat exchanger in stainless steel. It is externally insulated with closed
cell neoprene anti-condensation material.
Filter drier
Sight glass
It is used to verify that the expansion system is powered correctly and the presence
of humidity in the cooling circuit.
Mechanic thermostatic valve
The mechanical type valve, with external equaliser located at the evaporator outlet,
modulates the flow of refrigerant into the evaporator based on the load and en-
sures the correct superheat of the suction gas.
Electronic thermostatic expansion valve
Compared with a mechanical thermostatic valve, the electronic one offers better
overheating control so the evaporator is used more efficiently in all conditions,
thereby boosting machine output.
Its use in comfort dedicated applications allows to make substantial benefits espe-
cially in the presence of varying loads, because it allows you to maintain the maxi-
mum efficiency with any external air temperature.
In industrial applications, where there is often a need to make temperature changes
in a wide range of environmental conditions, the use of the electronic valve is ideal
because it avoids the need for continuous calibration, adapting the system to dif-
ferent load conditions and hence making it independent.
One-way valve
They allow one-way flow of the refrigerant.
Reversing valve
4-way cycle inversion valve. Reverses the refrigerant fluid flow.
HYDRAULIC CIRCUIT (VERSIONS WITHOUT HYDRONIC KIT)
Water filter
Equipped with steel filtering mesh, it prevents the heat-exchanger from clogging
system side due to any impurity inside the circuit.
Flow switch
Checks that water is circulating in the heat exchanger, and stops the unit if this is
not the case.
Pressure relief valve
Calibrated at 6 Bar and drain pipe, it activates by discharging overpressure if abnor-
mal pressure occurs.
Drain valve
HYDRAULIC CIRCUIT (VERSIONS WITH HYDRONIC KIT)
Pump
They provide useful static pressure to the system, excluding the unit pressure drops.
Expansion vessel
Membrane type precharged with nitrogen.
CONTROL AND SAFETY COMPONENTS
High pressure switch
With fixed calibration, placed on the high pressure side of the cooling circuit, it in-
hibits the operation of the compressor if abnormal work pressure occurs.
High pressure transducer
Placed on the high pressure side of the cooling circuit, signals the work pressure to
control board, generating a pre-warning in case abnormal pressure occurs.
Low pressure transducer
Placed on low pressure side of cooling circuit, it signals the work pressure to the
control board, generating a pre-warning in case abnormal pressure occurs.
ELECTRICAL CONTROL AND POWER PANEL
Complete with:
— door lock main isolating switch,
— magnetothermic switches and meters for compressors;
— phase sequence control,
— terminals for the connection with the remote keypad (OPTIONAL),
— terminals for remote alarm signals,
— clamps for signalling compressor switch-on status,
— terminals for boiler / heaters signal input,
— terminals for differential pressure switch alarm signal,
— electronic control µPC,
— control circuit numbered cables,
— terminals for 3-way valve,
— 0-10V terminals for modulating valve control
Door interlocked isolator
Access to the electrical panel is by operating the handle of the door interlocked
isolator which removes power to the unit.
When the electrical panel is closed, this lever can be locked - using one padlock or
more - during maintenance to prevent the machine being powered up accidentally.
Control panel
Allows complete control of the unit.
For further information refer to the user manual.
Electronic controller μPC
The device is the new controller for the management of the reversible water-cooled
units; the new PGD1 8-row display guarantees clear reading, with the icons show-
ing how the machine is operating.
Some entries are password protected and only available to the service technician.
The electronics also include a series of protection algorithms aimed at preventing
any damage to the main system components.
List of functions
Main functions:
1.
Parametrization of the compressor's on/off times to prevent ON/OFF cycles too
close together.
2.
To prevent any risk of the plate heat exchanger breaking due to the water
freezing, it contains 3 anti-freeze liquids (geothermal, system and zones). In
addition, the microprocessor stops the compressor if the temperature detect-
ed by the exchanger output probe is lower than the set antifreeze value.
3.
Water flow rate alarm activated by the differential pressure switches fitted as
standard.
4.
Condensation control managed through the speed modulation of the circulat-
ing pumps with phase cut or inverter, two-way modulating valve, pump ON/
OFF systems.
5.
“Chiller” water set-point compensation for external temperature.
Additional functions:
— Management of an external integration resource dedicated to the domestic
water heater.
— System management with heat pump and boiler.
— Anti-Legionella cycle.
— Time slots for the daily/weekly programming.
—
Temperature control
: temperature regulation is based on the delivery water
from the system.
—
System side circulating pump
: the electronic board has an output to manage
the circulating pump - always ON in COOLING and HEATING mode, and OFF with
a 1-minute delay after unit switch-off (standby).
—
Source side pump
: the electronic board has an output to manage the source
side pump (refer to the configurator for the available pumps). The source side
pump is turned on before the compressor is started and turned off about 30
seconds after it is turned off.
—
Antifreeze alarm
: the antifreeze function is only active when the unit is
switched on or in standby. To prevent any risk of the plate heat exchang-
er breaking due to the water inside it freezing, the microprocessor stops the
compressor if the temperature detected by the exchanger output temperature