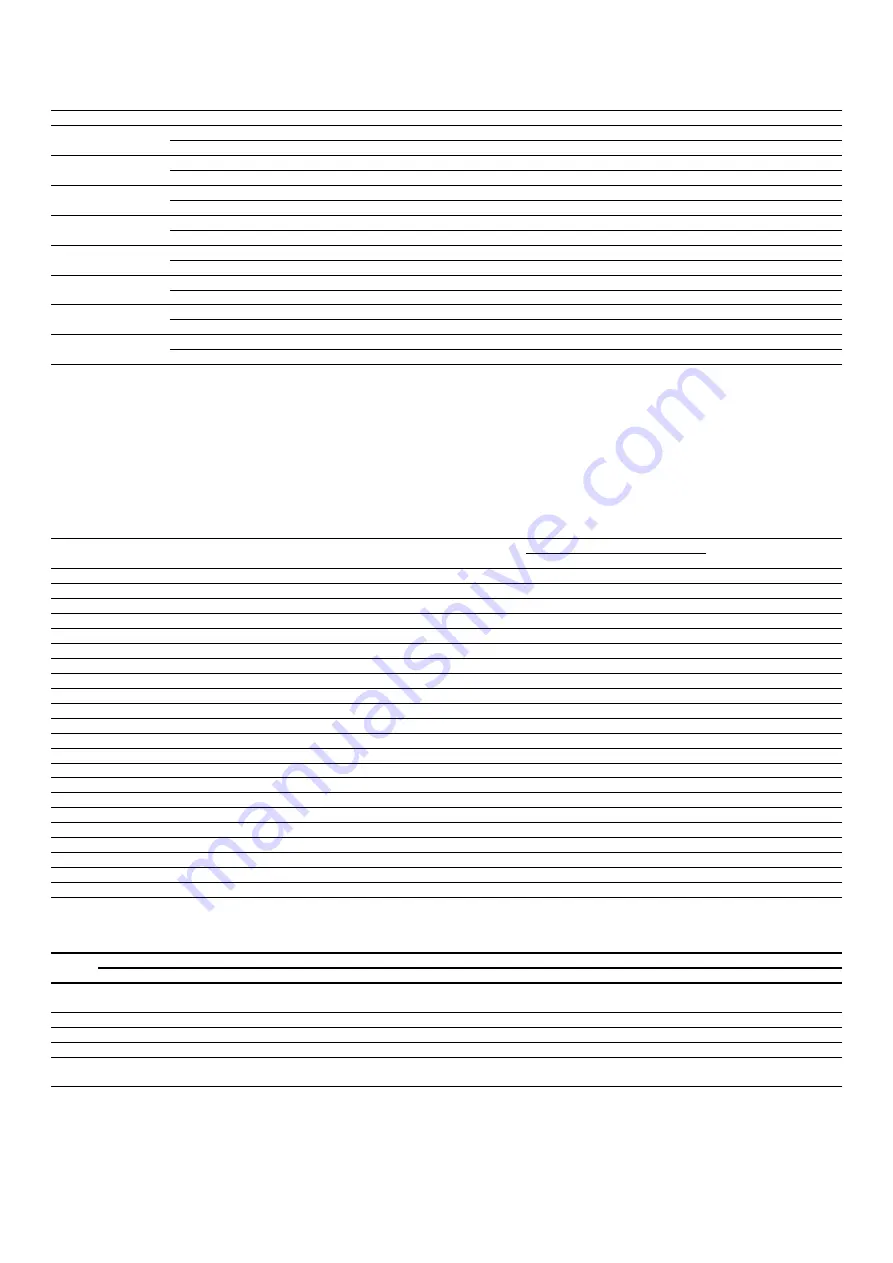
8
2.4 DIP SWITCH SETTING
The board has appropriate configuration dip-switches to meet possible installations. There are 8 microswitches with the following functions:
DIP
Position
Function
DIP 1
ON
Post-treatment resistance presence
OFF
Post-treatment resistance not present
DIP 2
ON
Pre heating resistance presence
OFF
Pre heating resistance not present
DIP 3
ON
Post-treatment coil presence
OFF
Post-treatment coil not present
DIP 4
ON
Recovery unit with heating coil + cooling coil
OFF
Recovery unit with heating/cooling coil
DIP 5
ON
Freecooling through alternation of the air flow
OFF
Freecooling through bypass damper
DIP 6
ON
Freecooling differential with 5°C hysteresis
OFF
Freecooling differential with 2°C hysteresis
DIP 7
ON
Differential pressure switches present
OFF
Differential pressure switches not present
DIP 8
ON
Activation differential according to 3°C electric load
OFF
Activation differential according to 2°C electric load
2.5 SUPERVISION SERIAL
This adjustment standard requires the management of the RS485 serial with which they can be connected as slave to a modbus network. The communication parameters are:
— Modbus RTU
— Baud Rate 19200 bit/s
— Stop bits 2
— No Parity
The following modbus data can be read/written by a supervision system:
LABEL
DESCRIPTION
CONTROLS
VALUE
UNIT
TYPE
ADD
0x03
0x10
MIN
MAX
SA_BMS
Value read by the room probe
SI
NO
-200
900
°C/10
A
0
SW_BMS
Value read by the external coil water probe
SI
NO
-200
900
°C/10
A
1
SAM_BMS
Value read by the inflow air probe
SI
NO
-200
900
°C/10
A
2
SAE_BMS
Value read by the external air probe
SI
NO
-200
900
°C/10
A
3
SINT_BMS
Value read by the probe in the user interface
SI
NO
-40
500
°C/10
A
4
SETC_BMS
Cold adjustment setpoint value
SI
NO
80
330
