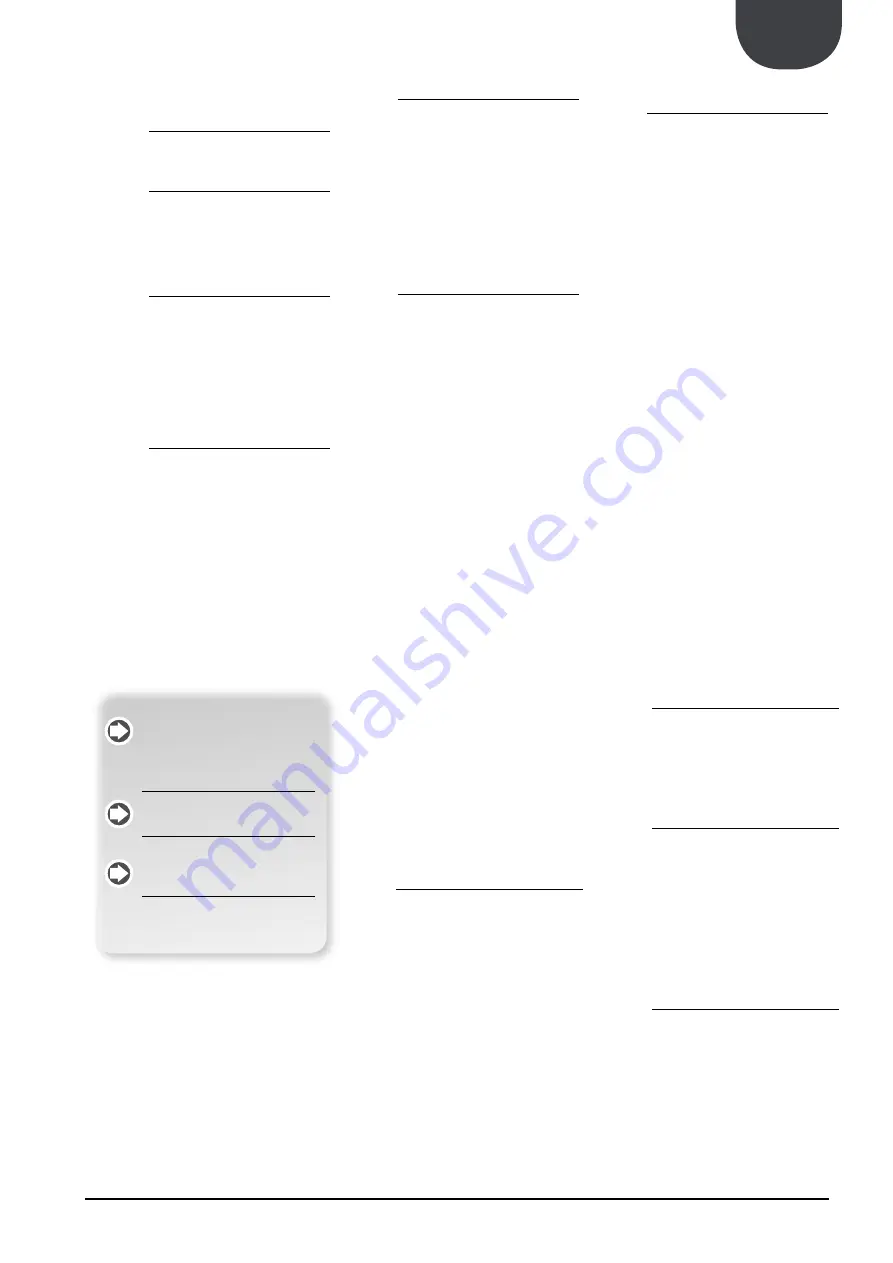
EN
11_11. 6755532_02
26. FUNCTIONING FEATURES
26.1. SET POINT IN COOLING MODE
(factory set) = 7°C, ∆t = 5°C.
26.2. SET POINT IN HEATING MODE
(factory set) = 45v, ∆t = 5°C.
If the unit power supply is restored after a tempo
-
rary interruption, the set mode will be kept in the
memory.
26.3. COMPRESSOR START-UP DELAY
Two functions have been prepared to prevent
compressor start-ups that are too close.
− Minimum time from last switch-off 180 sec
-
onds.
