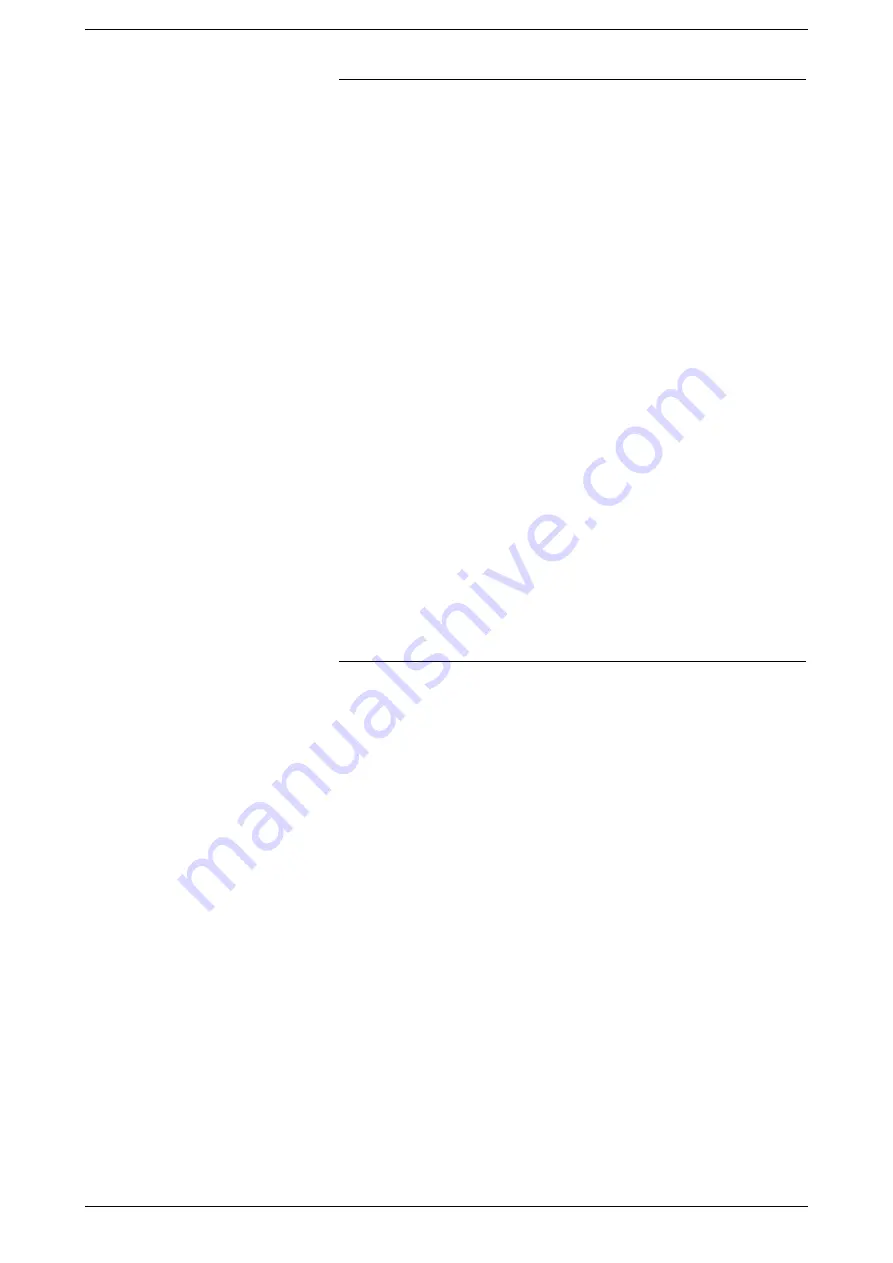
47
27. MAINTENANCE
NOTE
All routine and special maintenance
operations must be carried out exclu-
sively by qualified staff.
Before starting any servicing opera-
tion or cleaning, be sure to discon-
nect the power supply to the unit.
All appliances are subject to inevitable
wear and tear over time.
Maintenance makes it possible to:
−
Maintain the efficiency of the unit
−
Reduce the speed of deterioration
−
Collect information and data and
understand the status of efficiency
of the unit in order to prevent possi-
ble breakdowns.
IT IS therefore fundamental to envision
periodical controls::
• YEARLY
• SPECIAL
CASES
Keep a maintenance log on the machi-
ne (not supplied with the unit, the user's
responsibility) that enables you to keep
track of the servicing carried out on
the unit. This makes it easy to organise
the work appropriately and facilitates
troubleshooting on the machine.
In the log, record the date, type of work
carried out (routine maintenance, in-
spection, or repair), a description of the
work, any measures taken, and so on…
•
Yearly checks
Cooling circuit
−
Verify the watertight integrity of the
cooling circuit and that the pipes
have not been damaged.
−
Perform an acidity test on the oil of
the cooling circuit.
−
Verify the operation of the high and
low pressure pressure switches; in
the event of poor operation, repla-
cement is recommended.
−
Check the status of furring on the
dehydrator filter; replace the filter
if necessary.
•
Electric controls
−
Check the condition of the electri-
cal wires and their insulation.
−
Verify the functioning of the resi-
stance of the evaporator and of the
compressor sump.
•
Mechanical checks
Check the tightness of the screws on
the fan grids and on the fan bodies, the
compressors and the electric box, as
well as the exterior panelling of the unit.
Incorrect fastening can lead to anoma-
lous noise and vibrations.
Check the condition of the structure.
If there are any oxidised parts, treat
with paint suitable to eliminate or redu-
ce oxidation.
•
Hydraulic controls
−
Clean the water filter
−
Bleed the air from the circuit.
−
Verify that the water flow rate to
the evaporator is always constant.
−
Verify the status of the thermal in-
sulation of the hydraulic piping
−
Where envisioned, check the
percentage of glycol.
28. DISPOSAL
28.1. DISCONNECTING THE UNIT
The unit must be disconnected by a
qualified technician.
Before disconnecting the unit, the fol-
lowing must be recovered, if present:
• The refrigerant gas: the gas must be
extracted using suction devices opera-
ting in a closed circuit to ensure there
are no gas leaks into the environment.
• The glycol must not be dispersed in
the environment when removed, but
stored in suitable containers.
NOTE
The disposal of the gas refrigerant, the
glycoled water mixture where present
and the recovery of any other mate-
rial or substance must be carried out
by qualified staff in compliance with
the specific regulations in force on the
subject to prevent injury to persons or
damage to objects as well as the pollu-
tion of the surrounding area.
While waiting for disposal, the unit can be
stored outdoors, as harsh weather condi-
tions or extreme temperature changes do
not cause damaging effects on the environ-
ment provided that the electrical, cooling,
and hydraulic circuits are intact and closed.
28.2. DISMANTLING
AND DISPOSAL
In the dismantling stage, the fan, the
motor and the coil, if operational, can
be recovered by specialised recycling
centres.
NOTE
For dismantling/disposal, all the
materials must be taken to the
authorised facilities in compliance
with the national regulations in force
on this subject. For further informa-
tion on disposal, contact the manu-
facturer.
NRL_Tecnico (standard-silenziata3)_01_EN.indd 047
22/06/2009 11.47.55