°C/10
A
5
SETH_BMS
Hot adjustment setpoint value
SI
NO
120
400
°C/10
A
6
STATO_BMS
Machine status
SI
NO
0
1
//
A
7
MODE_BMS
Locally set functioning mode value
SI
NO
0
3
//
A
8
POW1_BMS
Fan 1 power
SI
NO
0
100
%
A
9
POW2_BMS
Fan 2 power
SI
NO
0
100
%
A
10
ALARM_BMS
Alarms found on the recovery unit + recovery unit status flag
SI
NO
0
8191
//
D
11
DIP_BMS
Dip_Switch Configuration
SI
NO
0
255
//
D
12
DIGIN_BMS
Status of digital inputs
SI
NO
0
255
//
D
13
RELE_BMS
Status of electronic board relays
SI
NO
0
255
//
D
14
ENABLE_BMS
Enabling from remote and data change flag
NO
SI
0
1
//
D
15
MODER_BMS
Remote forced mode value (1: MAN, 2:AUX, 3:AUTO)
NO
SI
1
3
//
A
16
SEASON_BMS
Remote forced season value
NO
SI
0
1
//
A
17
SET_POW1_BMS Power set for fan 1
NO
SI
0
100
%
A
18
SET_POW2_BMS Power set for fan 2
NO
SI
0
100
%
A
19
SETPOINT_BMS
Operating set point
NO
SI
80
500
°C/10
A
20
HH_FILTRO
Operating hours of filters
SI
NO
0
10000
hours
A
21
A: analogue data; D: digital data
The following table describes the digital modbus variables in detail:
LABEL
BITS DEFINITION
B1 5
B1 4
B13
B12
B11
B10
B9
B8
B7
B6
B5
B4
B3
B2
B1
B0
ALARM_BM S
NU
NU
NU
FLAG_A
F
FLAG_F
C
FLAG_RXO
N
FLAG_FOR
Z
FLAG_VEN
T
ALL_X
X
ALL_F
3
ALL_F
2
ALL_S
A
ALL_SA
M
ALL_SA
E
ALL_DM
P
ALL_DM
F
DIP_BMS
NU
NU
NU
NU
NU
NU
NU
NU
DIP7
DIP6
DIP5
DIP4
DIP3
DIP2
DIP1
DIP0
DIGIN_BMS
NU
NU
NU
NU
NU
NU
NU
NU
NU
FI
FR
FV
SP
PI
EC
CC
RELE_BMS
NU
NU
NU
NU
NU
NU
NU
NU
RL6
RL5
RL4
RL3
RL2
RL1
RL0
RL1
ENABLE_BM S
NU
NU
F_SE
T
F_V2
F_V1
F_SEA
F_M
F_A
NU
NU
NU
NU
NU
NU
NU
ENABLE
Key:
NU bit not used
ALL_DMF freecooling bypass alarm presence bit
ALL_DMP antifreezer bypass alarm presence bit
ALL_SAE external air probe alarm presence bit
ALL_SAM inflow air probe alarm presence bit
ALL_SA expelled air probe alarm presence bit