− Minimum time from last switch-on 300 sec
-
onds.
26.4. CIRCULATION PUMP
The circuit board envisions an output for pump
management, which starts on commissioning and
remains on for at least 150 seconds and controls the
state of the probes.
After the first 40 seconds that the pump functions,
when the water flow rate is in normal working
conditions, the water flow rate alarm functions
are activated (differential pressure switch or flow
meter).
When the machine enters stand-by mode, the
pump remains on for 30 sec and controls the flow
meter or the pressure switch
26.5. FAN SPEED CONTROL
(DCPX ACCESSORY)
To allow correct functioning of the unit at different
external temperatures, the MODUCONTROL by
reading the pressure via the pressure probe, con-
trols the rotation speed of the fans, thus allowing
to increase and/or decrease heat exchange, keep-
ing the condensation or evaporation pressures
more or less constant. The fan functions independ
-
ently with respect to the compressor.
Remember that the DCPX is mandatory for the
production of DHW
26.6. ANTI-FREEZE ALARM
The anti-freeze alarm is never active if the machine
is off or in stand-by mode. In order to prevent
breakage of the plate heat exchanger due to freez-
ing of the water it contains, the MODUCONTROL
blocks the compressor and ignition of the resist
-
ance (ACCESSORY) if the temperature detected
by the probe positioned at the outlet of the heat
exchanger and in inlet to the chiller is below +4°C.
THIS ANTI-FREEZE SET TEMPERATURE CAN ONLY
BE VARIED BY AN AUTHORISED AFTER-SALES
CENTRE AND ONLY AFTER HAVING CHECKED THAT
THERE IS ANTI-FREEZE SOLUTION IN THE WATER
SYSTEM.
The intervention of this alarm determines com
-
pressor block and not pump block, which remains
active along with the switch-on of the resistance
if installed.
To restore normal functions the temperature of
the outlet water must rise above +4°C. Rearm is
manual.
WHENEVER THIS ALARM INTERVENES, WE
ADVISE YOU CALL THE NEAREST AFTER-SALES
SERVICE IMMEDIATELY.
26.7. WATER FLOW RATE ALARM
The MODUCONTROL manages a water flow rate
alarm controlled by the differential pressure switch
installed in series on the machine.
This type of safety device intervenes after the first
40 seconds of pump functioning, if the water flow
rate is not sufficient.
The intervention of this alarm determines com
-
pressor and pump block.
WARNING
Inspection, maintenance and
eventual repair work must be car-
ried out only by a legally qualified
technician.
Lack of control/maintenance can
cause damage to persons or things.
For appliances installed near to
the sea, the maintenance intervals
must be halved.
27. MAINTENANCE
All cleaning is prohibited until the unit has been
disconnected from the electric power supply mains.
Make sure there is no voltage present before
operating.
Periodic maintenance is fundamental to keep the
unit perfectly efficient under a functional and ener
-
getic point of view.
It is therefore essential to carry out periodic yearly
controls for the:
27.1. HYDRAULIC CIRCUIT
− Refilling of water circuit
− Cleaning the water filter
− Control of flow switch
−
Bleed the air from the circuit.
− Verify that the water flow rate to the evapora
-
tor is constant.
− Verify the thermal insulation of the hydraulic
piping.
−
Check the percentage of glycol where neces-
sary.
27.2. ELECTRIC CIRCUIT CHECKS
− Safety efficiency
−
Electric supply pressure
−
Electrical Input
− Connection tightness
− Verify the operation of the carter compressor
resistance
27.3. COOLING CIRCUIT CHECKS
−
State of compressor
− Efficiency of the plate heat exchanger resist
-
ance if envisioned
−
Work pressure
− Leak test for watertightness control of the cool
-
ing circuit
− Functioning of high and low pressure pressure
switches
−
Carry out the appropriate checks on the filter
dryer to check efficiency
27.4. MECHANICAL CHECKS
− Check the tightening of the screws the
compressors and the electrical box, as well as
the exterior panelling of the unit. Insufficient
fastening can lead to undesired noise and
43
Summary of Contents for ANK030 H
Page 1: ...11_11 6755532_02 HEAT PUMPS TECHNICAL MANUAL ANK 030 045 050 H HP HA EN ...
Page 2: ......
Page 5: ......